Lingenfelter L460330000 Micro Storm MS-001 2-Stage Dual Ramp Progressive Nitrous Controller v 2.6 User Manual
Page 6
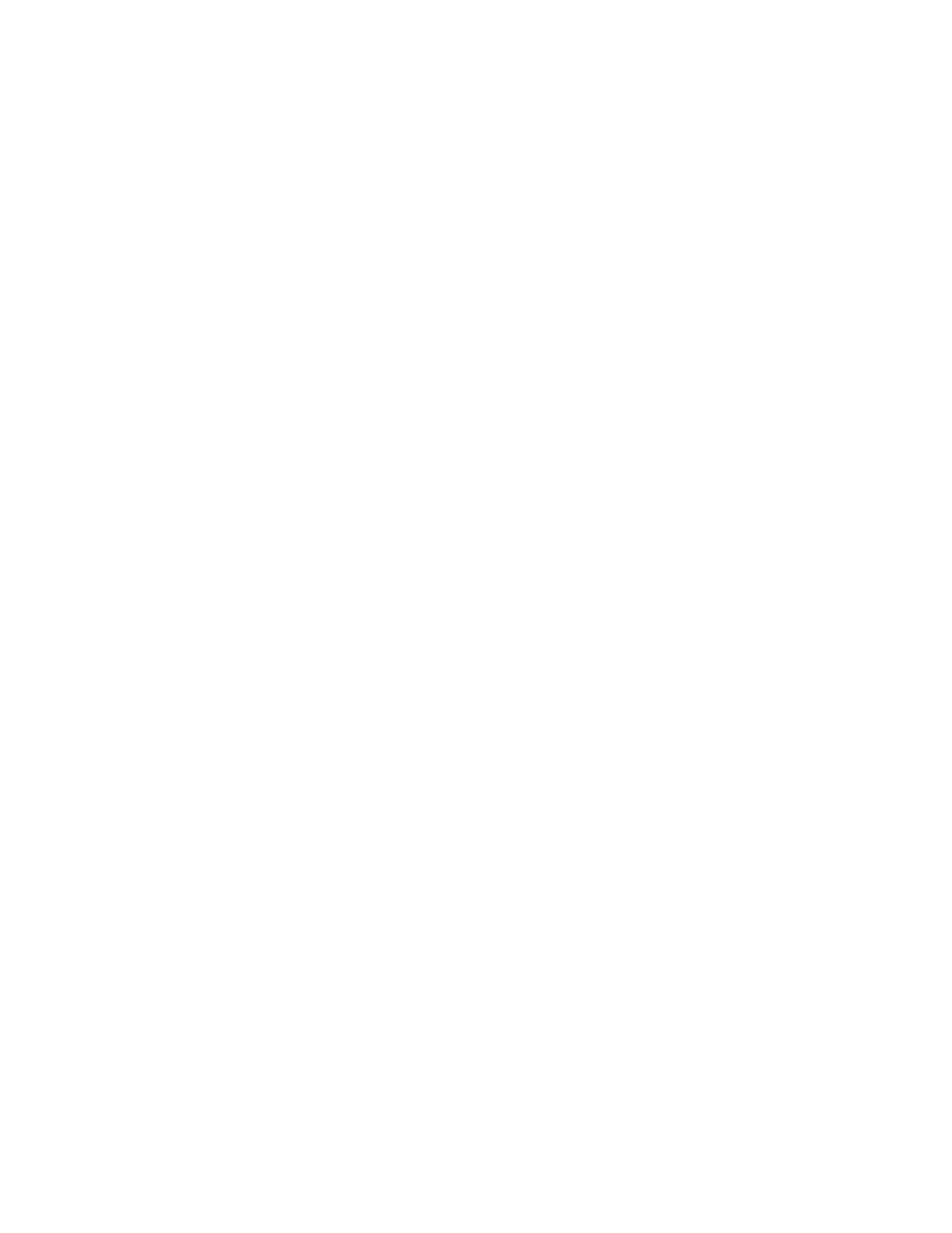
6
9—Nitrous Build Time1—Stage2: This setting controls the time it takes stage2 to go from the starting
percentage to the final percentage. The nitrous will progressively ramp from the start to final setting in the
time programmed for this parameter. A shorter time (example 0.2 second) will create a very aggressive ramp
and a longer time (example 9.9 seconds) will create a smoother application of power.
Valid range is 0.0 second to 9.9 seconds in .1 second increments.
10—Resume Mode—Hold & Wait or Reset: This setting allows the Progressive system to Hold & Wait when
the Activation signal is removed. Example - the throttle is lifted due to wheel spin or similar event. The Hold
& Wait setting allows the Progressive system to resume at the point where the throttle was lifted. If this
option is OFF the Progressive system and All Timers will reset each time the Activation is removed.
0 = Hold & Wait is OFF, Reset mode.
1 = Hold & Wait is ON.
11—Main timer period, 20 to 300 seconds: This controls the total time elapsed before a System Timeout
occurs. This limits the total amount of time the solenoids can be On if the Activation signal is never removed.
This setting also allows the system to be used with Wait & Hold option and the Progressive Timers will reset
after the Timeout Period has elapsed and the Activation signal is removed. If a reset is needed before the
timer has elapsed turn the controller off and back on. This method is by design to prevent the unit from being
inadvertently reset during operation.
Valid range is 20 to 300 seconds in 1 second increments.
12—TPS enable, use TPS signal for activation: This setting determines the activation input function. The
activation input can be configured for +12 volt activation or to read a TPS (throttle position sensor) signal.
When configured for +12 volt activation any voltage above 4.00 volts will be accepted as ON. When
configured for TPS signal the closed throttle voltage and WOT (wide open throttle) voltage will need to be
programmed for proper operation. A voltage span of at least 2.50 volts between closed and WOT throttle
position is required. An error code will be displayed on the “Ready” screen if this condition is not met.
0 = TPS enable OFF, +12 volt activation mode.
1 = TPS enable ON, must configure for proper operation.
13—TPS closed throttle volts—manual adjust: This setting is only used if TPS enable option is ON. The value
of this setting should be the closed throttle position voltage. See parameter #16 to configure using live TPS
data.
Valid range is 0.00 to 5.00 volts in .01 volt increments.
14—TPS wide open throttle volts—manual adjust: This setting is only used if TPS enable option is ON. The
value of this setting should be the WOT (wide open throttle) throttle position voltage. See parameter #16 to
configure using live TPS data.
Valid range is 0.00 to 5.00 volts in .01 volt increments.