11 lifetime limits, 12 proof testing, 13 maintenance – Flowserve 3200MD User Manual
Page 32: 14 repair and replacement, 15 training requirements
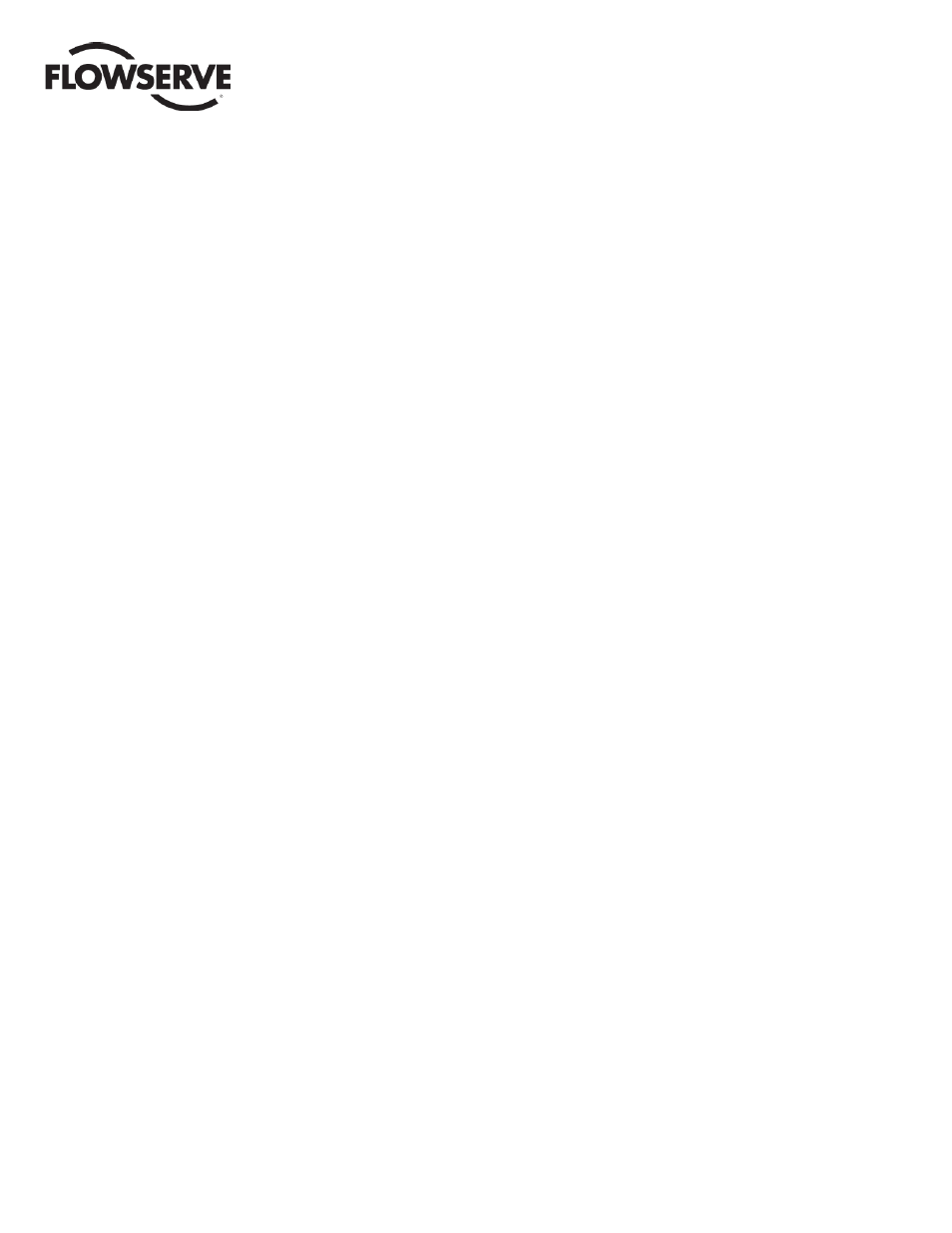
User Instructions - Digital Positioner 3200MD LGENIM0059-09 12/13
32
10.11 Lifetime Limits
The expected lifetime of the Flowserve 3200MD Positioner is ap-
proximately 10 years. The reliability data listed the FMEDA report is
only valid for this period. The failure rates of the Flowserve 3200MD
Valve Positioner may increase sometime after this period. Reli-
ability calculations based on the data listed in the FMEDA report for
lifetimes beyond 10 years may yield results that are too optimistic,
i.e. the calculated Safety Integrity Level may not be achieved.
10.12 Proof Testing
The objective of proof testing when used in low demand mode
of operation is to detect failures within Flowserve 3200MD Valve
Positioner and its associated sensors and actuators that may not be
detected by the normal self diagnostics. Of main concern are unde-
tected failures that prevent the safety instrumented function from
performing its intended function.
The frequency of the proof tests (or the proof test interval) is to be
determined in the reliability calculations for the safety instrumented
functions for which the Flowserve 3200MD Valve Positioner is ap-
plied. The actual proof tests must be performed at least as frequently
as specifi ed in the calculation in order to maintain required safety
integrity of the safety instrumented function.
The following tests need to be specifi cally executed when a proof
test is performed. The results of the proof test need to be docu-
mented and this documentation should be part of a plant safety
management system. Positioner failures that are detected should be
reported to Flowserve.
To perform the proof testing, a HART communicator such as a 375
Handheld or software such as ValveSight DTM for Logix 3200MD
are required.
Steps for Proof Test
Step Action
1. Bypass the safety PLC or take other appropriate action to avoid
a false trip.
2. Set the analog input command to less than 2.0 mA.
3. Ensure that the attached valve is fully in the safe state (defi ned
by application) and has moved to that position within the
allowed time. This tests for all failures that could prevent the
closure of the valve, including electronic and mechanical faults,
as well as valve faults.
4. Inspect the 3200MD Valve Positioner for any visible damage
or contamination and ensure the follower arm has suffi cient
spring bias.
5. Remove the bypass from the safety PLC or otherwise restore
normal operation
When the tests listed above are executed a proof test coverage of
95% can be claimed.
10.13 Maintenance
Calibrations should be checked annually.
10.14 Repair and Replacement
In the unlikely event that the Flowserve 3200MD Valve Positioner
fails, the failure should be reported to Flowserve. Replace faulty
components according to section 8 of this manual or return the
positioner to Flowserve for service.
10.15 Training Requirements
Activities specifi ed in this manual shall be performed by a service
technician trained in the installation and maintenance of process
instrumentation.