Installation, Cable connections – Lincoln Electric IM613-B User Manual
Page 11
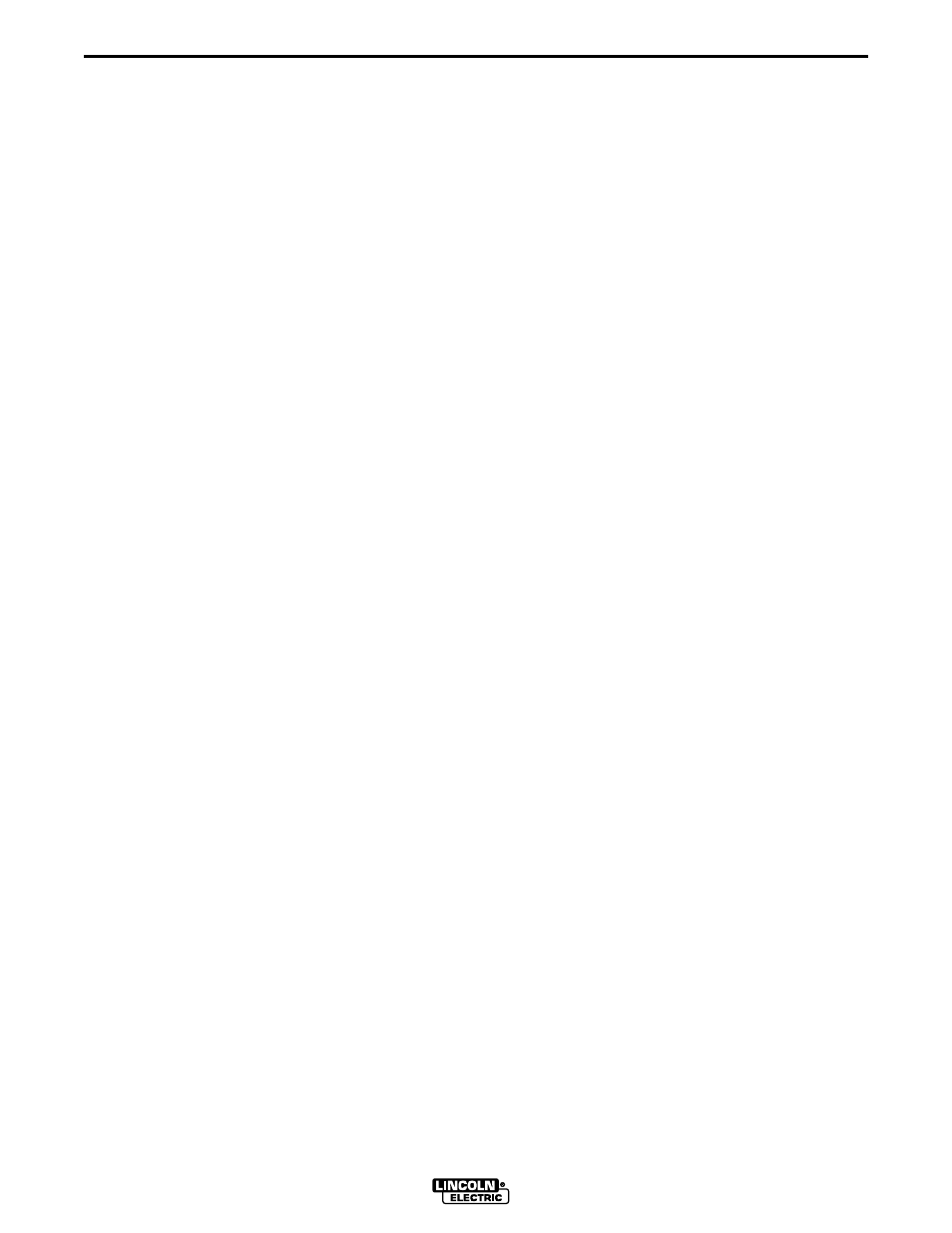
A-3
INSTALLATION
POWER FEED 11
A-3
CABLE CONNECTIONS
CONTROL CABLE CONNECTIONS
• All system control cables are the same.
• All control cables can be connected end to end to
extend their length.
• All system equipment must be connected to a con-
trol cable.
Welding systems using the Power Feed 11 offer previ-
ously unprecedented flexibility in the connection of
system components. This system uses the same type
of control cable between each of the system compo-
nents. Connections can be “daisy chained” from one
system component to another. Since communication
over the control cables is done by a robust communi-
cations network, the order of connection of the com-
ponents makes no difference. The cables can be con-
nected anywhere that there is a mating connector.
CONTROL CABLE SPECIFICATIONS
The cable is a 5 copper conductor cable in a SO-type
rubber jacket. There is one 20 gauge twisted pair for
network communications. This pair has an impedance
of approximately 120 ohms and a propagation delay
per foot of < 2.1 ns. There are two 12 gauge conduc-
tors that are used to supply the 40 VDC to the net-
work. The fifth wire is 18 gauge and is used as an
electrode sense lead. It is typically connected to the
feed plate on the feed head when that feed head is
active.
NOTE: Maximum cable length between any two
nodes is 250'.
TYPICAL CABINET FEEDER CONNECTION
The Control cable is connected from the Power
Source to the Wire Feeder. The Power Feed 11
comes standard with an 8 ft. Control Cable.
CONTROL CABLE INSTALLATION:
1. Connect the end of the control cable with the 5-pin
cable plug to the mating receptacle on the power
source. With the pins and key aligned, plug it into
the power source, rotate the threaded locking ring
until the connector is completely fastened
2. Connect the end of control cable with the 5-socket
end to the mating receptacle on the back of the
wire feeder. To connect the cable to the feeder,
aligning the pins and key, plug it into the back of
the wire feeder head, rotate the threaded locking
ring until the connector is completely fastened
Note: Depending on the location of the of the Wire
Feeder relative to the Power Source a longer
Control Cable or additional Control Cable(s) may be
required.See section 2.0 “Optional Features” for
information on optional Control Cables.
ELECTRODE CABLE CONNECTIONS
Most welding applications run with the electrode being
positive (+). For those applications, connect the elec-
trode cable between the wire feeder and the positive
(+) output stud on the power source (located beneath
the spring loaded output cover near the bottom of the
case front).
A work lead must be run from the negative (-) power
source output stud to the work piece. The work piece
connection must be firm and secure, especially if
pulse welding is planned. Excessive voltage drops at
the work piece connection often result in unsatisfacto-
ry pulse welding performance.
When negative electrode polarity is required, such as
in some Innershield™ applications, install as above,
except reverse the output connections at the power
source (electrode cable to the negative (-) stud, and
work cable to the positive (+) stud).
ELECTRODE CABLE INSTALLATION:
The Power Feed 11 comes with an installed electrode
cable. Connect the power source end of the cable to
the power source output terminal of the desired polari-
ty.
The K1636-1 Power Feed 11 (Europe) electrode cable
is equipped with a Twist-Mate™ connector while the
K1635-1 Power Feed 11 (World) is equipped with a
lug connector. Also for both models open the Wire
Drive compartment door and check that the electrode
cable lug is against the Feedplate and that the con-
nection is tight. Any electrode cable replacement or
extension should be sized according to the specifica-
tions given in the work cable connections section .