MK Products Copperhead Weldhead User Manual
Page 14
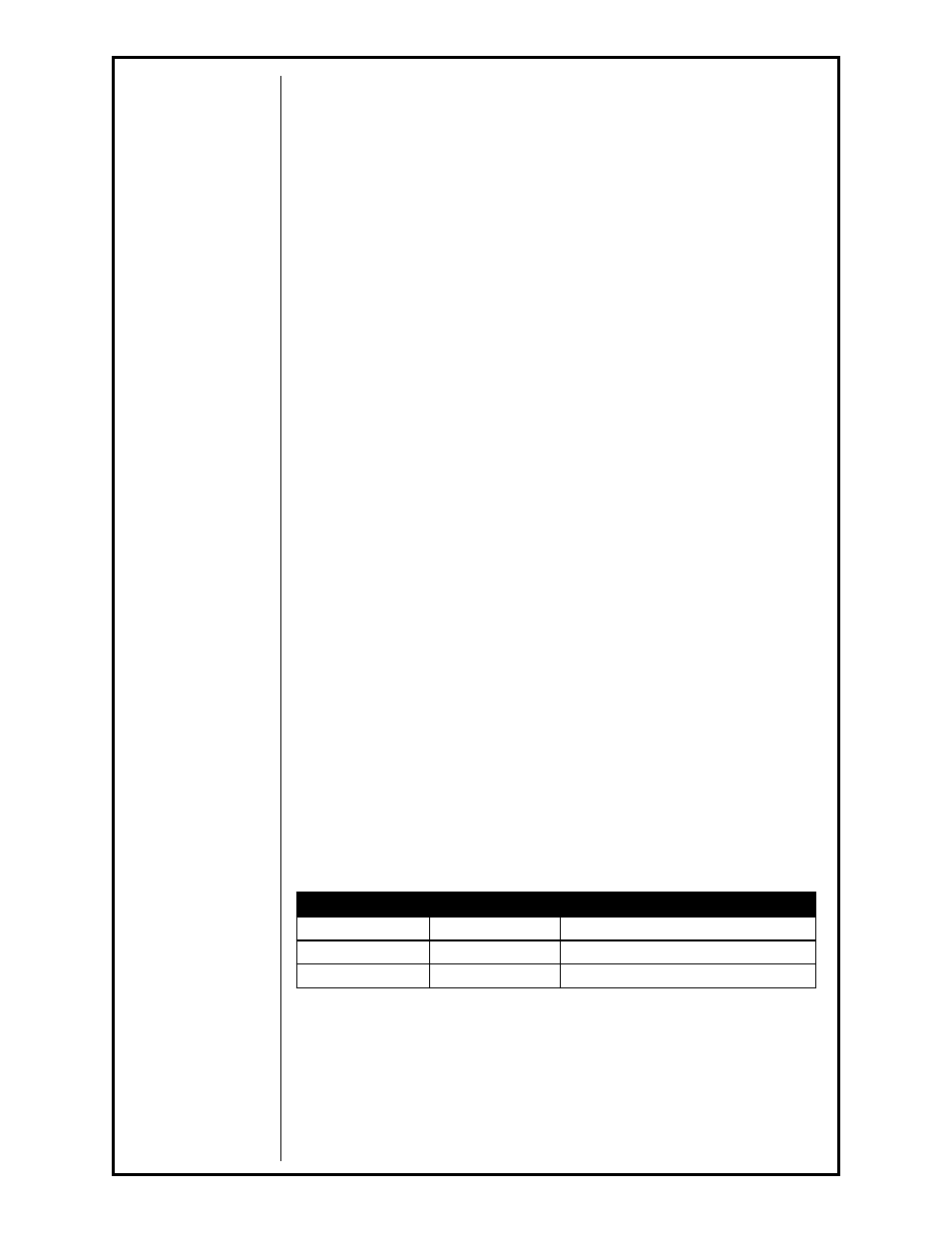
CopperHead
®
Owner’s
Manual - Page
6
Be sure that the tungsten does not extend into the rotor teeth and that both
setscrews are flush with the rotors surface (see Figure 5).
Any length of tungsten that is protruding out the back of the rotor will jam
with the meshing gears inside the weldhead. This will push the tungsten into
the weld being made and inevitably cause an ARC FAULT.
If the weldhead becomes jammed, a “Motor Stall” will result. Usually, some
foreign matter, or a piece of tungsten electrode has fallen within the gear
mechanism of the weldhead, hindering the rotation of the gears.
Clearing a Jammed Weldhead
In order to clear the jam, turn the weldhead upside-down and vigorously
shake the weldhead. If this fails to clear the foreign matter; while still
inverted, briefly push the red “Reverse” button located in the bottom of the
handle.
Before turning the weldhead right side up, attempt to locate the foreign
object. If the jam cannot be cleared in this manner, the weldhead must be
disassembled and the objects removed.
See WELDHEAD DISASSEMBLY in the Maintenance section for detailed
information on dismantling the CopperHead
®
Extenders
The Extenders are designed to fit in the large tungsten hole in the rotor.
They have a 3/32” diameter hole, with an accompanying setscrew in the end
to allow for the tungsten holder.
Holders
Once the holder is locked into the extender, the holders are designed to
hold the tungsten electrode at a place that is somewhere outside the normal
confines of the weldhead. There are three angles at which the tungsten can
be set in the holder: 20° and 30° from vertical, or a single angle setting of 90°
from horizontal.
Both the extender and the holder are made in different lengths, depending
on tube diameter and joint offset. In some cases, special Collets are also
needed when having to use this type of tungsten tooling. Contact the factory
for Specialty Tooling.
Tungsten Tooling
As mentioned above, the larger of two tungsten holes is primarily used for
tungsten tooling: Holders and Extenders. The extender is a tool for the
holder; without it, the holder has nothing to fit into. These two must be used
together.
Gas Flow Rates
Weldhead Model Gas Flow Rates Minimum Pre & Post Purge Times
5001
15-20 CFH
10 Seconds
5002
20-25 CFH
20 Seconds
5003
25-30 CFH
30 Seconds
Recommended arc gas flow rate is the same for the ACL
®
and the
CobraTig
®
. Flow rates higher than 35 CFH can create turbulence within the
weldhead chamber and blow the arc about.
Back-up gas flow rates are typically between 5 and 20 CFH, depending
on internal volume and component configuration. Typically, when welding
components with relatively large internal volumes, a separate source for
backup purge gas is recommended.