Gas piping, Table 1 — maximum capacity of pipe, Combustion-air, vent, and condensate piping – Carrier 58SX040 User Manual
Page 2: Caution, Warning
Attention! The text in this document has been recognized automatically. To view the original document, you can use the "Original mode".
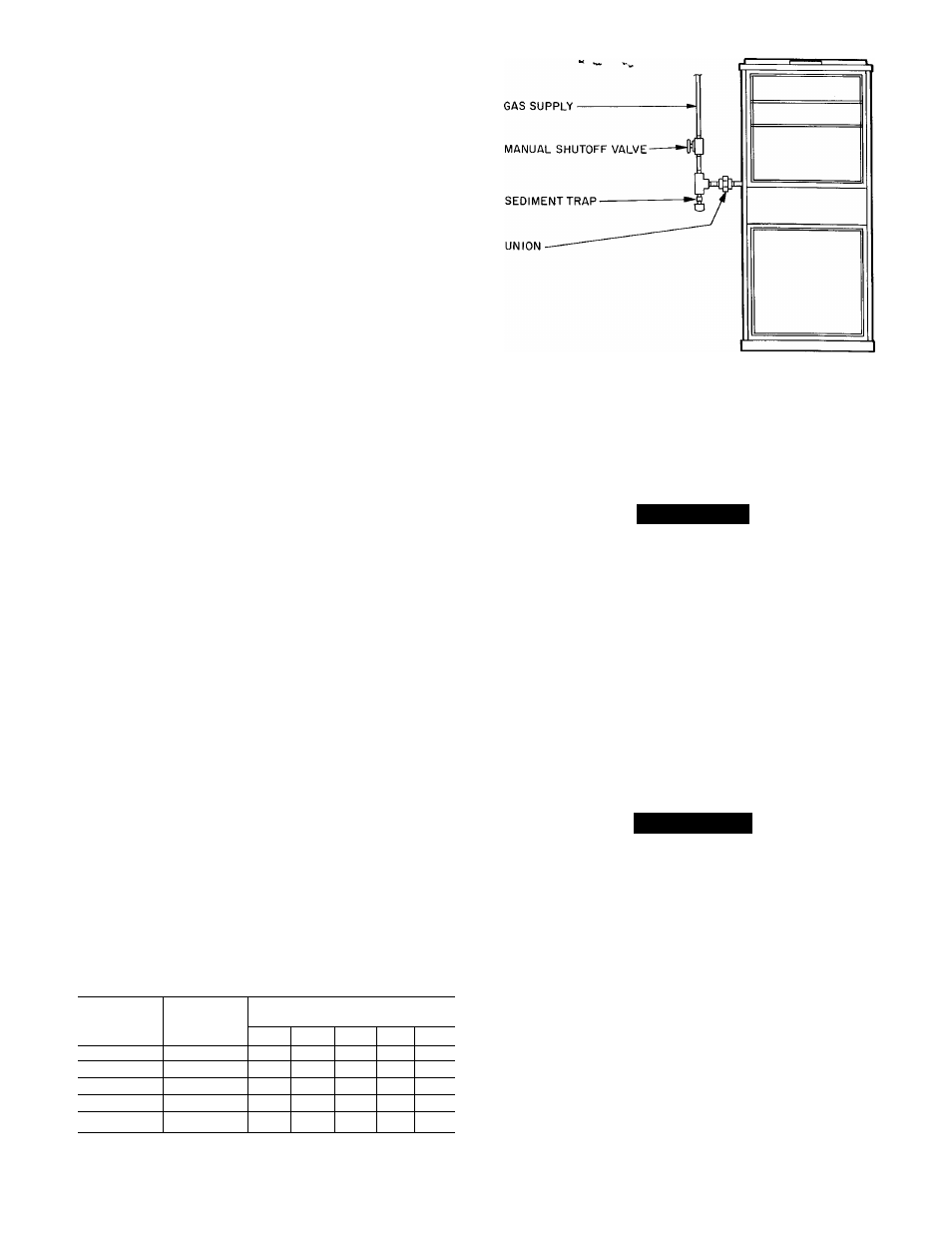
For casing ventilation purposes, provide the confined
space with 2 permanent openings, one within 12 in. of
top and one within 12 in. of bottom of enclosure. Each
opening shall have a minimum free area of one sq in /
1000 Btuh of total input rating of all equipment in
enclosure, but not less than 100 sq inches
Openings must freely communicate with interior areas
whose volume, when combined with tbe volume of the
confined space, meet the criteria for an unconfined space.
This can be accomplished through installation of either
permanent openings or louvered doors.
LOUVERS AND GRILLES — When calculating the
free area, consider the blocking effect of louvers, grilles,
or screens protecting openings Screen mesh size must
equal or exceed 1/4 inch Use the free area through the
design of the louver or grille, when known, to calculate
the opening size required to provide free area specified.
If free area is not known, assume that wood louvers will
have a 20 to 25% free area, while metal louvers and grilles
will have a 60 to 75% free area. Construct all louvers and
grilles providing combustion or dilution air so that they
cannot be closed
GAS PIPING
Gas piping must be installed in accordance with
national and local codes.
Run a separate gas supply line directly from the meter
to the furnace, if possible Table 1 shows recommended
gas pipe siziijg. Slope all pipe 1 /4 inch in 15 ft to prevent
traps. Slope all horizontal runs away from meter and
toward risers. Use risers to connect lines to furnace
and meter.
Apply joint compounds (pipe dope) sparingly and only
to male threads of joints Consult local gas supplier for
compound recommendations.
NOTE Use only compounds resistant to the action of
LP (propane) gas.
Install a sediment trap in the riser leading to the furnace
to trap dirt and condensate. Connect a tee to the riser
leading to the furnace, keeping straight-through section
of tee vertical. Connect a capped nipple into lower end
of tee, so that nipple extends below level of gas controls
(Fig. I).
Where a gum filter is required by local codes, install it
in accordance with their requirements.
An accessible manual shutoff valve must be installed
upstream of furnace gas controls and within 6 ft of
furnace. A 1/8-in. NPT plugged tapping, accessible for
test-gage connection, must also be installed immediately
upstream of gas supply connection to furnace and down
stream of manual shutoff valve.
Install a ground joint union between gas control
manifold and manual gas sbutoff valve (Fig 1).
Table 1 — Maximum Capacity of Pipe*
NOMINAL
IRON PIPE
SIZE (In.)
INTERNAL
DIAMETER
(in.)
LENGTH OF PIPE (ft)
10
20
30
40
50
'/2
0.622
175
120
97
82
73
Ÿ4
0.824
360
250
200
170
151
1
1.049
680
465
375
320
285
1V4
1.380
1400
950
770
660
580
IV
2
1 610
2100
1460
1180
990
900
Fig. 1 — Ground Joint Union and Sediment Trap
Protect all segments of the piping system against
physical and thermal damage. Support all piping with
appropriate straps or hangers (one hanger every 6 ft
minimum). For pipe sizes larger than I/2 in., follow
recommendations of national codes.
A
CAUTION
If a flexible connector is required or allowed by the
authority having jurisdiction, black iron pipe must
be installed at the gas valve and extend a minimum
of 2 in. outside the furnace casing
Pressure-test piping in accordance with local and
national plumbing and gas codes before attaching
furnace. Crack ground joint union before pressure
testing If pressure exceedsO.5 psig( 14 in. wg), disconnect
gas supply line from furnace before performing pressure
test If test pressure is equal to or less than 0.5 psig
(I4in. wg), close manual shutoff valve located on gas
valve before testing
After final connection to the furnace has been made,
purge lines and check for leakage with regulated gas
supply pressure
A
WARNING
Never purge line into combustion chamber. Never
use matches, candles, flame, or other sources of
ignition to check for gas leakage. Use a soap-and-
water solution to check for leaks.
‘Cubic ft of gas per hour, for gas pressures of 0 5 psig (14 in wg)
or less, and a pressure drop of 0 5 in wg (based on a 0 60 specific
gravity gas)
COMBUSTION-AIR, VENT, AND
CONDENSATE PIPING
Construct all combustion-air and vent pipes for this
unit of schedule40 PVC, PVC-DWV, or ABS-DWV
pipe. The accessory vent terminal kit described below
must be used in constructing the vent terminal for this
unit. Pipes must terminate through either roof or side-
wall; roof termination is preferable Locate sidewall
terminations to prevent damage to shrubs or siding
materials. Table 2 gives clearance requirements.
When a previously common-vented system (furnace
and water heater) is converted to water heater only, vent
system may be drastically oversized for water heater.
Consult National Fuel Gas Code for proper sizing and
revise vent system if necessary.