Motor calibration data – MK Products Copperhead Weldhead User Manual
Page 16
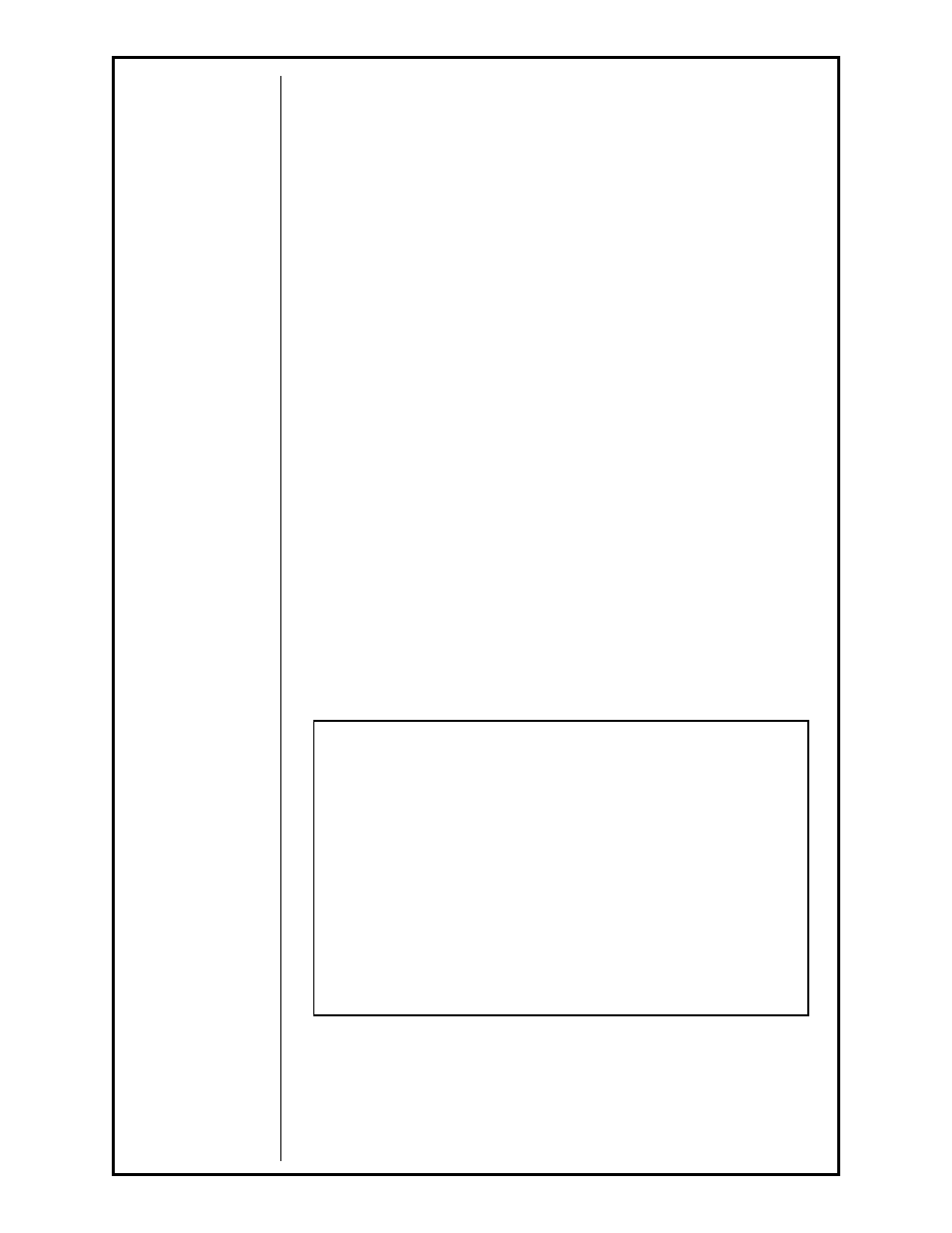
CopperHead
®
Owner’s
Manual - Page
8
two different speeds to get two times at high speed and two times at low
speed. This raw data is displayed under the column “Measured”. The two
readings per speed are averaged together to produce an average time. This
is displayed under the column “Actual”. The expected values are under the
column “Cal”. The corresponding speeds derived by the above-mentioned
method are displayed under the column “Actual” for the test results and
under the column “Cal” for the expected results.
column “Measured”. The two readings per speed are averaged together to
produce an average time. This is displayed under the column “Actual”. The
expected values are under the column “Cal”. The corresponding speeds
derived by the above-mentioned method are displayed under the column
“Actual” for the test results and under the column “Cal” for the expected
results.
Using this information the ACL
®
calculates the two sets of error parameters:
Gain and Zero. The Gain parameter is a measure of the multiplying factor
error on the speed. The Zero parameter is the error of the speed where it
should be going at zero rpm but in actually it is slightly non-zero. The ACL
®
then calculates the adjustment coefficients based upon these error param-
eters to properly adjust the motor speed commands in order to give the cor-
rect weldhead rotor speed.
The second set of parameters is the “Tach” error. The motor speed is
directly read by the ACL
®
, using the tachometer feedback from the weldhead
motor, in two ways: 1) the analog tachometer signal is used by the analog
closed loop motor servo to control to the commands provided from the ACL
®
control system. 2) The analog tachometer signal is converted to a digital
signal, using an analog multiplex analog to digital converter technique, and
then Interpreted by the digital ACL
®
control system. It compares on what
it has calculated from its timing data versus what the tachometer is giving
corrected by the same coefficients mentioned above. Similarly, a gain error,
“Gain”, and an off-set error, “Zero”, are derived. Reference the Sample ACL
®
Calibration Printout in Table 1.
Motor Calibration Data
08/07/01 15:45:04 / 08/07/01 15:45:04
Gain Error = 3.5% / Zero error = 0.05 RPM
Cal
RPM
Actual
RPM
Cal
Sec
Actual
Sec
Measured
Update
Sec
Sec
Sec
6.00
5.84
10.00
10.27
10.27
10.26
0.00
2.00
1.98
30.00
30.36
30.60
30.05
Tachometer: Gain error= -4.1% / Zero error = 0.13 RPM
Actual
RPM
Read
RPM
Measured
Update
Sec
RPM
RPM
5.84
5.96
5.96
5.96
0.00
1.98
1.93
1.91
1.94
Sample ACL
®
Calibration Printout
Table 1