Tables, Application hints – Rainbow Electronics ADC12L038 User Manual
Page 25
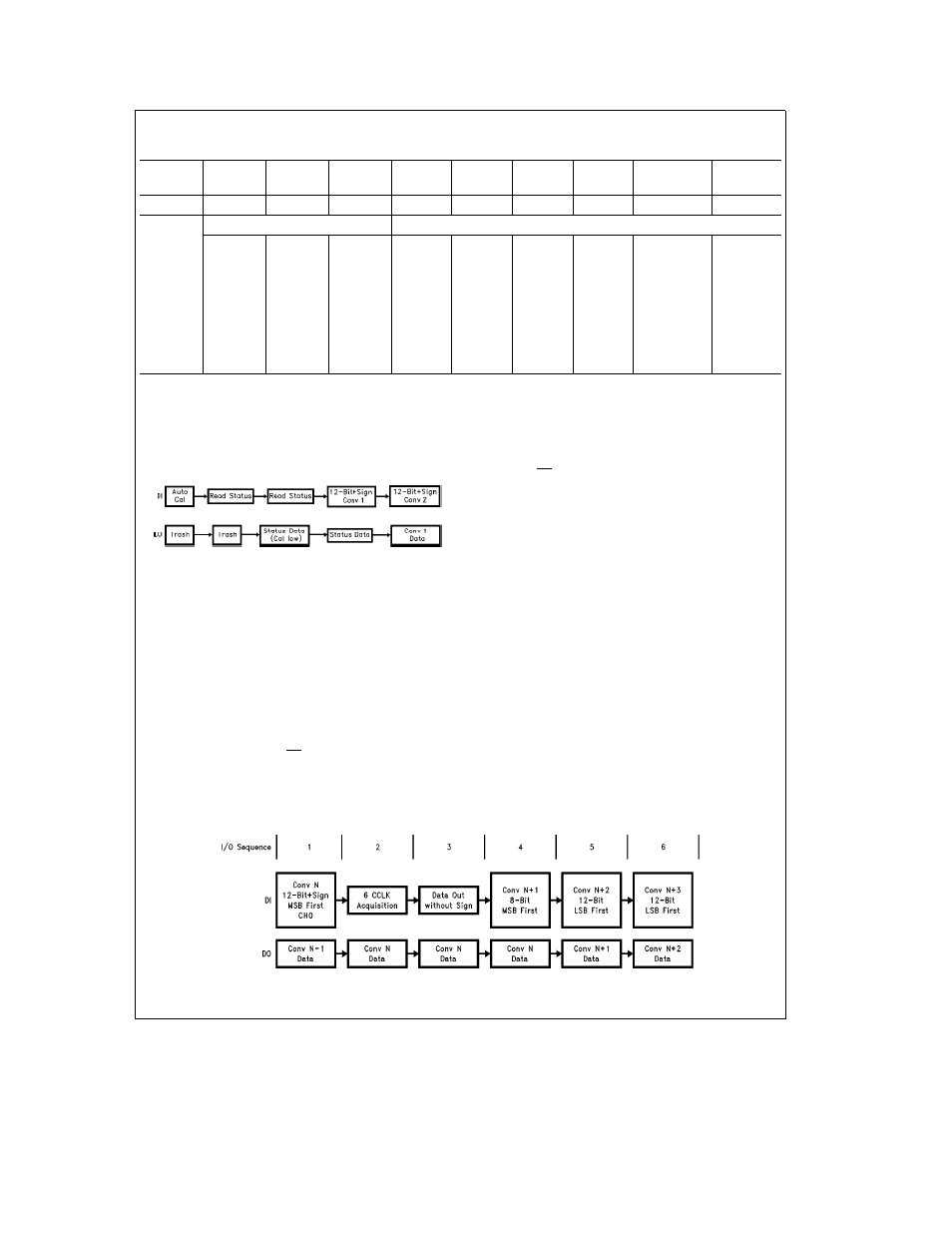
Tables
(Continued)
TABLE VII Status Register
Status Bit
DB0
DB1
DB2
DB3
DB4
DB5
DB6
DB7
DB8
Location
Status Bit
PU
PD
Cal
8 or 9
12 or 13
16 or 17
Sign
Justification
Test Mode
Device Status
DO Output Format Status
‘‘High’’
‘‘High’’
‘‘High’’
‘‘High’’
‘‘High’’
‘‘High’’
‘‘High’’
When ‘‘High’’
When
indicates
indicates
indicates
indicates
indicates
indicates
indicates
the
‘‘High’’ the
a Power
a Power
an Auto-
an 8 or 9
a 12 or
a 16 or
that the
conversion
device is in
Up
Down
Cal
bit format
13 bit
17 bit
sign bit is
result will be
test mode
Function
Sequence
Sequence
Sequence
format
format
included
output MSB
When
is in
is in
is in
When
first When
‘‘Low’’ the
progress
progress
progress
‘‘Low’’
‘‘Low’’ the
device is in
the sign
result will be
user mode
bit is not
output LSB
included
first
Application Hints
1 0 DIGITAL INTERFACE
1 1 Interface Concepts
The example in
Figure 5
shows a typical sequence of
events after the power is applied to the ADC12L030 2 4 8
TL H 11830 – 36
FIGURE 5 Typical Power Supply Power Up Sequence
The first instruction input to the A D via DI initiates Auto Cal
The data output on DO at that time is meaningless and is
completely random To determine whether the Auto Cal has
been completed a read status instruction is issued to the
A D Again the data output at that time has no significance
since the Auto Cal procedure modifies the data in the output
shift register To retrieve the status information an addition-
al read status instruction is issued to the A D At this time
the status data is available on DO If the Cal signal in the
status word is low Auto Cal has been completed Therefore
the next instruction issued can start a conversion The data
output at this time is again status information To keep noise
from corrupting the A D conversion the status can not be
read during a conversion If CS is strobed and is brought low
during a conversion that conversion is prematurely ended
EOC can be used to determine the end of a conversion or
the A D controller can keep track in software of when it
would be appropriate to communicate to the A D again
Once it has been determined that the A D has completed a
conversion another instruction can be transmitted to the
A D The data from this conversion can be accessed when
the next instruction is issued to the A D
Note when CS is low continuously it is important to transmit
the exact number of SCLK cycles as shown in the timing
diagrams Not doing so will desynchronize the serial com-
munication to the A D (see Section 1 3)
1 2 Changing Configuration
The configuration of the ADC12L030 2 4 8 on power up
defaults to 12-bit plus sign resolution 12- or 13-bit MSB
First 10 CCLK acquisition time user mode no Auto Cal no
Auto Zero and power up mode Changing the acquisition
time and turning the sign bit on and off requires an 8-bit
instruction to be issued to the ADC This instruction will not
start a conversion The instructions that select a multiplexer
address and format the output data do start a conversion
Figure 6
describes an example of changing the configura-
tion of the ADC12L030 2 4 8
During I O sequence 1 the instruction on DI configures the
ADC12L030 2 4 8 to do a conversion with 12-bit asign
resolution Notice that when the 6 CCLK Acquisition and
Data Out without Sign instructions are issued to the ADC
I O sequences 2 and 3 a new conversion is not started
The data output during these instructions is from conversion
N which was started during I O sequence 1 The Configura-
tion Modification timing diagram describes in detail the se-
quence of events necessary for a Data Out without Sign
Data Out with Sign or 6 10 18 34 CCLK Acquisition time
mode selection Table V describes the actual data neces-
TL H 11830 – 37
FIGURE 6 Changing the ADC’s Conversion Configuration
25