Normal data transfer – ProSoft Technology MVI56E-GSC/ GSCXT User Manual
Page 88
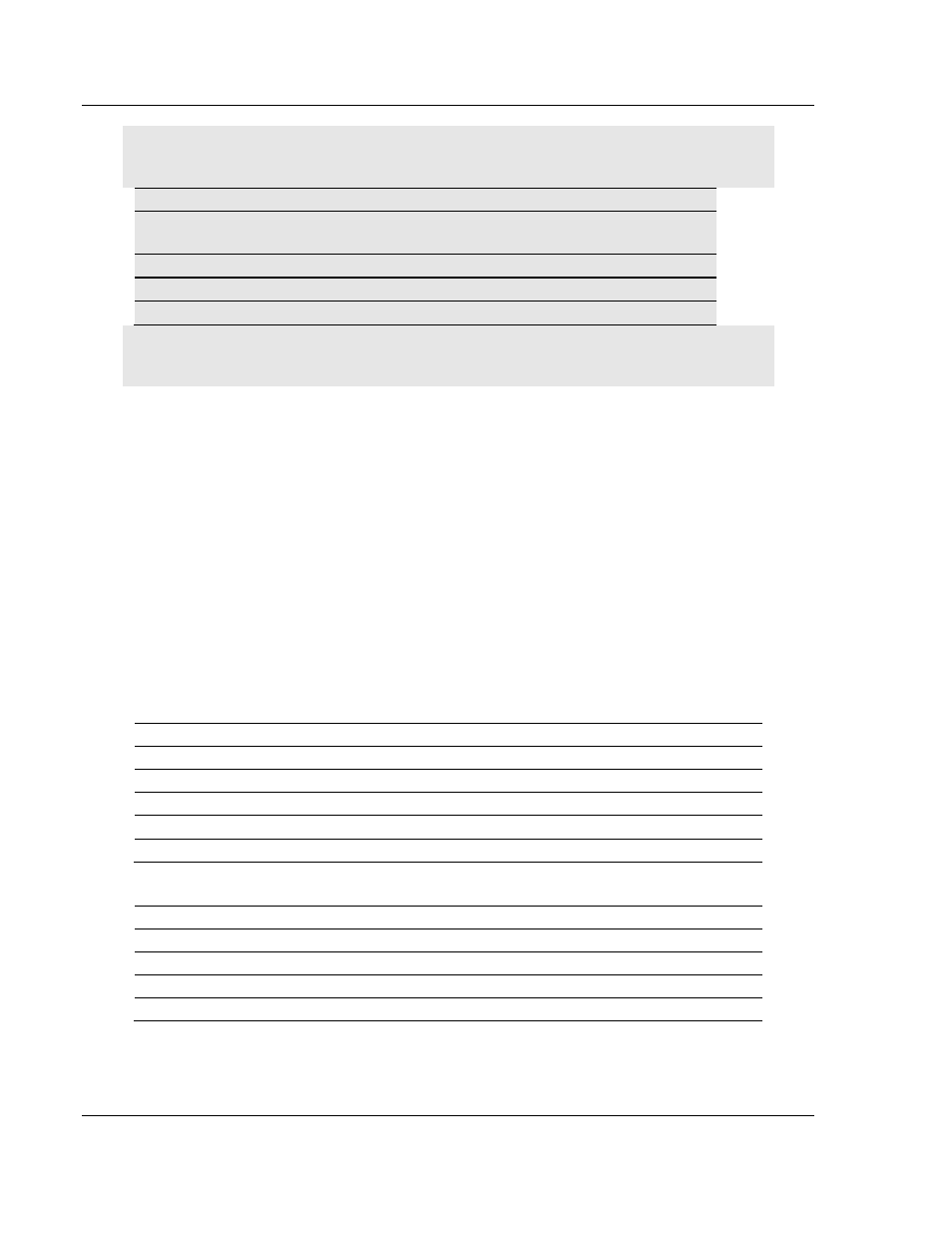
Reference
MVI56E-GSC ♦ CompactLogix or MicroLogix Platform
User Manual
Enhanced Generic ASCII Serial Communication Module
Page 88 of 140
ProSoft Technology, Inc.
May 9, 2014
Note: For each termination type, you must also enter values in the following parameter
configuration tags:
For Termination Type
Receive Parameters to Set
Terminating Characters GSC.PortX.RTermCnt
GSC.PortX.RTermChar
Message Timeout
GSC.PortX.RTimeout
Intercharacter Delay
GSC.PortX.RDelay
Packet (String) Length
GSC.PortX.RPacketLen
Streaming mode is not recommended for general use, as it creates heavy demands on the Control
Logix processor and requires time-critical programming logic to properly process.
4.3
Normal Data Transfer
Normal data transfer includes the transferring of data received or to be
transmitted on the ports and the status data. These data are transferred through
read (input image) and write (output image) blocks. Refer to Sample Logic
Program for a description of the data objects used with the blocks and the ladder
logic required. The following topics describe the function and structure of each
block.
4.3.1 Block Request from the Processor to the Module
These blocks of data transfer information from the ControlLogix processor to the
module. The structure of the output image used to transfer this data is shown
below:
Port 1
Byte Offset
Description
0
Block Sequence Number (Read Block Byte 499 value sent by module)
1 to 2
Intercharacter delay for this message (milliseconds between characters)
3 to 4
Number of characters to transmit on Port 1 (0 to 200)
5 to 204
Port 1 data to transmit
205 to 250
Reserved
Port 2
Byte Offset
Description
251 to 252
Intercharacter delay for this message (milliseconds between characters)
253 to 254
Number of characters to transmit on Port 2 (0 to 200)
255 to 454
Port 2 data to transmit
455 to 495
Reserved
To set up a message to be transmitted, the simple example ladder expects the
user to do the following in this order, either manually or by writing additional
process logic: