Carrier 07E User Manual
Page 12
Attention! The text in this document has been recognized automatically. To view the original document, you can use the "Original mode".
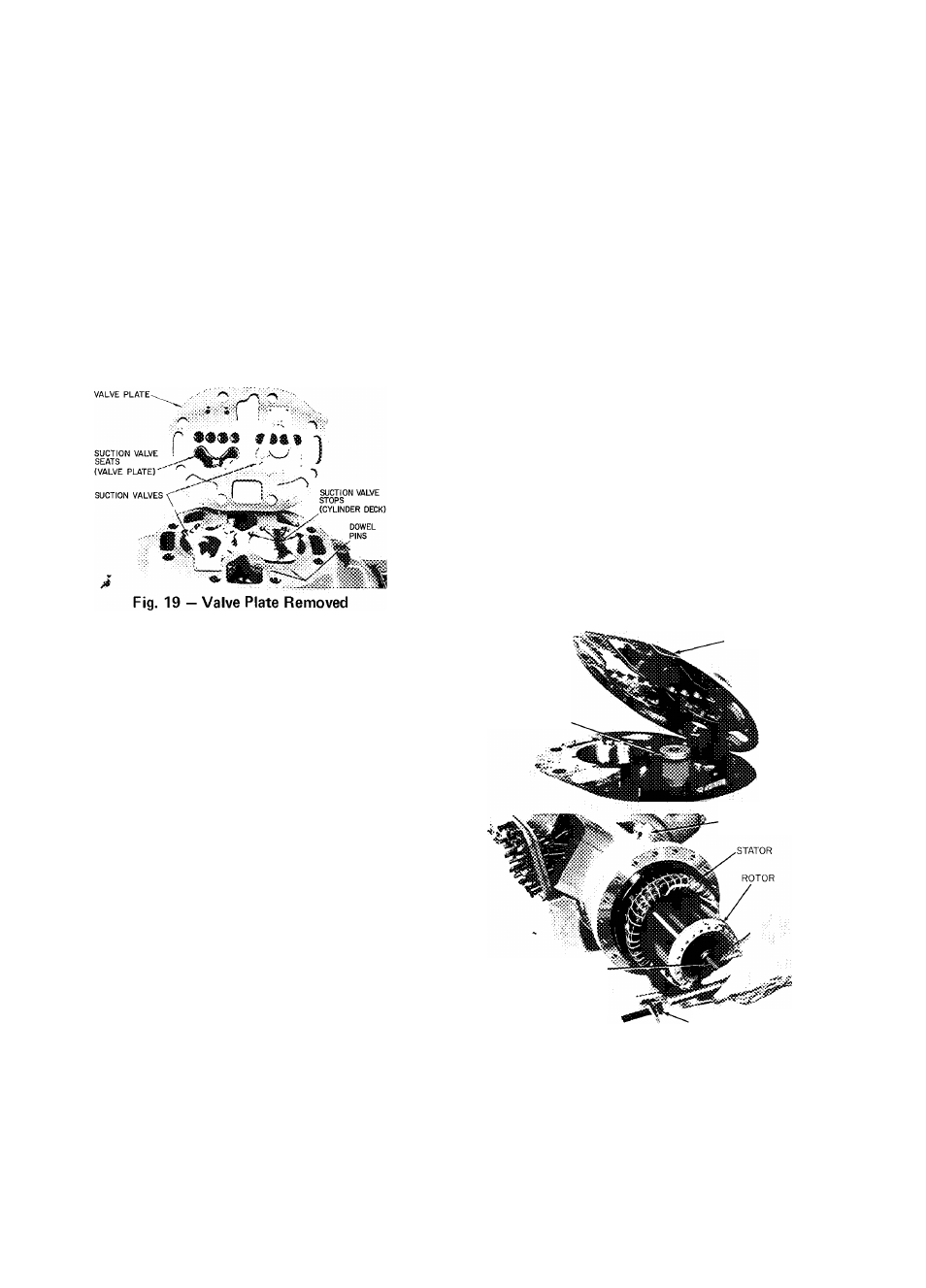
If there is an indicated loss of capacity and
discharge valves check properly, remove suction
and discharge valve plate assembly and inspect
suction valves.
Disassembly
— Remove cylinder head.
1. Remove discharge valve assembly: cap screws,
valve stops, valve stop supports and valves.
2. Pry up on side hfting tab to remove valve plate
and expose suction valves (Fig. 19). Remove
suction valves from dowel pins.
Inspect valves and valve seats for wear and
damage (see Wear Limits, Table 5). Replace valves
if cracked or worn. If valve seats are worn, replace
complete valve plate assembly.
Table 5 — Wear Limits - 06E Compressor
COMPRESSOR PART
Main Bearing Diameter
Journal Diameter
PUMP END
Main Bearing Diameter
Journal Diameter
CONNECTING ROD
Bearing Diameter
(After Assembly)
Crankpin Diameter
THRUST y,ASHER
(Thickness)
CYLINDERS
Bore
Piston Diameter
Wrist Pin Diameter
Con. Rod Wrist Pin ID
Piston Ring End Gap
Piston Ring Side
Clearance
VALVE
THICKNESS
Discharge
END CLEARANCE
Suction
FCTY TOLER
ANCES (in.)
Max Min
1 8760
1 6260
1 7515
2 6885
8755
007
003
.03J5
^'0255
■ 0'225
.031
I 8725
1.6233
I 7483
.155
2 6817
8748
.002
001
.0305
'“70245"
MAX
ALLOWABLE
WEAR* (in.)
001
’
OOP
.
002
*
002
002
.001
001
.015
002
.002
.010
"■Maximum allowable wear above maximum or below minimum fac
tory tolerances shown. For example: difference between main bear
ing diameter and journal diameter is 0035 in. (1.8760 — 1.8725)
per factory tolerances. Maximum allowable difference is 0045 in.
(.0035 -f.001).
Reassembly
— Do not interchange valves. Install
suction valves on dowel pins. Place valve plate on
cylinder deck, and reinstall' dischârge valve
assembly. Retorque discharge valve stop cap screws
to 16 ft-lb. Replace cylinder head. (Ensure tab on
cylinder head gasket is lined up with tabs on
cylinder head and valve plate.)
MOTOR REMOVAL
Motor End Bell
— Remove motor end bell carefully
to prevent damage to stator. Use 7/16 in. —
14 X 5 in. studs (3) for guides and support. Inspect
suction strainer in end bell. Clean it with solvent or
replace if broken or corroded.
Rotor
— Bend motor lock washer tab backward
and remove rotor lock bolt. If crankshaft turns,
preventing lock bolt from being loosened, remove a
cylinder head and valve plate and place a rubber
plug (06R suction plug) on top of one piston
(Fig. 20.) Replace valve plate assembly and
cylinder head (only two bolts required to hold
cylinder head in place). Proceed to remove rotor
lock bolt, lock washer and plate washer.
Use a jackscrew to remove rotor (Fig. 20).
Insert a brass plug into rotor hole to protect end of
crankshaft from jackscrew. Support rotor while it
is being removed to prevent stator damage.
Remove ring spacer between rotor and crankshaft.
Clean rotor thoroughly with solvent. If stator is
to be replaced, a matching rotor must be used.
VALVE PLATE
RUBBER PLUG
STATOR
LOCKING
ASSEMBLY
JACKSCREW'
'ROTOR LOCK BOLT
Fig. 20 — Removing Rotor
Terminal Plate Assembly
— Disassemble junction
box from terminal plate, and remove cap screws
holding terminal plate to compressor. Mark all
motor leads so they can be reassembled correctly
to terminal plate. Loosen alien head screws holding
motor leads to terminal plate (Fig. 21). Remove
terminal plate.
12