Festo Линейный привод с датчиком перемещения DFPI User Manual
Linear drive dfpi-...-...-nd2p-c1v-...-a
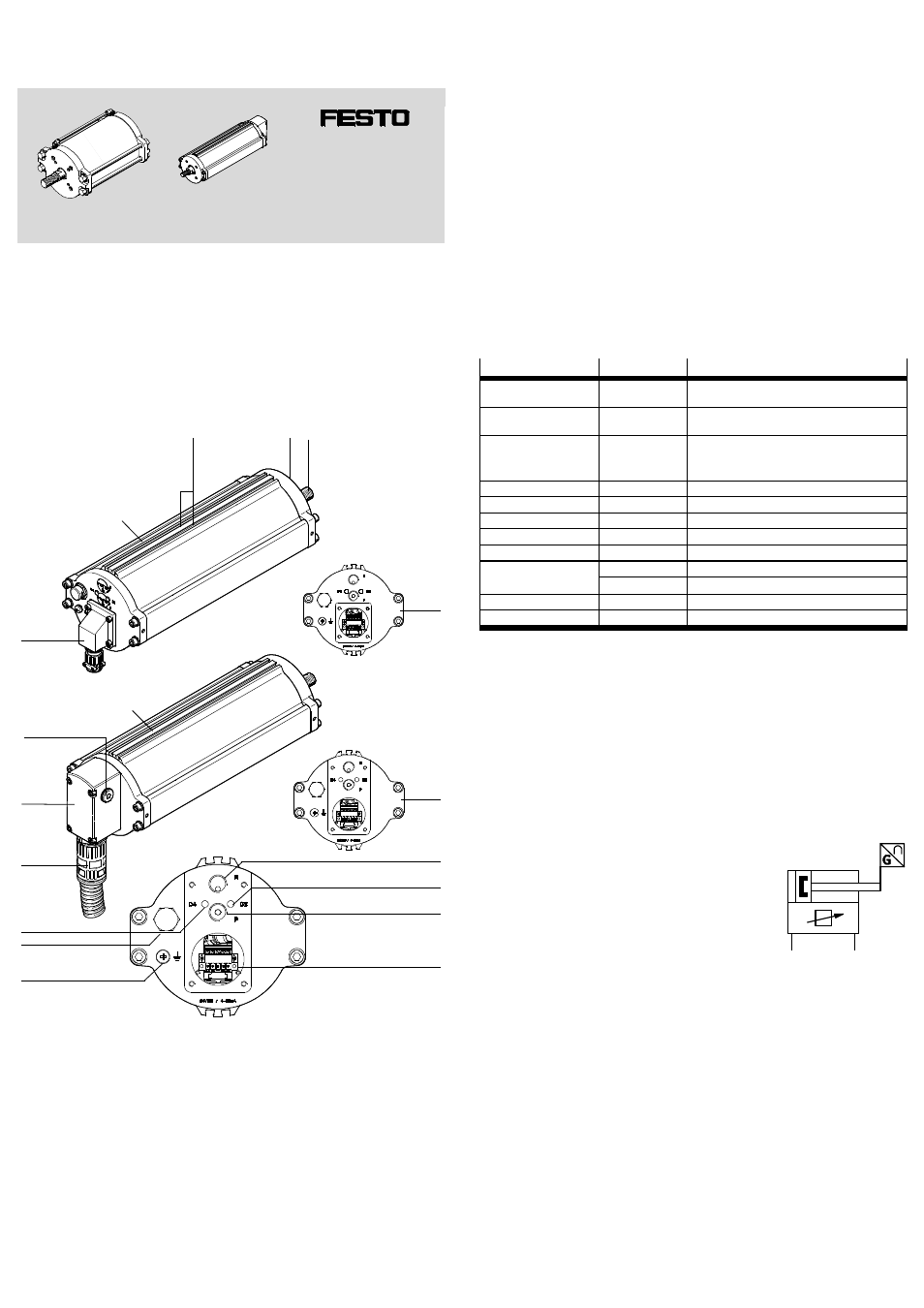
Linear drive
DFPI-...-...-ND2P-C1V-...-A
Festo AG & Co. KG
Postfach
73726 Esslingen
Germany
+49 711 347-0
www.festo.com
(en)
Operating instructions
8029184
1309a
[8029186]
Original: de
Linear drive DFPI-...-...-ND2P-C1V-...-A
English
. . . . . . . . . . . . . . . . . . . . . . . . . . . .
1
Operating elements and connections using as an example the DFPI-100-...
2
1
4
3
9
aJ
aA
aB
DFPI-...-...-ND2P-C1V-A
DFPI-...-...-ND2P-C1V-P-A
4
5
6
7
8
aC
aD
aE
1 Slot for proximity sensor
2 Mounting thread (reverse side,
Fig. 4)
3 Piston rod with mounting thread
for coupling and spanner flat for
counter holding
4 Representation without flange
receptacle
5 Pneumatic interface
*)
– channel R
(exhaust)
6 Flow control screw D2
7 Pneumatic interface
*)
– channel P
(compressed air supply)
8 Electrical connection behind the
flange receptacle
9 Earth terminal; position dependent
on piston diameter
aJ Pressure compensation element
aA Flow control screw D4
aB Optional: connecting cable with
protective conduit (accessories)
aC Flange receptacle – here
DFPI-...-...-ND2P-C1V-P-A
aD Plug screw (from factory) or filter
nipple or silencer (accessories)
aE Flange receptacle – here
DFPI-...-...-ND2P-C1V-A
*)
Pneumatic connection
Fig. 11
Fig. 1
2
Design
The DFPI-...-...-ND2P-C1V-…-A is an electro-pneumatic linear drive consisting of:
– a double-acting pneumatic cylinder with
– integrated displacement encoder (potentiometer) for determining the actual
position
– integrated valve manifold with directional control valves for controlling the pis-
ton rod
– integrated positioner for position control.
If necessary, proximity sensors can be installed in the available slots (
Fig. 1
1 )
in order to provide binary interrogation of positions.
A pressure compensation element (
Fig. 1
aJ ) prevents the formation of con-
densate inside the housing in the event of temperature fluctuations, thus protect-
ing the internal electronics.
For DFPI-...-...-ND2P-C1V-A the pneumatic connections are freely accessible (pneumatic
connection G¼). The electrical connections are protected by a flange receptacle.
For DFPI-...-...-ND2P-C1V-P-A the electrical and pneumatic connections are protec-
ted against external mechanical influences by a rugged flange receptacle. The
flange receptacle provides push-in connectors for the pneumatic system and a G¼
exhaust port for venting on site.
The product is available in various designs. These operating instructions describe
the following product variants:
Features
Type codes
Description
Type
DFPI–
Double-acting pneumatic drive for process auto-
mation with integrated displacement encoder
Size of valve actuator
100–, 125– , 160–,
200–, 250–, 320–
Piston diameter can be selected in steps, spe-
cifications in [mm]
Stroke
...–
Stroke length freely selectable in the range from
40 to 990;
(40 ... 990)
Specifications in [mm]
Cushioning
N
No cushioning
Displacement encoder
D2
Analogue displacement encoder
Method of measurement
P–
Potentiometer
Regulation
C1
Controller 1
Directional control valve
V–
Integrated
Connection type
Not specified
Unprotected pneumatic connections
P
Protected pneumatic connections
Feedback signal
A
Analogue feedback signal, actual value
Safety position
Not specified
Piston rod advancing
Fig. 2
Type code (e.g. DFPI-100-200-ND2P-C1V-P-A)
The following characteristics of the linear drive are dependent on the piston
diameter, and may differ from the representation in Fig. 1:
– Position of the earth terminal (
identification on product)
– Shape of the cylinder barrel
– Shape of the flange receptacle.
In addition, for linear drives with a piston diameter ≥ 200 mm the compressed air
supplied from one side is fed via an unprotected line parallel to the cylinder barrel.
Tie rod screws are used to mount the cylinder end cap. For linear drives with a
piston diameter ≤ 200 mm the compressed air is fed internally. The cylinder end
caps are screwed to the housing.
3
Function
The compressed air applied at connection P
is directed by the integrated valve manifold
alternately to the two piston chambers of
the cylinder – depending on the setpoint po-
sition that is specified. This causes the pis-
ton rod connected to the piston to move
backwards and forwards.
Fig. 3
The maximum possible venting of the two cylinder chambers can be set independ-
ently of each other using flow control screws D2 and D4. D2 controls the venting
flow when the piston rod advances. D4 controls the venting flow when the piston
rod retracts. This can be used to influence the maximum travel speed of the linear
drive in the range from 0 ... 100 %. In the factory setting, the flow control screws
are completely open. In the DFPI-...-...-ND2P-C1V-A they are protected against
contamination by rubber plugs, and in the DFPI-...-...-ND2P-C1V-P-A by the flange
receptacle.
Positions are specified via an analogue setpoint signal (4 … 20 mA), for example
via a master PLC/IPC or manually on-site via an external setpoint generator. Posi-
tioning of the piston rod/slide gate is by means of closed-loop control.
The integrated positioner performs position control of the piston rod within the
available stroke range.
The integrated displacement encoder transmits the current position to the internal
positioner as an analogue signal. The positioner cyclically compares the setpoint
and actual positions and transmits appropriate positioning signals to the integ-
rated valve manifold for positioning control.
Document Outline
- Linear drive DFPI-...-...-ND2P-C1V-...-A English