Pump – Carrier 07E User Manual
Page 7
Attention! The text in this document has been recognized automatically. To view the original document, you can use the "Original mode".
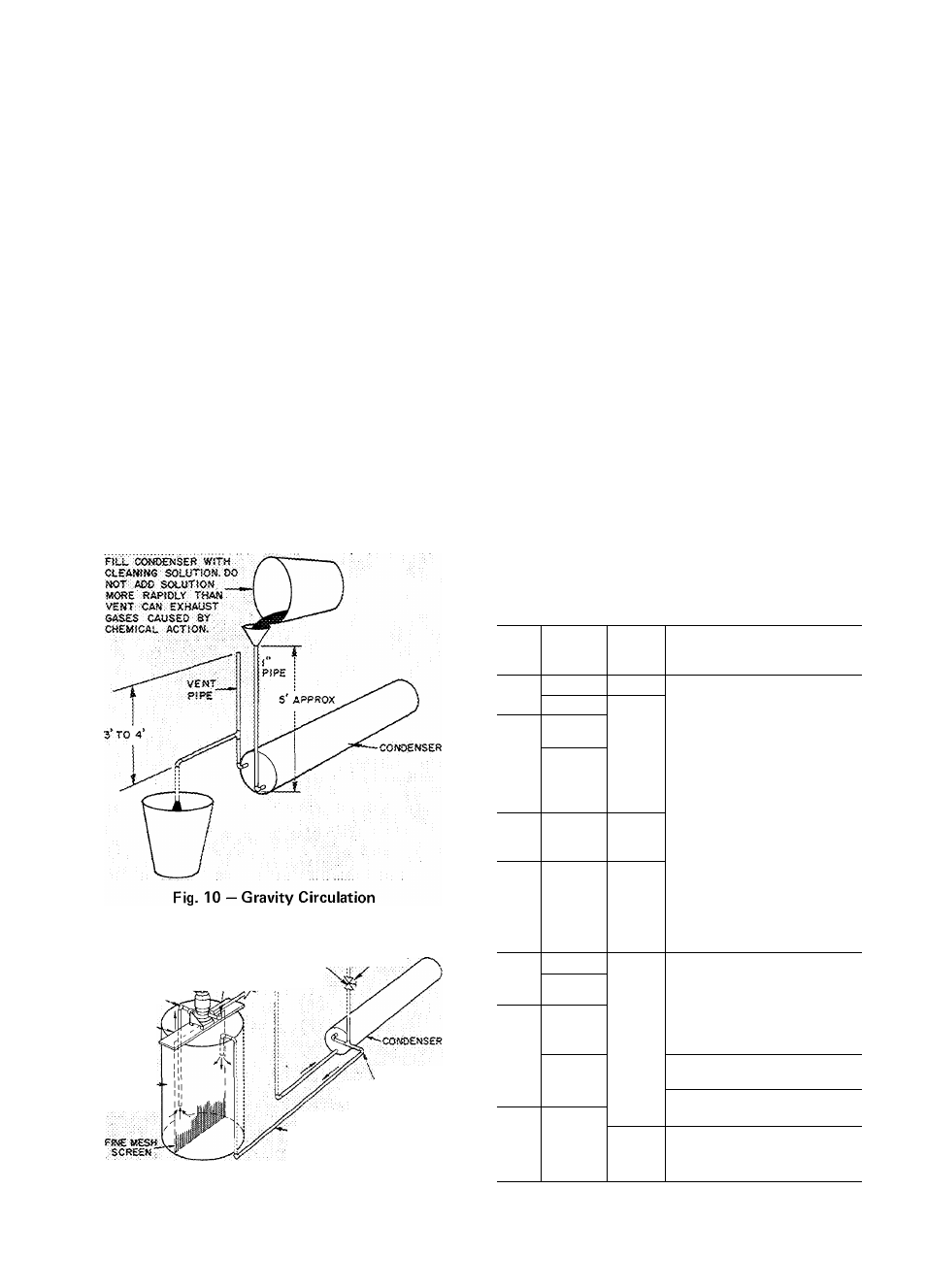
Pressure Differential Adjustment
— Turn differ
ential adjusting s,crew in counterclockwise direc
tion to its back-stop position (differential in this
position 6 psig). Pressure differential is set by
turning adjustment screw clockwise; every full turn
increasing differential by 1.5 psig. (Approximately
10 turns in clockwise direction will increase
pressure differential to 22 psig.)
CONDENSER MAINTENANCE (07E Units)
To inspect and clean condenser, drain water
and remove condenser heads. To drain condenser,
shut off water supply and disconnect inlet and
outlet piping. Remove drain plugs and vent plug.
With condenser heads removed, inspect tubes
for refrigerant leaks. (Refer to Carrier Standard
Service Techniques Manual, Chapter 1 Section 1-6,
Leak Testing, for instructions.)
Clean condenser tubes with nylon brush
(available from Carrier Service Department). Flush
water thru tubes while cleaning. If hard scale has
formed, clean tubes chemically. Do not use brushes
that will scrape or scratch tubes.
For chemical cleaning solution, use inhibited
hydrochloric acid solution (Oakite 32). Handle
C£NTfilFU<5AL
<3AS VSNT-
30 GPM AT 35* BEAD
GC03E
PRIMING /VAUvesX
CONN, /
!
i
CLOSE VENT PIPE
( VALVE WHEN
( PUMP IS
! RUNBiNG
PUMP
SUCTION
PUMP^
SUPPORT
TANK-
REMOVE WATER
REGULATING VALVE
-RETURN
acid cautiously. Clean condenser by gravity or
forced circulation (Fig. 10 and 11). For average
scale deposits allow acid solution to remain in
condenser overnight; for heavy deposits, allow 24
hours. Drain condenser and flush with clean water.
NOTE: Protect condenser from freezing when
ambient is below 32 F by draining water from
system or adding antifreeze to water.
REMOVING, INSPECTING AND
REPLACING COMPONENTS (Fig. 12)
Service Notes
1
.
2
.
3.
Where compressor components are shown they
are in normal order of removal from compressor.
All compressors have interchangeable valve
plate assemblies, unloader valves and oil pump
bearing head assemblies. For replacement items
use Carrier Specified Parts.
Before compressor is opened, the refrigerant
must be removed from it by the Pumpdown
method.
a.
Start compressor, close suction shutoff
valve, and reduce crankcase pressure to
2 psig. (Jumper low pressurestat.)
Table 4 — Torque Values
Fig. 11 — Forced Circulation
SIZE
DIAM
(in.)
THREADS
PER IN.
TORQUE
RANGE
(ft-lb)
USAGE
yi6
27 (pipe)
8-12
Pipe Plug — Crankshaft
V
4
18
20-25
Pipe Plug — Crankcase
‘/4
20
8-10
8-12
Conn. Rod Cap Screw
Junction Box
V
4
28
3-5
14-18
14-18
14-18
Sight Glass
Oil Pump Drive Segment
Unioader Valve
Discharge Valve Stop
18 (pipe)
15-24
15-24
Cover Plate — Pump End
Bearing Head
Discharge Service Valve(4 cyl)
%
16
30-40
30-40
30-40
25-30
2-4
Bottom Plate — Crankcase
Compressor Foot
Terminal Block
Oil Plug — Pump End Bearing
Head
Terminal Bolts
\
18 (pipe)
30-40
Pipe Plug — Junction Box
Xe
14
55-65
55-65
Motor End Cover
Pump End Bearing Head
Va
13
100-120
90-120
90-120
Cyl inder Head
Discharge Service Valve(6 cyl)
Suction Service Valve (4 cyl)
V»
11
90-120
90-120
Suction Service Valve (6 cyl)
Rotor Lock — Crankshaft
%
18
60-75
Oi 1 Drain Plug
%
16
105
Stator Lock
No. 6
32
1-2
Check Valve Body — Crankcase
No. 10
32
4-6
4-6
Oil Pump Drive Segment
Terminal Screw