5 tools required, 6 fastener torques, 7 renewal clearances – Flowserve LNGT User Manual
Page 31: 8 disassembly
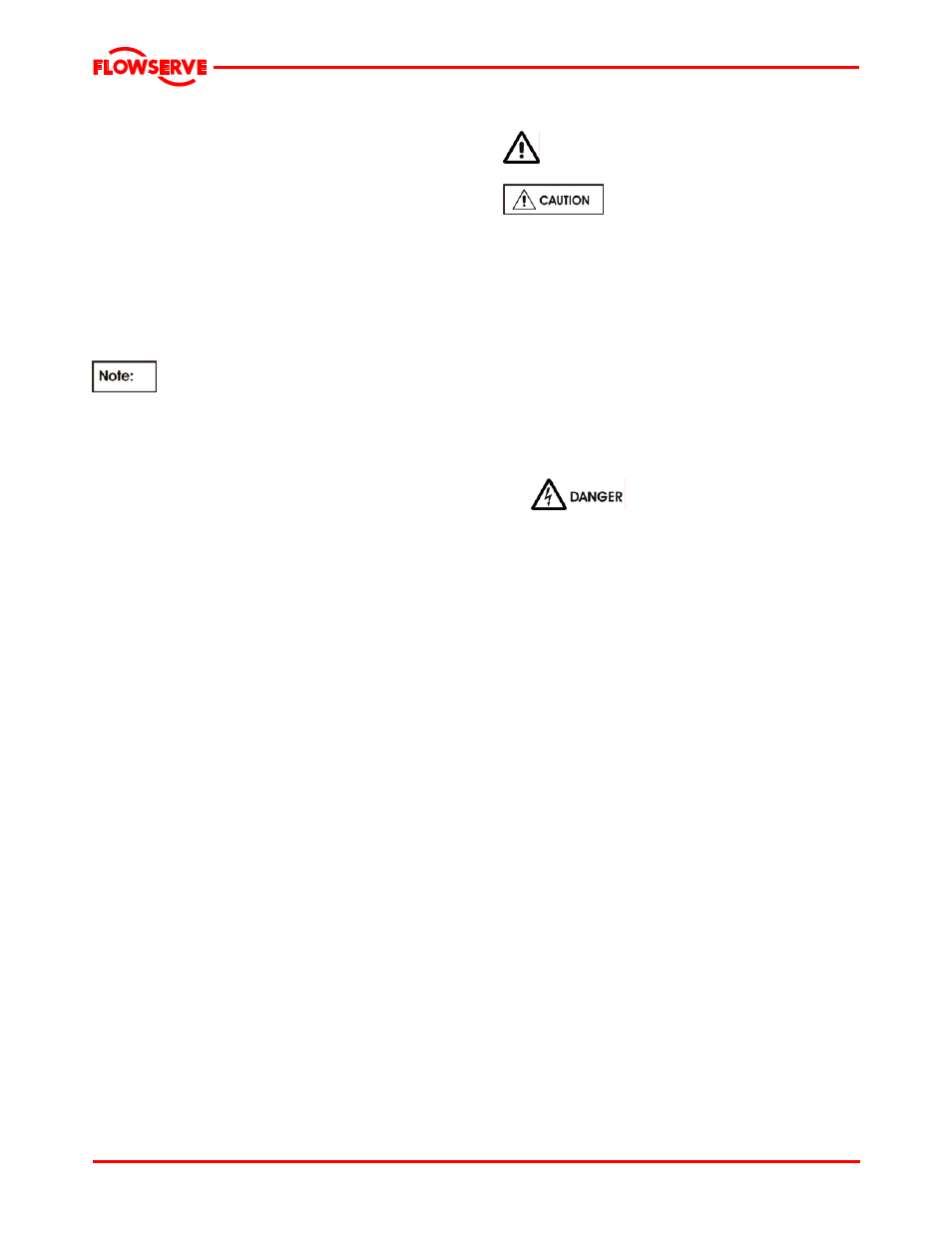
LNGT USER INSTRUCTIONS ENGLISH 00083107 02-08
Page 31 of 48
®
For 4 years operation:
1 - set of bearings [journal and thrust]
2 - sets of gland packing [if applicable]
2 – lantern rings [if applicable]
2 - basic mechanical seal [if applicable]
2 – set of shaft sleeves
2 - set of gaskets and O-rings
1 – impeller
2 - set of casing wear rings
2 – set of impeller wear rings [if applicable]
2 - set of bearing isolators
2 – set of throath bushes
Please refer to this manual for spares of
applicable buy outs.
6.5 Tools required
A typical range of tools that will be required to
maintain these pumps is listed below.
Readily available in standard tool kits, and
dependent on pump size:
• Open ended spanners [wrenches] to suit up to
M 48 screws/nuts
• Socket spanners [wrenches], up to M 48
screws
• Allen keys, up to 10 mm [A/F]
• Range of screwdrivers
• Soft
mallet
More specialized equipment:
• Bearing
pullers
• Bearing induction heater
• Dial test indicator
• C-spanner [wrench] - for removing shaft nut.
[If difficulties in sourcing are encountered,
consult Flowserve.]
6.6 Fastener torques
See applicable section in the Manual for Fastener
torques. Also read the Supplementary User
Instructions.
6.7 Renewal clearances
As wear takes place between the impeller and casing
ring the overall efficiency of the pump set will
decrease. To maintain optimum efficiency it is
recommended that rings are replaced and the
impeller renovated when the radial clearance detailed
in section 3.4.2 has doubled to 0.6 to 0.8 mm [0.024
to 0.032 in.], depending on pump size.
6.8 Disassembly
Refer to section 1.6, Safety, before
dismantling the pump.
Before dismantling the pump for
overhaul, ensure genuine Flowserve replacement
parts are available.
Refer to sectional drawings for part numbers and
identification.
The pump unit can be disassembled without using
any special or auxiliary tools.
Besides the instructions below, refer to the
sectional drawing of the pump unit
The following activities should be carried out prior
to disassembly of the pump:
Stop the pump. Please refer to
the procedure for stopping the pump..
Secure the pump unit; make sure that the
electric motor cannot start up unexpectedly
while maintenance work is being carried out.
Disconnect the electric motor from the mains in
accordance with the instructions provided by
the relevant supplier. Attach a warning sign to
the switch box.
Drain off the fluid in the pump unit. To do this,
remove the plug [6569] underneath the pump
casing or use the device in the drain pipe.
Collect the fluid in a drip tray. If hazardous
fluids are being pumped, use personal
protection equipment and dispose of the
drained-off fluid in an environment-friendly
manner.
Flush the pump thoroughly, so that no
dangerous fluids remain inside. Dispose of the
drained flushing fluid using an environment-
friendly method. If the pump was flushed by a
third party, make sure that it has been released
for disassembly.
Fit the plug [6569] into the pump casing or
close the device in the drain pipe.
Mark all components to be absolutely sure of
their correct position during assembly.
Disconnect any auxiliary piping, e.g. for the
cooling, sealing and flushing fluids of the
mechanical seal.
Disassemble the protective cover local to the
coupling.
Disassemble, if present, the coupling spacer
between the pump unit and electric motor in