MSD 7761 Advance RPM Control Module Installation User Manual
Page 4
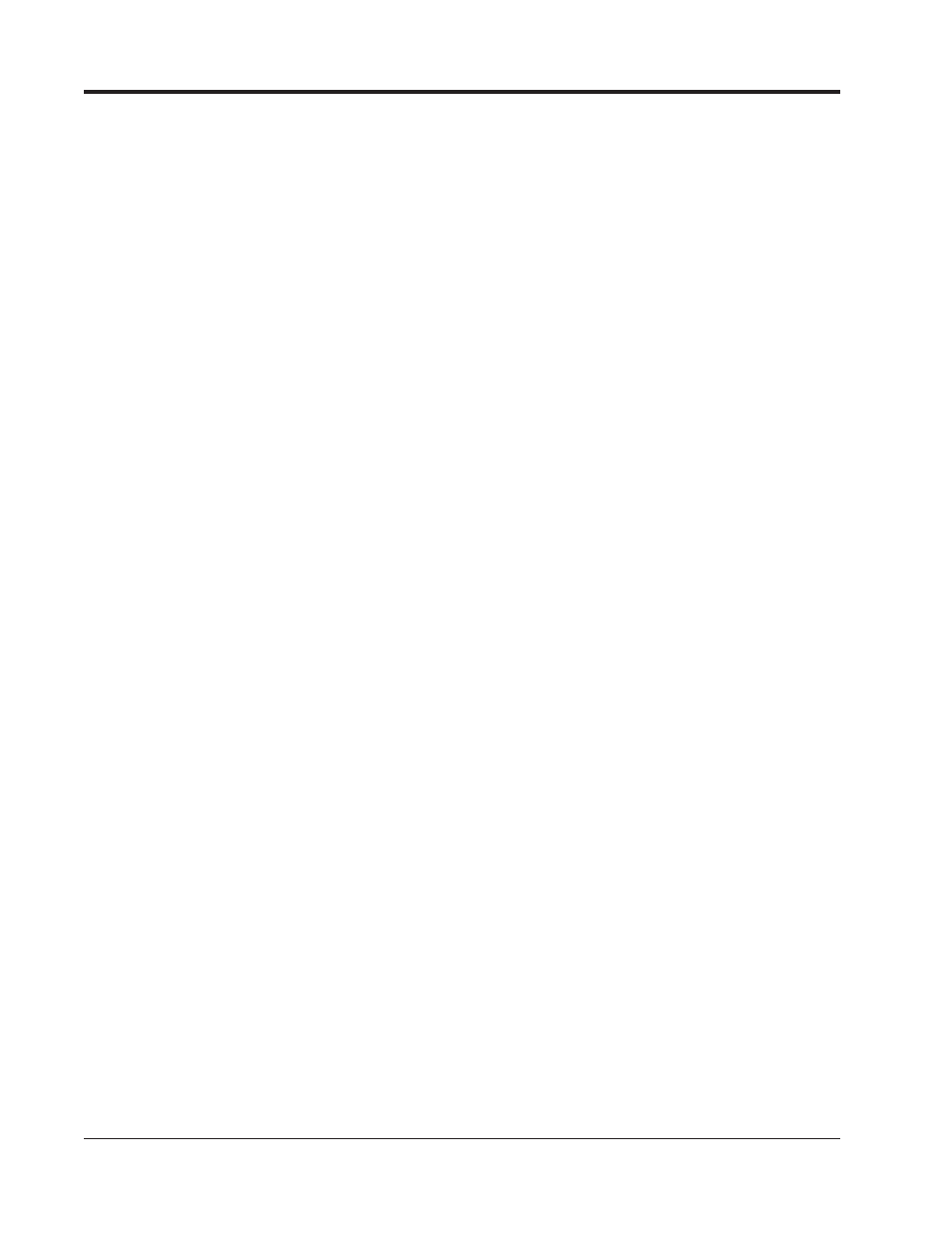
4
INSTALLATION INSTRUCTIONS
M S D
• W W W . M S D P E R F O R M A N C E . C O M • ( 9 1 5 ) 8 5 7 - 5 2 0 0 • F A X ( 9 1 5 ) 8 5 7 - 3 3 4 4
RETARD ABOVE LIMIT
The settings in this sub tab determine the amount of timing retard based on time from launch. A slope
can be set if an engine needs less timing retard further into a run. Multiple steps can be plotted to
coordinate with gear changes or nitrous events. The settings here vary depending on the application.
Two lines can be programmed. The software is designed so that the lower line will always be the
maximum timing taken out. The top line will always be the minimum timing taken out. Because of
this, it makes no difference which line is above the other.
When the driveshaft rpm is between the Retard Curves the ARC module will automatically determine
timing change. The unit calculates the amount of timing change by interpolation. By using the
calculation, the module makes it progressively harder for the engine to continue accelerating past
the desired plot.
If only one retard setting is desired – with no progressive control – then both Retard Above Limit curves
should be set identically. If one line is left at the top of the plot, the software will see the minimum
retard as zero.
CURVES
There are up to three curves to set in this tab; two Retard Curves and a single Limiter Curve. The
three lines can be combined or used individually for only retard or only limiter. Typically, one Retard
Curve will be set to follow the driveshaft rpm curve closely. The other Retard Curve will be plotted
above. The Limiter Curve is a safety by plotting above the highest Retard Curve. When driveshaft
speed exceeds the Rev Limiter Curve the ARC module will clamp the engine at the engine rpm that
was present when the driveshaft speed exceeded the plot. The engine rpm clamp will be released
after the driveshaft speed drops below the plot. Each curve set can be programmed with up to 30
points in intervals of 0.01 seconds and 1 rpm. See “Loading Curves” below for instructions to import
a driveshaft curve into this plot.
CRANK SHAFT
If settings are entered for both Driveshaft and Crankshaft the module will react accordingly for
both inputs.
Settings made to these sub tabs control the engine according to crankshaft rpm. There is sometimes
a lag between driveshaft and crank shaft inputs, this is especially true in vehicles with automatic
transmissions due to the convertor.
SLEW RATE
The ARC Module can control the engine RPM when it exceeds the pre determined acceleration.
During excessive acceleration, the ARC Module can be programmed to retard timing or to rev limit
the engine speed. MSD ReView can be used to determine the slew rate and assist in slew settings.
On the Engine RPM trace of any file within View the slew rate is calculated for the time between the
red and blue cursors. It is best to put the cursors at the top and bottom of the steepest area of a good
run to get a starting point of an engine’s slew.
A margin must be set since all RPM curves experience some variances (“wobble” - jagged lines due
to split second changes in speed). The margin programmed in RPMs allows for excessive slope in
the slew rate for a short period of time. Without the margin, or when the margin is set too low, the
module may limit the engine each time there is an upswing in the normal variance (rpm “wobble”).
If margin is too large, the slew controller will not activate early enough to control rapid acceleration.
The default Margin is set to 200 rpm.