9 safety aspects – Festo Электроцилиндр User Manual
Page 26
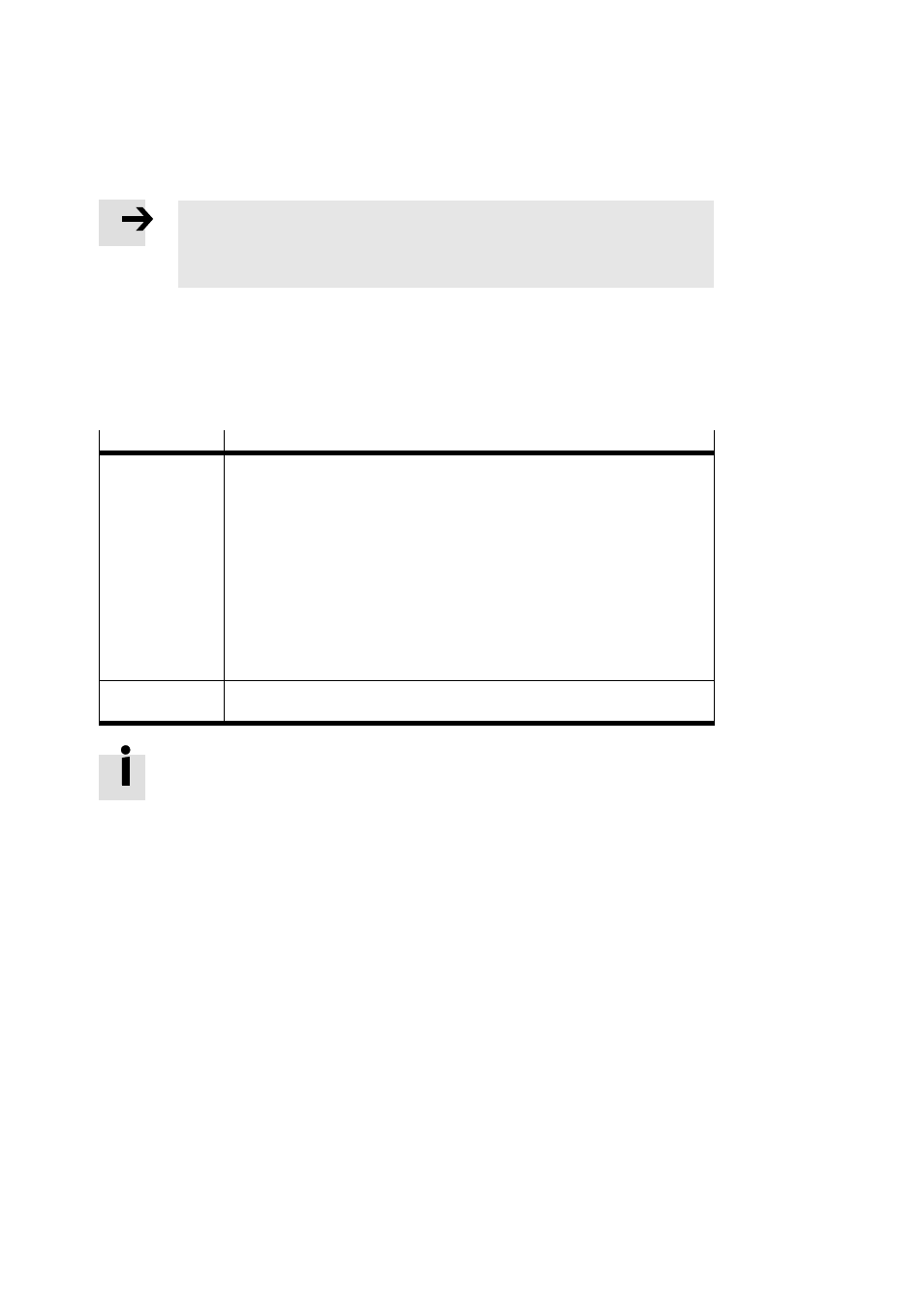
2
Overview
26
Festo – GDCP-CMMO-ST-EA-SY-EN – 1301a – English
2.9
Safety aspects
Note
Check within the framework of your EMERGENCY STOP procedures to ascertain the
measures that are necessary for switching your machine/system into a safe state in the
event of an EMERGENCY STOP.
•
If an EMERGENCY STOP circuit is necessary for your application, use additional, separate safety
limit switches (e.g. as normally closed limit switches wired in series).
•
Use hardware limit switches or, if required, mechanical safety limit switches and fixed stops or
shock absorbers as appropriate in order to make sure that the axis always lies within the permitted
positioning range.
•
Note the following points:
Action
Behaviour
Cancellation of
the ENABLE signal
on the I/O
interface
–
Without brake/clamping unit:
The drive brakes with the quick stop ramp (Quick stop). The controller
output stage is then switched off. The effective load could possibly slide
down if mounted in a vertical/inclined position.
–
When using a brake/clamping unit:
If the drive moves when ENABLE is cancelled, then it will initially be brought
to rest using Quick Stop deceleration. As soon as the drive has come to a
standstill, the brake output is reset: the brake/clamping unit closes.
Simultaneously, the switch-off delay time begins to run. The CMMO-ST still
controls the position. The controller end stage is switched off after the
switch-off delay.
Switching off the
load voltage
The load voltage is switched off. The effective load on the drive may continue to
move due to inertia, or it will fall if mounted in a vertical or sloping position.
For STO function:
separate document GDCP-CMMO-ST-STO-…