A.4 converting measuring units – Festo Электромотор MTR-DCI User Manual
Page 133
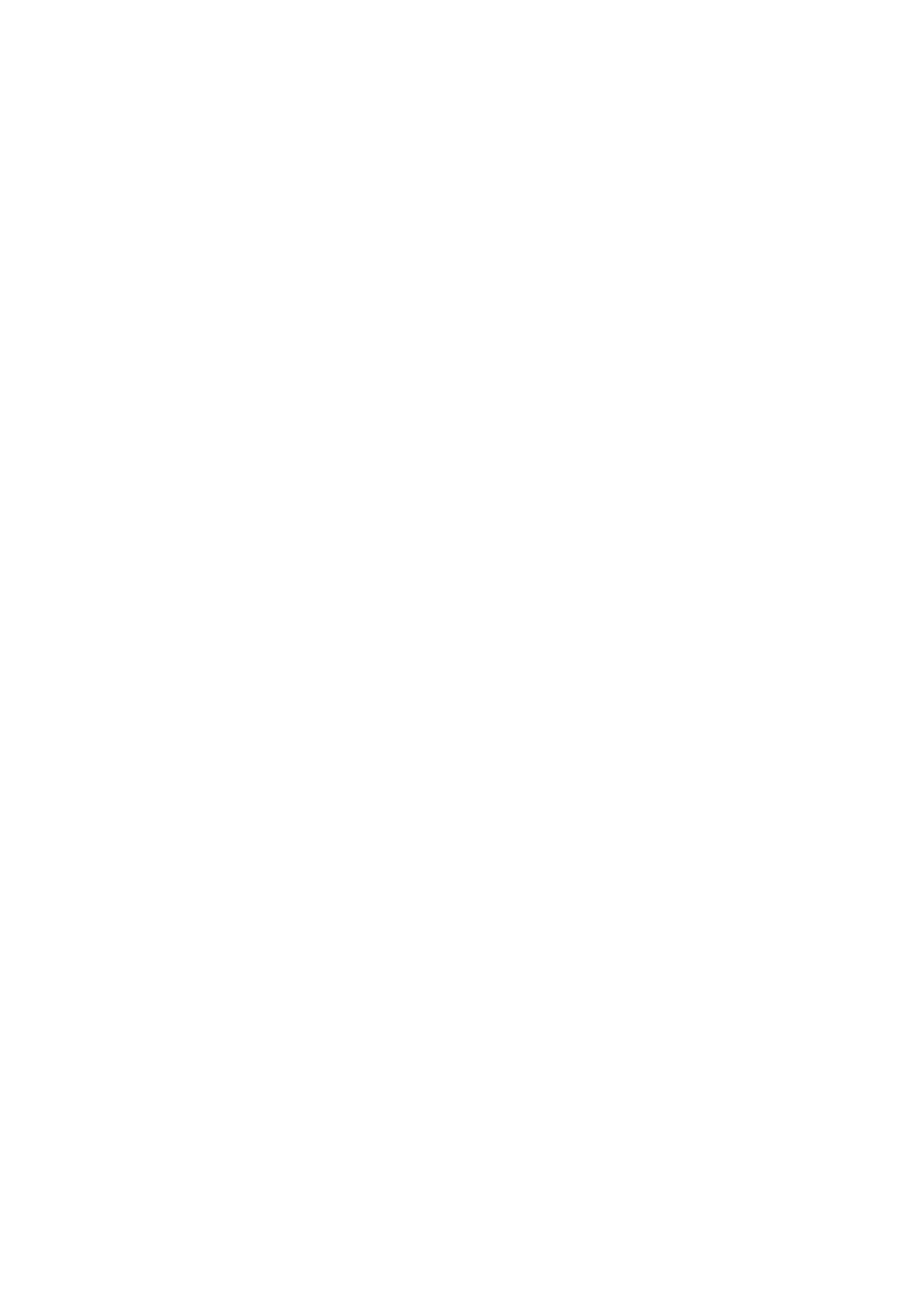
A. Technical appendix
A-13
Festo P.BE-MTR-DCI-IO-EN en 1209d
A.4
Converting measuring units
A measuring system must be defined for specifying the para-
meters of the electric axis. In order to enable simple paramet-
rizing for different application cases, the controller can be set
via the control panel or FCT so that the user can specify or
read all variables directly in the desired units on the power
take-off, e.g.:
– the metric measuring system for linear movements (mm,
mm/s, mm/s
2
)
– the angle measuring system for purely rotational move-
ments (degree, degree/s, degree/s
2
) or (rot, rot/s, rot/s
2
)
– the imperial measuring system (inch, inch/s, inch/s
2
)
Each physical variable (position, speed and acceleration) is
adapted to the relevant measuring system by means of a con-
version factor.
In the controller all parameters are always saved in increment
specifications (inc, inc/s, inc/s
2
) and are not converted until
they are written in or read. For the display, conversion from
the internal basis system into the (pre)set measuring system
takes place within the firmware; for representation on the PC
monitor within the FCT software. In this way, the user does
not need to carry out conversion when entering values or
when reading on the control panel or in the FCT.
Direct transfer of values via the serial interface with CI com-
mands always takes place in the basis system and requires
conversion into increments.
Conversion is carried out via the parameters:
– Feed constant (depending on the drive type)
– Gear reduction
– Encoder resolution = physical measuring steps per motor
revolution. For the MTR-DCI: Pulse quadruplication by di-
gital interpolation