5000 test maintenance, Maintenance – Parr Instrument 6400 User Manual
Page 74
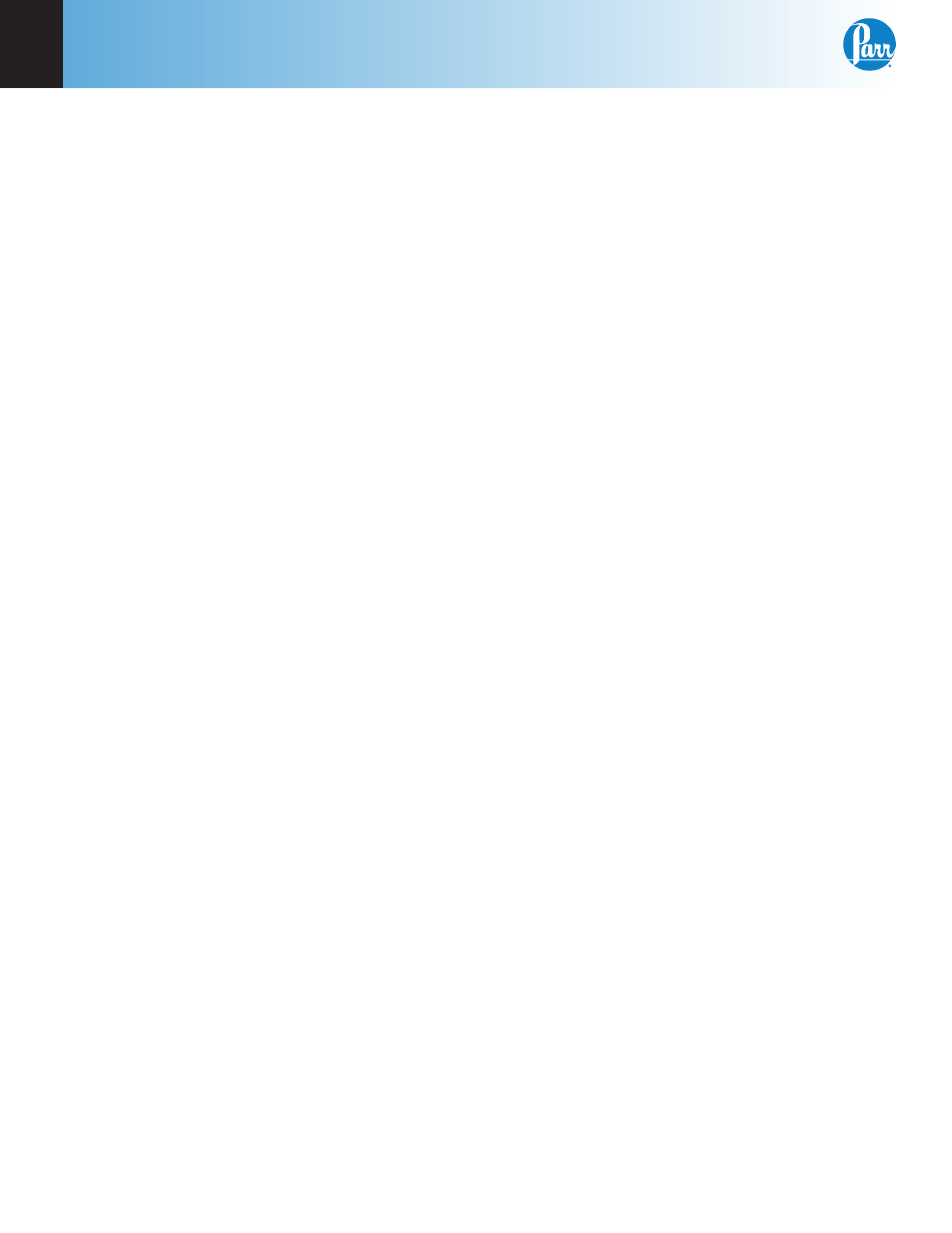
10
Maintenance
P a r r I n s t r u m e n t C o m p a n y
72
The 1140DD Seal/Release mechanism should be ser-
viced with the same frequency as the bomb head.
This includes the replacement and lubrication of the
659DDJU (2), 1138DD, 1143DD and 357HCJB O-rings
with 811DD lubricant. See Figure 14-15 and Figure
14-16 for O-ring locations. The tools required are:
screwdriver, snap ring pliers and needle nose pliers.
1. Turn off the gas supply to the calorimeter. Raise
the lid. Go to the I/O Diagnostics Screen and
turn on the bomb seal command. Turn on the O
2
Fill Command. Wait for the oxygen tube in the
lid to stop hissing. These steps are necessary
to release the gas pressure in the seal/release
mechanism before disassembling.
2. Turn off the calorimeter.
3. Insert the bomb head into the cylinder and lock
into place.
4. Disengage the screws, SA163X2RD018 that hold
the bucket in the air can. Remove the 941DD
plastic wedge that secures the front of the air
can assembly.
5. Lift the bomb and bucket as a unit from the
calorimeter air can chamber and disconnect the
bucket thermistor probe. Set this unit aside.
6. Remove the vessel spacer, 964DD and the asso-
ciated O-ring, 969DD.
7. Remove the cylinder spacer, 1141DD, which sits
on top of the snap ring, 1137DD.
8. Remove the snap ring that retains the cylinder
insert in the release mechanism at the bottom
of the air can. Withdraw both the insert and the
release pin as a unit using needle nose pliers.
9. If present, remove any scoring on the 966DD2
release pin, above the smaller O-rings, with
crocus cloth. Replace the 659DDJU O-rings on
the release pin as well as the 1138DD O-ring that
seals the cylinder insert. Replace the 659DDJU
and 357HCJB O-rings.
10. Lightly lubricate the 659DDJU (2), 1138DD,
1143DD, and 357HCJB O-rings.
11. Reverse the above procedure to reinstall the
cylinder insert/pin as well as the bomb bucket
assembly. Make sure that the large side hole
in the 1139DD insert is oriented toward the left
side of the instrument. The insert is keyed to the
cylinder and can not be fully inserted unless it is
properly oriented
5000 Test Maintenance
To deal with the realities of today’s test loads and
cycle times, the ASTM Committee recommends
in method E144 Standard Practice for Safe Use of
Oxygen Combustion Bombs that “all seals and other
parts that are recommended by the manufacturer
be replaced or renewed after each 5000th firing or
a more frequent interval if the seals or other parts
show evidence of deterioration.” Oxygen bombs
returned to Parr for service will be tested in accor-
dance with ASTM E144. A test certificate is provided
with each repair.
This service includes:
• Disassembly, cleaning and inspection of all parts
• Re-polishing of the inner surfaces of the bomb
• Re-assembly with new insulators, and seals,
sealing rings, and valve seats
• Proof testing
• Hydrostatic testing
The hydrostatic and proof testing of the oxygen
bomb should be performed after every 5000 firings
or if:
• The bomb has been fired with an excessive
charge
• The ignition of any of the internal components
has occurred
• There have been any changes in the lugs on the
bomb cylinder
• The bomb has been machined by any source
other than Parr Instrument Company
After repeated use with samples high in chlorine
(over 1%), the inner surfaces of the bomb will
become etched to the point where appreciable
amounts of metal salts will be introduced during
each combustion. Any bomb which is being used for
chlorine determination should be polished at more
frequent intervals to prevent the development of
deep pits. If the interior of the bomb should become
etched or severely pitted, the resistance of the metal
to further attack can be improved by restoring the
surface to its original polished condition.
There are no user serviceable parts inside the prod-
uct other than what is specifically called out and dis-
cussed in this manual. Advanced troubleshooting
instructions beyond the scope of this manual can be
obtained by contacting Parr Instrument Company in
order to determine which part(s) may be replaced or
serviced.