5 power supply, Ower supply – Bronkhorst FLOW-BUS interface User Manual
Page 17
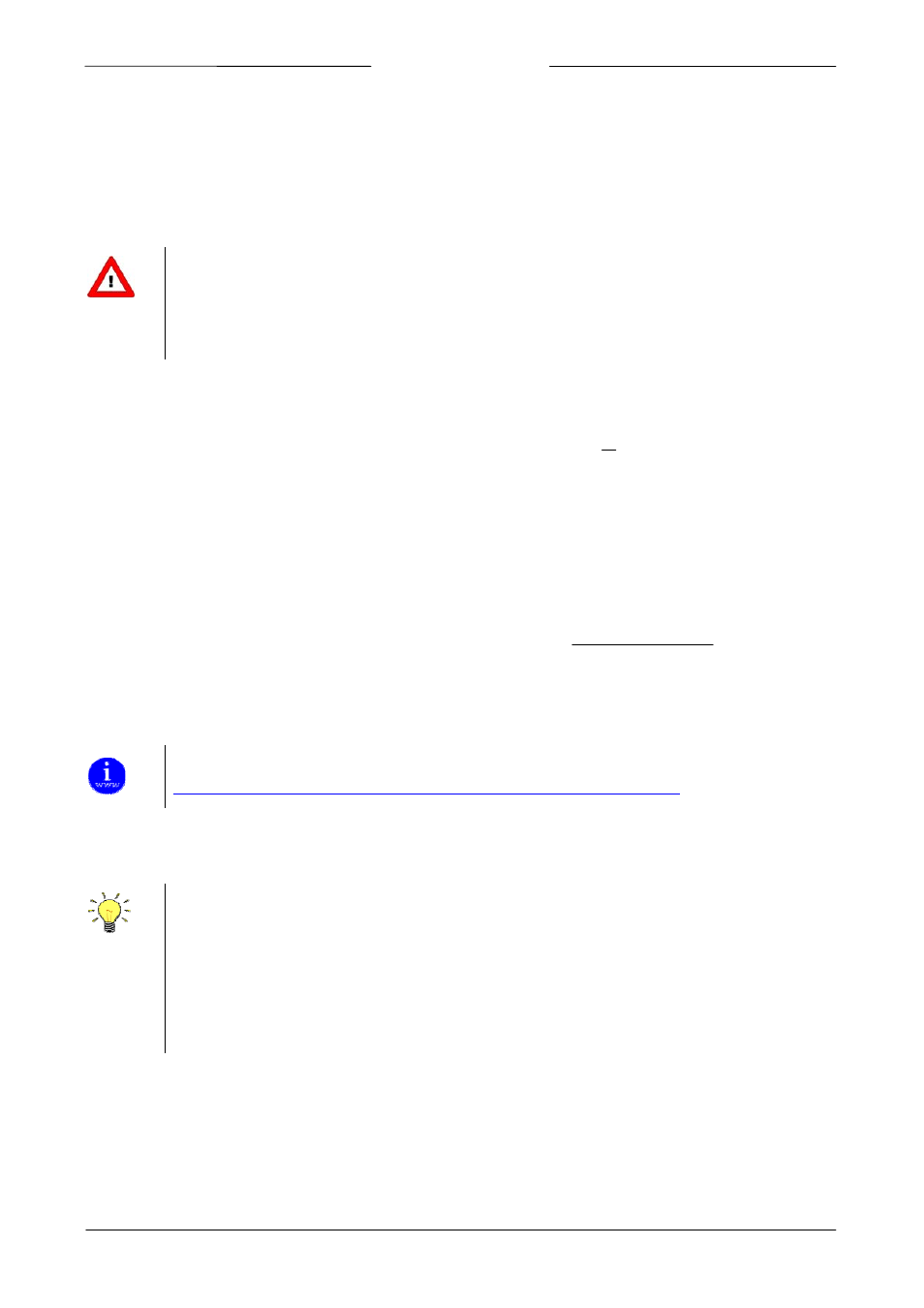
BRONKHORST
®
2.5 P
OWER SUPPLY
Bronkhorst uses FLOW‐BUS cables with extra wires inside for +15…24Vdc and 0Vdc in order to handle power supply
and communication within the same cable. Because RS485‐cabling needs a daisy‐chain connection and power‐lines
prefer a star‐point connection, we came to a compromise of both in the FLOW‐BUS cabling. Bronkhorst can advise you
how to power your FLOW‐BUS system. It is the best to keep the power‐lines as short as possible, so local power‐
supply is preferred. This of course, depends on your demands of building‐up your system.
Page 17
FLOW‐BUS interface
9.17.024
The maximum numbers of instruments on one power supply depends of several parameters.
1.
Minimum voltage on the instrument (+15V ‐10% = 13.5V).
2.
Power supply tolerance
3.
Maximum contact rating of the connectors.
4.
Voltage drop across cables.
RJ45 cable systems use two internal wires for power supply, M12 cable systems only one.
Ω
A
l
ρ
R
Wire resistance can be done manually by the following formula:
Where “l” is the length of the conductor, measured in meters [m], “A” is the cross‐sectional area of the conductor
measured in square meters [m²], and “ρ” (rho) is the electrical resistivity (also called specific electrical resistance) of
the material, measured in ohm‐metres (Ωm)
As an example:
Wire diameter 1 mm
0.0223Ω
2
0.001
π
0.25
1
8
1.75e
R
Wire length 1 m
Copper specific electrical resistance
= 1.75 E‐8 m
= 3.14
Calculation of wire resistance and maximum wire current can also be done on:
Using standard power‐supplies from Bronkhorst and Shielded Twisted Pair patch‐cable with RJ45
connectors for non IP65 applications and DeviceNet cables with circular M12 connectors for IP65
applications:
A cluster of 4 digital controllers can be powered locally from a distance approx. <= 6.5 meters from the
power‐supply.
Powering more instruments will reduce the distance allowed to the supply‐unit in linear relationship.