Hypertherm PHC Sensor User Manual
Page 50
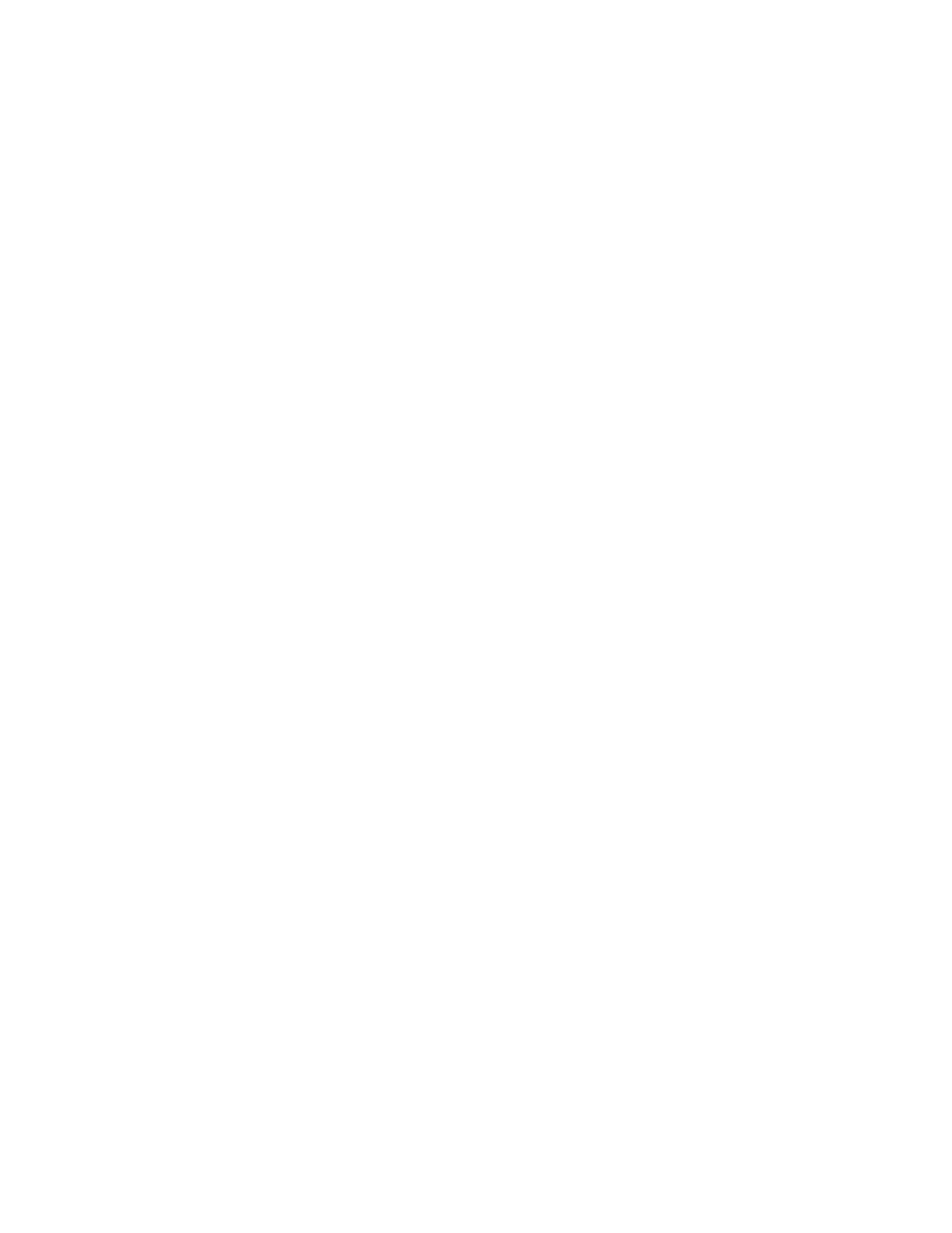
50
Sensor™ PHC Operation and Setup Guide
• A coolant leak on a liquid cooled torch.
Solution: This error is reset on the next CYCLE_START.
E.03 Lifter Timeout Error
Reason: Lifter motion was commanded but the lifter destination was not sensed within the timeout period.
Possible causes:
• A mechanical problem in the lifter such as the motor coupling to the lifter mechanics has loosened.
• The torch lead set is binding and limiting the lifter motion.
• A problem with the motor wiring, motor drive, or with the motor itself.
Solution: The error is reset on the next CYCLE_START.
E.04 Limit Reached during Auto Operation
Reason: The lifter reaches a travel limit during arc voltage controlled operation.
Possible causes:
• The lifter does not have the range of travel to accommodate the thickness of the material being cut.
• Improper operation of either the limit switches or the limit switch wiring.
Solution: Adjust the lifter or torch mounting to make more effective use of the lifter travel range.
This error is reset on the next CYCLE_START.
E.05 IHS SYNC Timeout
Reason: The torch reaches the IHS pierce position and is waiting for the IHS_SYNC input from the CNC to be
released.
Solution: Check the wiring of the IHS_SYNC input and the CNC programming for this signal. This error is
reset on the next CYCLE_START.
The HIS_SYNC signal is usually only used for multiple torch installations.
E.06 Transfer Timeout Error
Reason: The Plasma torch was fired but that the TRANSFER signal was not received within 5 seconds
Possible causes:
• A faulty IHS sequence that resulted in an improperly high pierce height.
• Failure to transfer due to bad consumables.
• Improper plasma gas settings.
• Bad work piece grounding.
• The TRANSFER signal on the power supply interface is missing or improperly connected to the PHC
Plasma Interface
Solution: The next CYCLE_START resets this error.
E.07 Lost Plasma Arc Error
Reason: The plasma torch lost transfer during operation before CYCLE_START was removed
Possible causes:
• Cutting off the edge of the plate.
• Bad
consumables.
• Improper height control settings.
Solution: The next CYCLE_START resets this error.
E.08 Torch Breakaway Error
Reason: The torch breakaway has tripped.
Possible causes:
• The torch crashed into the work piece because of tip-ups or improper height control setup.
Solution: If a torch breakaway is not installed, turn the setup DIP switch #15 on the PHC to OFF (down) to
ignore this input.
If a torch breakaway is installed, see Torch breakaway error on page 53 for a troubleshooting procedure.