Hot alignment check and doweling, Instruct customer operator – Carrier 17DA User Manual
Page 7
Attention! The text in this document has been recognized automatically. To view the original document, you can use the "Original mode".
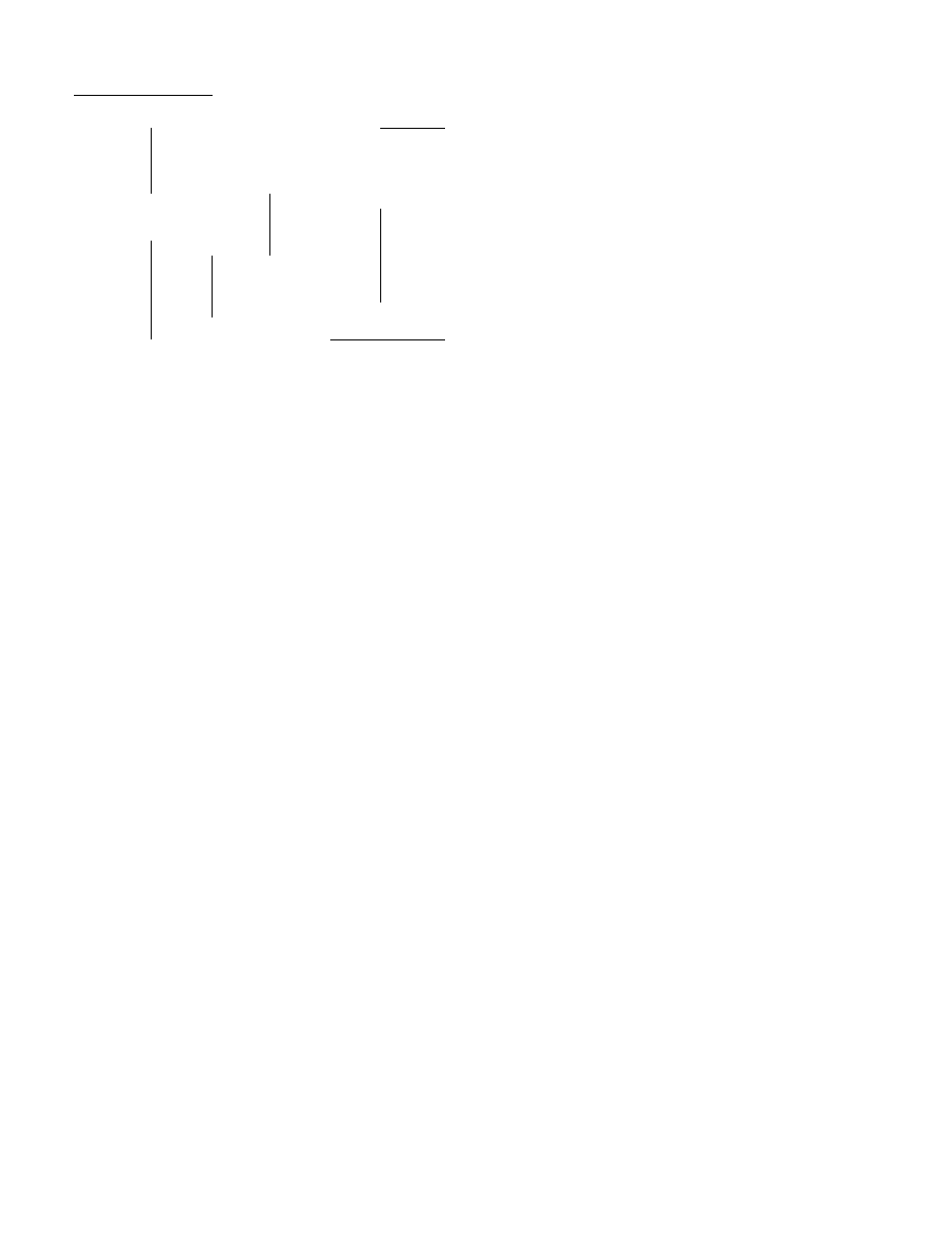
Table 5 — Typical 17DA Coder and Condenser
Refrigerant Charges (lb)
COOLER
15-FT
18-FT
22-FT
COND
REFRIG
SIZE
TUBES
TUBES
TUBES
SIZE
WT
61
3,300
3,900
4,800
61
2200
63
4,000
4,700
5,800
63
2200
65
4,000
4,700
5,800 .
65
2700
67
4,600
5,600
6,800 Î
67
2700
651*
3,500
4,200
5,100 ' 651*
2500
671*
4,200
5,000
6,100
671*
2500
71
5,100
6,100
7,500
71
2900
73
5,500
6,500
8,000
73
2900
75
6,100
7,300
8,900
75
3400
81
7,100
8,500
10,400
81
3900
83
7,600
9,200
11,200
83
4400
85
8,500
10,100
12,400
85
5100
87
9,500
11,400
13,900
87
4900
* Refrigerant 500
HOT ALIGNMENT CHECK AND DOWELING
After the machine has been running at about
full load for four hours, its components will have
come up to steady state operating temperature
conditions and the final hot alignment check may
be made.
Realign component locations until angular and
parallel alignments are within coupling manu
facturer’s specified tolerances.
Dowel all equipment into place as soon as the
hot alignment check proves that the machine is
within these running tolerances.
See Carrier Standard Service Techniques, Form
SM-15, Rev A, for these operations.
INSTRUCT CUSTOMER OPERATOR
The following is an outline guide for giving
operating instructions to the customer’s operator.
1. Present operator with copy of Operating and
Maintenance Instructions.
2. Point out machine components and explain
function and settings for each.
a. Controls
(1) S a f e t y panel, gages and safety
switches
(2) Control station, manual-automatic
modes
Compressor
(1) Oil reservoir
(2) Seal
(3) Guide Vanes
(4) Auxiliary oil pump, filter and cooler
(5) Bleed valve
Cooler
(1) Refrigerant level sight glass
(2) Pressure relieving valve
Condenser
(1) Sub-cooler
(2) Leveltrol
b.
c.
d.
e. Purge
(1) Operation
(2) Maintenance
f.
Drive and gear
g. Pumpout system (if supplied)
h. Auxiliary gages and thermometers
3. Refrigerant cycle
a. Explain system
b. Importance of log sheets
4. Describe compressor lubricating oil system.
a.
Oil heater
b. Oil cooler
c. Pressure regulating valve, back pressure
valves, etc.
d. Auxiliary oil system (if supplied)
5. Point out safety and operating controls and
explain function of each.
a. Standard controls
b. Special controls
6. Instruct proper operating procedure.
a. Preparation for start-up (valves, electrical,
etc.)
b. Starting methods
c. Running measurements and maintenance
of log
d. Shutdown
e. Extended shutdown
7. Review maintenance items.
a. Daily
b. Items to watch
c. Extended shutdown
d. Water treatment and strainer cleaning
8. Review spare parts lists.
9. Advise regarding Carrier Planned Service.
a. Maintenance contracts
b. Inspection Contracts
c. Carrier Regional Service Schools
10. Review special features of machine.
a. Operation of pumpout system and valve
settings
b. D r i v e m a i n t e n a n c e a n d operating
precautions
c. Starter settings and location
11. Leave phone number of Machinery and Systems
Division, Carrier Corp. for quick reference.
12. Review questions and answers on Operation
and Maintenance Instructions.
13. Advise on start of Warranty Period.