Rainbow Electronics MAX8709 User Manual
Page 14
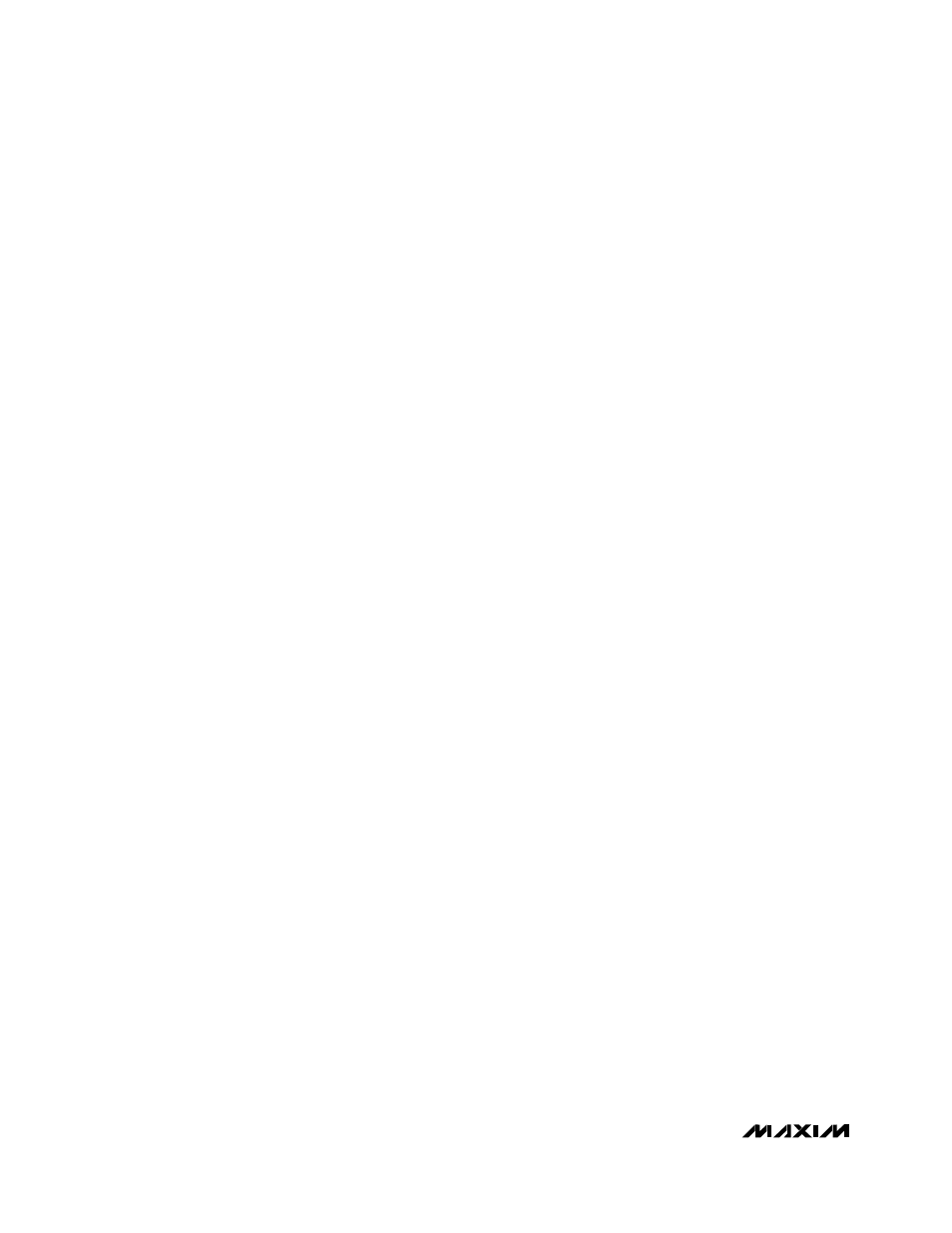
MAX8709
High-Efficiency CCFL Backlight
Controller with SMBus Interface
14
______________________________________________________________________________________
age-loop transconductance error amplifier compares
the rectified VFB voltage with a 500mV internal thresh-
old to create an error current. The error current charges
and discharges a capacitor connected between CCV
and ground to generate an error voltage V
CCV
. The
lower of V
CCI
and V
CCV
takes control and is compared
with an internal ramp signal to set the high-side
MOSFET switch on-time (t
ON
).
Lamp Startup
A CCFL is a gas discharge lamp that is normally driven
in the avalanche mode. To start ionization in a nonion-
ized lamp, the applied voltage (striking voltage) must
be increased to the level required for the start of
avalanche. The striking voltage can be several times
the typical operating voltage.
Because of the MAX8709’s resonant topology, the strik-
ing voltage is guaranteed regardless of the tempera-
ture. Before the lamp is ionized, the lamp impedance is
infinite. The transformer secondary leakage inductance
and the high-voltage parallel capacitor determine the
unloaded resonant frequency. Since the unloaded res-
onant circuit has a high Q, it is easy to generate high
voltages across the lamp.
Operation during startup differs from the steady-state
condition described in the Current and Voltage Control
Loops section. Upon power-up, V
CCI
slowly rises,
increasing the duty cycle, which provides soft-start.
During this time, V
CCV
is limited to 150mV above V
CCI
.
Once the secondary voltage reaches the strike voltage,
the lamp current begins to increase. When the lamp
current reaches the regulation point, V
CCI
exceeds
V
CCV
and it reaches steady state.
Feed-Forward Control and
Dropout Operation
The MAX8709 is designed to maintain tight control of
the transformer secondary under all transient condi-
tions including dropout. The feed-forward control
instantaneously adjusts the t
ON
time for changes in
input voltage (V
BATT
). This feature provides immunity to
input voltage variations and simplifies loop compensa-
tion over wide input voltage ranges. The feed-forward
control also improves the line regulation for short
DPWM on-times and makes startup transients less
dependent on the input voltage.
Feed-forward control is implemented by increasing the
PWM’s internal voltage ramp rate for higher V
BATT
. This
has the effect of varying t
ON
as a function of the input
voltage while maintaining about the same signal levels
at V
CCI
and V
CCV
. Since the required voltage change
across the compensation capacitors is minimal, the
controller’s response to input voltage changes is
essentially instantaneous.
To maximize run time, it may be desirable to allow the
circuit to operate in dropout if the backlight’s perfor-
mance is not critical. When V
BATT
is very low, the con-
troller loses current regulation and runs at maximum
duty cycle. Under these circumstances, a transient
overvoltage condition could occur when the AC
adapter is suddenly applied to power the circuit. The
feed-forward circuitry minimizes variations in lamp volt-
age due to such input voltage steps. The regulator also
clamps the voltage on V
CCI
. These two features togeth-
er ensure that overvoltage transients do not appear on
the transformer when leaving dropout.
The V
CCI
clamp is unique in that it limits V
CCI
to the
peak voltage of the PWM ramp. As the circuit reaches
dropout, V
CCI
approaches the PWM ramp’s peak in
order to reach maximum t
ON
. If V
BATT
decreases fur-
ther, the control loop loses regulation and V
CCI
tries to
reach its positive supply rail. The clamp on V
CCI
pre-
vents this from happening and V
CCI
rides just above
the PWM ramp’s peak. If V
BATT
continues to decrease,
the feed-forward control reduces the amplitude of the
PWM ramp and the clamp pulls V
CCI
down. When
V
BATT
suddenly steps out of dropout, V
CCI
is still low
and maintains the drive on the transformer at the old
dropout level. The control loop then slowly corrects and
increases V
CCI
to bring the circuit back into regulation.
DPWM Dimming Control
The MAX8709 controls the brightness of the CCFL by
“chopping” the lamp current on and off using an internal
DPWM signal. The frequency of the DPWM signal is
210Hz. The brightness code set through the SMBus inter-
face determines the duty cycle of the DPWM signal. A
brightness code of 0b00000 corresponds to a 9.375%
DPWM duty cycle, and a brightness code of 0b11111
corresponds to a 100% DPWM duty cycle. The duty cycle
changes by 3.125% per step, but codes 0b00000 to
0b00010 all produce 9.375% as shown in Figure 6.
In DPWM operation, the CCI and CCV control loops work
together to regulate the lamp current, limit the secondary
voltage, and control the rising and falling of the lamp cur-
rent. During the DPWM off-cycle, the output of the volt-
age-loop error amplifier (CCV) is set to 1.15V and the
current-loop error-amplifier output (CCI) is high imped-
ance. The high-impedance output acts like a sample-
and-hold circuit to keep V
CCI
from changing during the
off-cycles. At the beginning of the DPWM on-cycle, V
CCV
linearly rises, gradually increasing t
ON
, which provides
soft-start. Once V
CCV
exceeds V
CCI
, the current-loop
error amplifier takes control and starts to regulate the
lamp current. In the meantime, V
CCV
continues to rise
and is limited to 150mV above V
CCI
. At the end of the
DPWM on-cycle, the CCV capacitor discharges linearly,
gradually decreasing t
ON
and providing soft-stop.