Ingalls 39209 User Manual
Ingalls
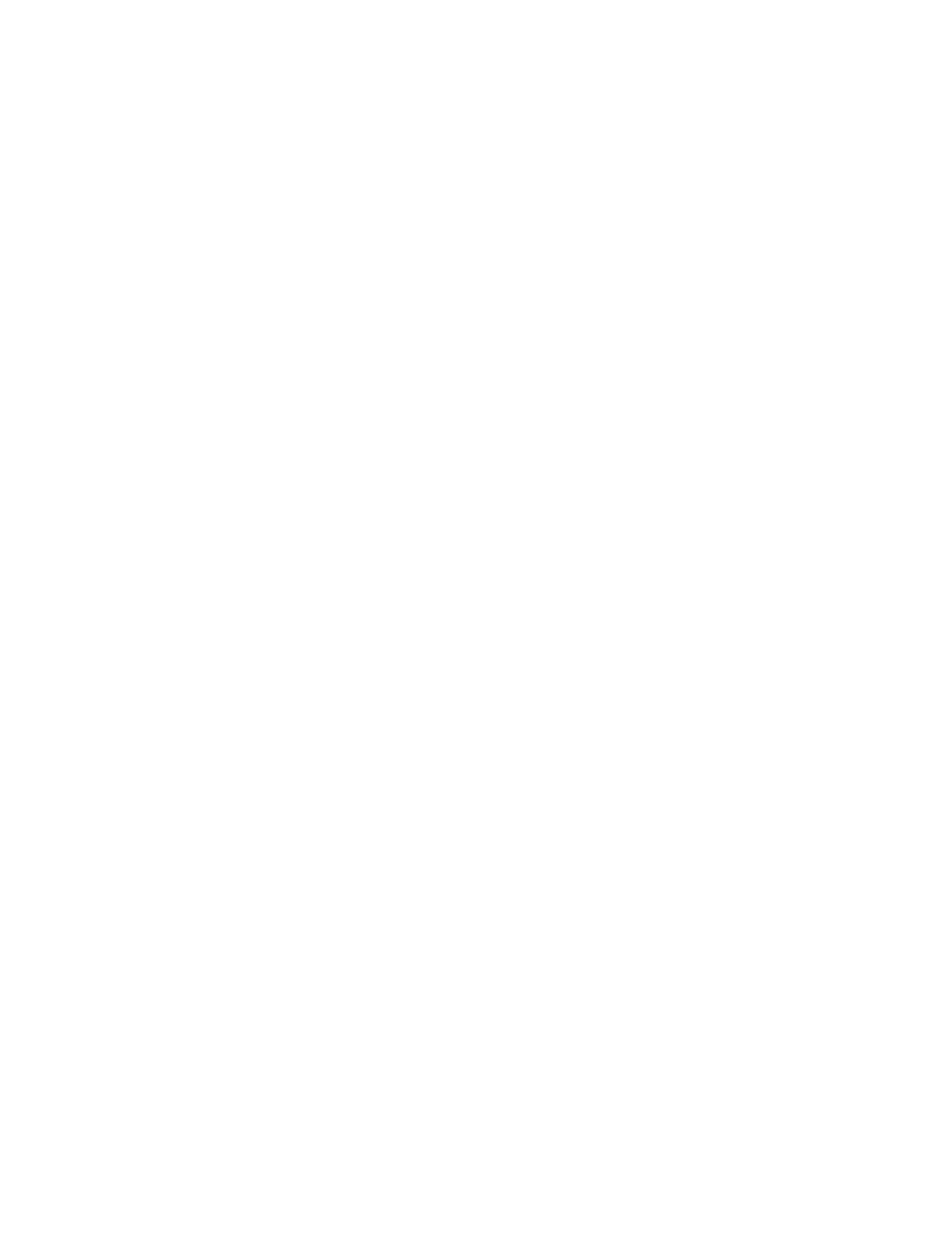
Ingalls
Product Installation Instructions
ING39200-043004
Part Number 39200 Series
CAUTION: Observe proper safety and repair procedures for installation of all chassis parts. Some chassis parts require specialized tools and
experience and therefore MUST be installed by a qualified technician otherwise an unsafe vehicle and/or personal injury could result. Wear safety
glasses and other protection.
WARNING: Before beginning, check for any damaged or loose suspension connections. Loose connections here indicate worn or broken parts which
MUST BE REPLACED. Failure to replace a damaged or worn spindle and/or link may cause the wheel to separate from the vehicle, possibly resulting in
serious personal injury.
NOTE: These parts are intended for use in vehicles with abnormal alignment and are designed to replace the non-adjustable factory equipment. These
parts are not designed for installation on vehicles with suspension and/or steering systems modified for racing, competition or any other non-standard
purpose.
Instructions
1. Before starting alignment, complete inspection checklist and determine the amount of change needed. Make sure the kit
purchased will give the correct camber adjustment needed (p/n 39201 thru 39204 give –2° to +1.75° and p/n 39205 thru 39208
give +1° to +4°).
2. Raise the front of vehicle and support body on jack stands in a safe manner. Remove front tire and wheel assembly.
3. Remove the ABS wire bracket (if equipped) from the existing control arm (carefully press out and save the stud and nut for re-
attaching the bracket to the new control arm).
4. Protect the ball joint stud threads and carefully break the taper loose (hammer blows to the side of the spindle around the taper
area will loosen the joint). Do not hit the ball joint stud. After breaking taper free, remove ball joint stud from spindle.
5. Put a tie around the upper spindle arm to keep it from extending too far out of the wheel well so the CV joint remains in place.
6. Remove the two bolts securing the OE control arm to the body. The strut spring will need to be removed or adjusted up or down as
necessary to allow the control arm bolts to be removed. Remove the control arm from the vehicle.
7. Assemble the new adjustable control arm as shown in the figure (for kits without ball joints, follow the figure instructions to use the
OE ball joint). Place the conical lock washers on the bolts with the cone ID resting under the bolt head so that the cone OD will
rest against the control arm. Place the curved bracket (with ball joint installed) under the curved section of the control arm and
thread a bolt (with washer) through each slot into the middle threaded hole on each end of the bracket.
8. Install the adjustable control arm into the vehicle in the same manner as the OE control arm. Tighten the mounting bolts to 47 ft-
lbs [64 N-m].
9. Install the new ball joint to the spindle. Torque the nut to 29-35 ft lbs (39-48 N-m) and install the cotter pin (if the cotter pin does
not line up with the hole, tighten the nut so the next slot is aligned with the cotter pin hole).
10. Using the stud and nut previously removed from the OE control arm, install the ABS wire (if present) to the adjustable control arm
in the same manner as the OE control arm and tighten the nut.
11. Re-install the tire/wheel and attach alignment equipment. Lower the vehicle to its intended ride height and adjust the front wheel
camber by sliding the ball joint to the desired position (also adjust toe as necessary). Tighten the two bolts holding the ball joint
bracket to the adjustable control arm.
12. Install two other bolts (with washers) through the control arm slots into the available threaded holes of the bracket. Tighten all four
bolts to 20 ft-lbs [27 N-m].
13. Verify camber and toe readings and check for suspension clearance as noted below. Road test and make modifications as
necessary.
ALWAYS CHECK FOR SUSPENSION CLEARANCE
Modifying any suspension component may change other part clearances and cause binding or interferences. After installing any Ingalls’ product, the
suspension must be checked for binds or interference between all components, other arms and the chassis. Be sure that all control arms, struts and
steering ends move freely through the full movement of the suspension (springs may need to be removed to fully check component travel). Installing
any Ingalls’ product on a modified vehicle (lowered or raised) from the original factory design requires a detailed check of all suspension components
and their movements. Ingalls recommends that a trained technician install all products.
Limited Warranty
Subject to Disclaimer. All Ingalls products are warranted against defects in materials and workmanship for ninety (90) days from date of purchase.
During the warranty period, Ingalls will repair, or at its option replace at no charge, components that prove to be defective. The product must be
returned, shipping prepaid, to Ingalls facility. This limited warranty does not apply if the product is damaged by accident or misuse. The foregoing
warranty is in lieu of all other warranties expressed or implied including but not limited to any implied warranty of merchantability, fitness, or adequacy for
any particular purpose or use. Ingalls shall not be liable for any special, incidental or consequential damages whether in contract, tort, or otherwise
resulting from the use or the inability to use the product.
Warranty Disclaimer
Use of this product in competition, or use on vehicles altered from original manufacturer’s specifications or settings, EXPRESSLY VOIDS WARRANTY.
The user is urged to inspect for suspension binding or interference when the product is used in these manners. However, due to the varying conditions
and manner of use which the product will be subjected to in such uses, Ingalls Engineering Co., Inc. makes no warranties, either express or implied,
including any warranty of merchantability or fitness for a particular purpose for use in competition or with specifications or settings other than those
specified by the original manufacturer’s specifications.
Copyright
©
2004 Ingalls Engineering Co., Inc.