MK Products Copperhead Weldhead User Manual
Page 13
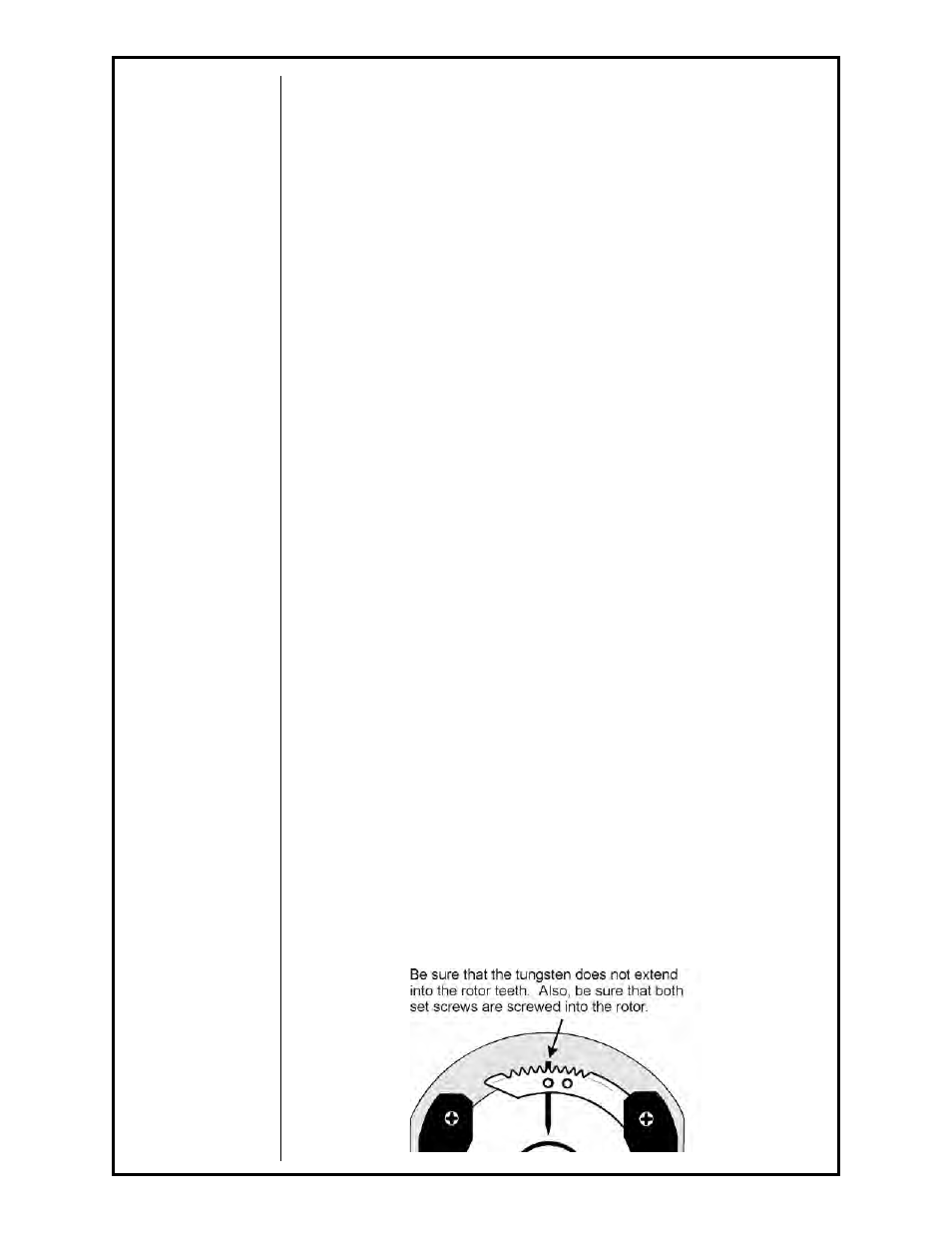
CopperHead
®
Owner’s
Manual - Page
5
3/32” hole is used for tungsten tooling (holders and extenders) however, a
tungsten electrode can also be used.
To insert the electrode, jog the rotor around until the setscrew is exposed
(approximately at the twelve-o’clock position), and loosen the setscrew.
Insert a properly prepared electrode from the top of the rotor and tighten the
setscrew. Be sure to set the appropriate arc gap prior to welding.
Recommended Arc Gap
The proper arc gap is an important part of the proper use of your orbital
welding equipment. Improper arc gap can cause arc strikes to occur to your
Collets or to the Side Plate Clamp.
Be sure the arc gap is as short as possible, consistent with the process and
weld current level, but not so short as to ‘crash’ or touch the weld being
made.
If no arc gap is known when designing a weld procedure a good rule-of-
thumb is as follows:
For on-site field welding applications; match the arc gap to the wall
thickness of the tube/fitting being welded, with a maximum arc gap
of .090”. For example, if the tube wall thickness is .035”, then start
with an arc gap of .035”.
For in-house manufacturing; add 1/2 the wall thickness plus .010”, with
a maximum arc gap of .070”.
Setting the Arc Gap
1. Place the part to be welded on the lower Collets with the clamps in the
upright open position.
2. Jog the rotor until the tungsten hole in the rotor is sitting directly over
the part with access to the tungsten set screw, approximately at twelve-
o’clock.
3. Prepare the tungsten electrode with the right length and shape as
explained in the Tungsten Geometry and Tungsten Preparation sections.
4. Put the tungsten electrode through the appropriate hole on the top of the
rotor.
5. Place the appropriate thickness gauge between the tungsten electrode
and the part to be welded so that the tungsten electrode is at the correct
gap.
Be certain the thickness gauge is perpendicular to the tungsten
electrode.
6. Tighten the setscrew to secure the tungsten electrode in the rotor.
CAUTION
Do not over-tighten the tungsten set screw. Over-tightening the setscrew
can crack and splinter the tungsten causing errant starts and arc wander.
Figure 5