6 piping – Flowserve APKD User Manual
Page 25
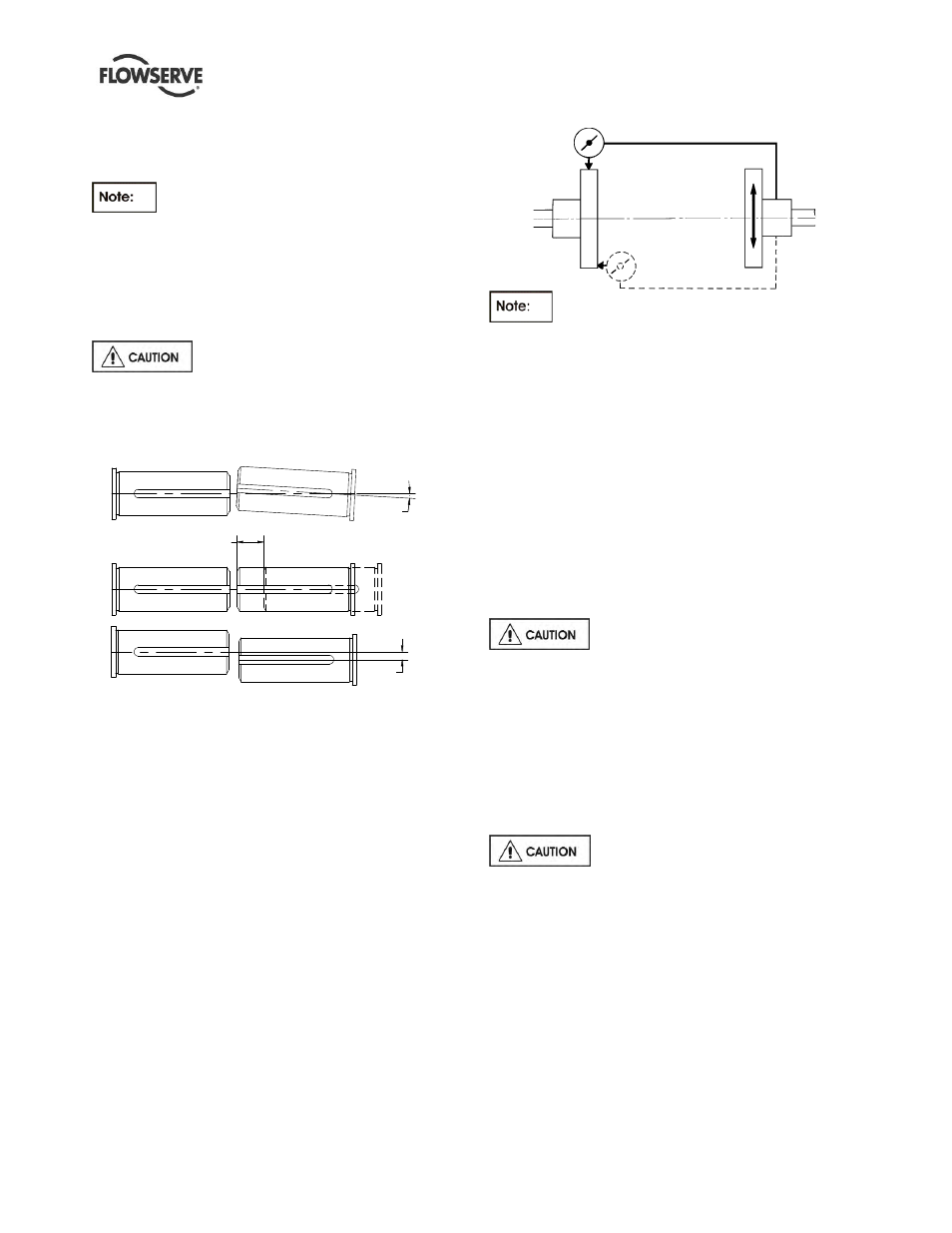
APKD DOUBLE-CASE, DOUBLE-SUCTION USER INSTRUCTIONS 26999903 07-13
Page 25 of 55
flowserve.com
See section 5.3.2.1 for final coupling alignment for
solid shaft.
Before bumping motor make sure that the
coupling halves are not touching and that the driver
can rotate freely without rotating the pump. Driver
half coupling must be in proper position so the
circular key will not come out.
4.5.4
Angular and parallel misalignment
Check the direction of pump rotation
before the coupling is fully connected. The power
supply to the driver to be connected only after the
final alignment is complete.
Figure 4.9
Parallel offset
Angular offset
Axial offset
a)
b)
c)
a) Angular Offset: The median lines of shaft
intersect halfway between the ends of the two
shafts.
b) Axial Offset: Another offset is the displacement
of one or both of the shafts. A typical example is
thermal expansion.
c) Parallel Offset: The median lines run parallel.
The maximum allowable parallel offset depends
on the size of coupling and is indicated in the
instruction manual of manufacturer of coupling.
For couplings with narrow flanges use a dial indicator
as shown in the detail to check both parallel and
angular alignment.
Figure 4.10
Parallel
Angular
a) Pumps with thick flanged non-spacer couplings
can be aligned by using a straight-edge across
the outside diameters of the coupling hubs and
measuring the gap between the machined faces
using feeler gauges, measuring wedge or
calipers.
b) When the electric motor has sleeve bearings, it is
necessary to ensure that the motor is aligned to
run on its magnetic centerline.
Refer to the motor User Instructions for details.
A button (screwed into one of the shaft ends) is
normally fitted between the motor and pump shaft
ends to fix the axial position.
If the motor does not run in its
magnetic center the resultant additional axial force
may overload the pump thrust bearing.
If the pump is handling hot liquid, the alignment must
be rechecked in warm condition of the unit. The
alignment of the unit shall be checked again after 200
service hours.
4.6 Piping
Protective covers are fitted to the pipe
connections to prevent foreign particles or objects
entering the pump during transportation and
installation. Ensure that these covers are removed
from the pump before connecting pipes.
4.6.1 Pipe
work
velocities
In order to minimize friction losses and hydraulic
noise in the pipe work it is good practice to choose
pipe work that is one or two sizes larger than the
pump suction and discharge.
Typically, main pipe velocities should not exceed 2
m/s (6 ft/sec) on the suction and 3 m/s (9 ft/sec) on
discharge.