Applications information – Rainbow Electronics MAX17031 User Manual
Page 23
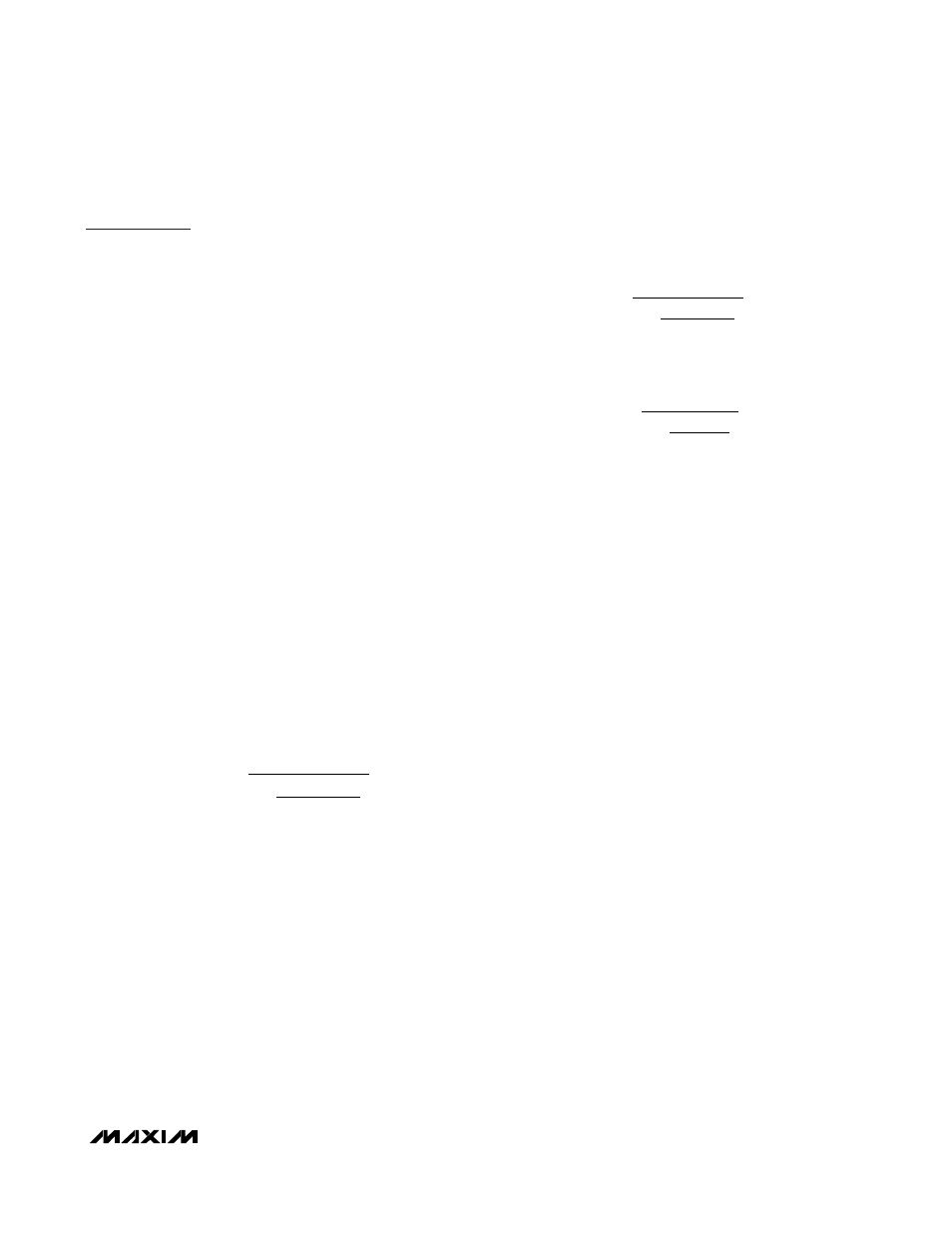
Applications Information
Step-Down Converter
Dropout Performance
The output voltage-adjustable range for continuous-
conduction operation is restricted by the nonadjustable
minimum off-time one-shot. When working with low
input voltages, the duty-factor limit must be calculated
using worst-case values for on- and off-times.
Manufacturing tolerances and internal propagation
delays introduce an error to the TON K-factor. This error
is greater at higher frequencies. Also, keep in mind that
transient response performance of buck regulators
operated too close to dropout is poor, and bulk output
capacitance must often be added (see the V
SAG
equa-
tion in the
Design Procedure
section).
The absolute point of dropout is when the inductor cur-
rent ramps down during the minimum off-time (
∆I
DOWN
)
as much as it ramps up during the on-time (
∆I
UP
). The
ratio h =
∆I
UP
/
∆I
DOWN
indicates the controller’s ability
to slew the inductor current higher in response to
increased load, and must always be greater than 1. As
h approaches 1, the absolute minimum dropout point,
the inductor current cannot increase as much during
each switching cycle, and V
SAG
greatly increases
unless additional output capacitance is used.
A reasonable minimum value for h is 1.5, but adjusting
this up or down allows trade-offs between V
SAG
, output
capacitance, and minimum operating voltage. For a
given value of h, the minimum operating voltage can be
calculated as:
where V
DROP2
is the parasitic voltage drop in the
charge path (see the
On-Time One-Shot
section),
t
OFF(MIN)
is from the
Electrical Characteristics
table,
and K (1/f
SW
) is the switching period. The absolute min-
imum input voltage is calculated with h = 1.
If the calculated V
IN(MIN)
is greater than the required mini-
mum input voltage, then operating frequency must be
reduced or output capacitance added to obtain an
acceptable V
SAG
. If operation near dropout is anticipated,
calculate V
SAG
to be sure of adequate transient response.
Dropout Design Example:
V
OUT2
= 2.5V
f
SW
= 355kHz
K = 3.0µs, worst-case K
MIN
= 3.3µs
t
OFF(MIN)
= 500ns
V
DROP2
= 100mV
h = 1.5:
Calculating again with h = 1 and the typical K-factor
value (K = 3.3µs) gives the absolute limit of dropout:
Therefore, V
IN
must be greater than 3.06V, even with
very large output capacitance, and a practical input volt-
age with reasonable output capacitance would be 3.47V.
PCB Layout Guidelines
Careful PCB layout is critical to achieving low switching
losses and clean, stable operation. The switching
power stage requires particular attention. If possible,
mount all the power components on the top side of the
board, with their ground terminals flush against one
another. Follow these guidelines for good PCB layout:
•
Keep the high-current paths short, especially at the
ground terminals. This practice is essential for sta-
ble, jitter-free operation.
•
Keep the power traces and load connections short.
This practice is essential for high efficiency. Using
thick copper PCBs (2oz vs. 1oz) can enhance full-
load efficiency by 1% or more. Correctly routing
PCB traces is a difficult task that must be
approached in terms of fractions of centimeters,
where a single milliohm of excess trace resistance
causes a measurable efficiency penalty.
•
Minimize current-sensing errors by connecting LX_
directly to the drain of the low-side MOSFET.
•
When trade-offs in trace lengths must be made, it is
preferable to allow the inductor charging path to be
made longer than the discharge path. For example,
it is better to allow some extra distance between the
input capacitors and the high-side MOSFET than to
allow distance between the inductor and the low-
side MOSFET or between the inductor and the out-
put filter capacitor.
•
Route high-speed switching nodes (BST_, LX_,
DH_, and DL_) away from sensitive analog areas
(REF, and OUT_).
A sample layout is available in the MAX17031 Evaluation
Kit data sheet.
V
=
µ
= 3.
IN(MIN)
2 5
0 1
1
1 500
3 3
.
.
.
V
V
ns
s
+
−
×
⎛
⎝⎜
⎞
⎠⎟
0
06V
V
=
µ
=
IN(MIN)
2 5
0 1
1
1 5
500
3 0
.
.
.
.
V
V
ns
s
+
−
×
⎛
⎝⎜
⎞
⎠⎟
3
3.47V
V
V
V
h t
K
IN MIN
OUT
DROP
OFF MIN
(
)
(
)
=
+
−
×
⎛
⎝⎜
⎞
⎠⎟
2
1
MAX17031
Dual Quick-PWM Step-Down Controller with Low-
Power LDO and RTC Regulator for MAIN Supplies
______________________________________________________________________________________
23