1 sloping current, 2 degree procedure, 3 tube o.d – MK Products Advanced Color Logic Rev.C User Manual
Page 15: 4 wall thickness, 5 tacks, 6 levels, 7 travel speed
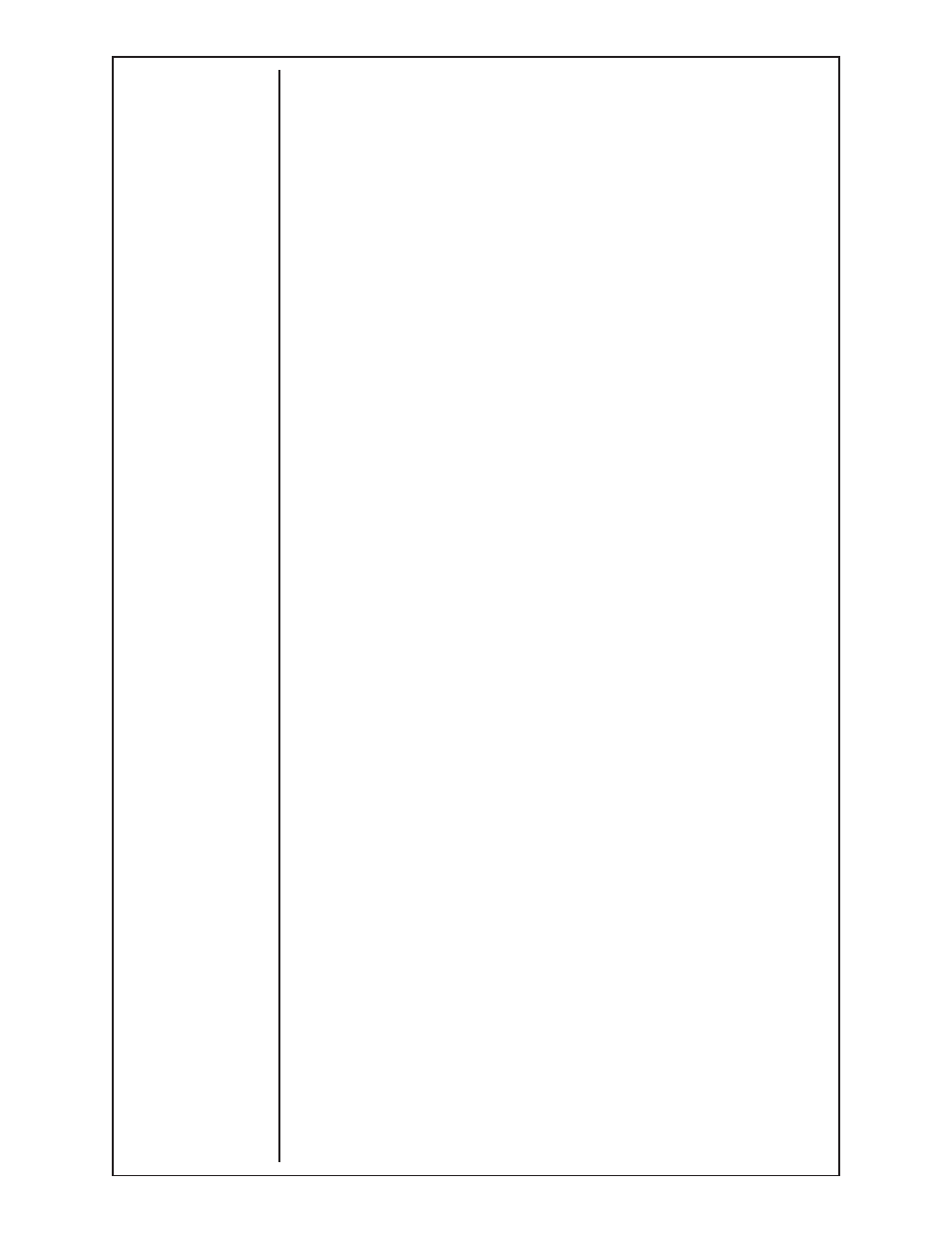
Advanced Color Logic Owner’s Manual - Page 10
2.6.2 Degree Procedure
A degree procedure is one based on a circumference of degrees and not
inches or millimeters. Each level is exactly a certain number of degrees
and not a certain number of seconds. Similarly, each level is programmed
to end at a set degree and not when time runs out.
If a degree procedure is chosen, certain conventions must be
remembered when modifying and developing; such as motor speed scaling
versus rotational travel and level jumping versus level termination (see
MODIFYING WELD PROCEDURES).
Declining a degree procedure will default the APG to make a standard time
based procedure.
The next screen is the Auto-Procedure Generation Information screen. It
is at this screen that all pertinent variables are inputted and used for weld
procedure generation. In order, from top to bottom they are, Tube O.D. (up
to 5.5”), Wall Thickness (up to 0.200”), Number of Tacks (up to 8), Number
of Levels (up to 90), and Travel Speed (ipm - maximum based on tube
diameter).
2.6.3 Tube O.D.
This maximum is based on the largest sized weldhead available. The ACL
unit does not need to know the size of the weldhead it welds uses; it uses
a correlation between tube diameter and travel speed (ipm) to calculate a
rotational speed (rpm) of the tungsten.
2.6.4 Wall Thickness
The maximum output of the ACL Welding Power Supply is 200 amps; the
ACL is programmed to give one-amp for every one-thousands material
thickness. For these reasons, the maximum wall thickness input possible
is two hundred thousands.
2.6.5 Tacks
When this option is utilized, the ACL program will generate a current value
and a length of time for each tack, which is in relation to the tube diameter
and wall thickness. For thicker materials, longer and hotter tacks while
thinner materials get a shorter and colder tack.
All tacks programmed from this auto tacking function, will occur at
opposing intervals around the tube. These tacks are not programmed
into the procedure as levels, but exist as opposing intervals of degrees,
occurring after the Pre-Purge and prior to initial arc strike.
2.6.6 Levels
Whether designing a regular procedure or a degree procedure, the
circumference of the tube will be evenly cut into slices that correlate to the
number of levels chosen, excluding the Up Slope and Final Slope levels.
2.6.7 Travel Speed
This is the only screen in which you will see the travel speed with a value
of inches-per-minute (ipm). All other travel speed values in this program use
rpm. The travel speed in rpm is derived by dividing the travel speed in ipm,
by the circumference (which is calculated from the tube diameter).
When all the values for the weld procedure have been entered, the program
will return to the MAIN MENU. Options [1 Weld With Procedure *TRIAL*]
and [5 Modify Procedure *TRIAL*] will contain the name ‘*TRIAL*’ where
the once empty blanks were.
Since this procedure has just been made, the program gives it the name
*TRIAL*. At this point the operator may choose to save this procedure
with a valid name, using option [6 Save Modified Procedure], or continue
with modification, editing, testing and/or welding and save at a later time
in the program.
Section B
(Cont.)