Charge machine with oil, Final preoperation alignment check, Operate drive – Carrier 17DA User Manual
Page 5: Set purge valves and switches, Check water supply, Check air supply, pneumatic machines, Start-up
Attention! The text in this document has been recognized automatically. To view the original document, you can use the "Original mode".
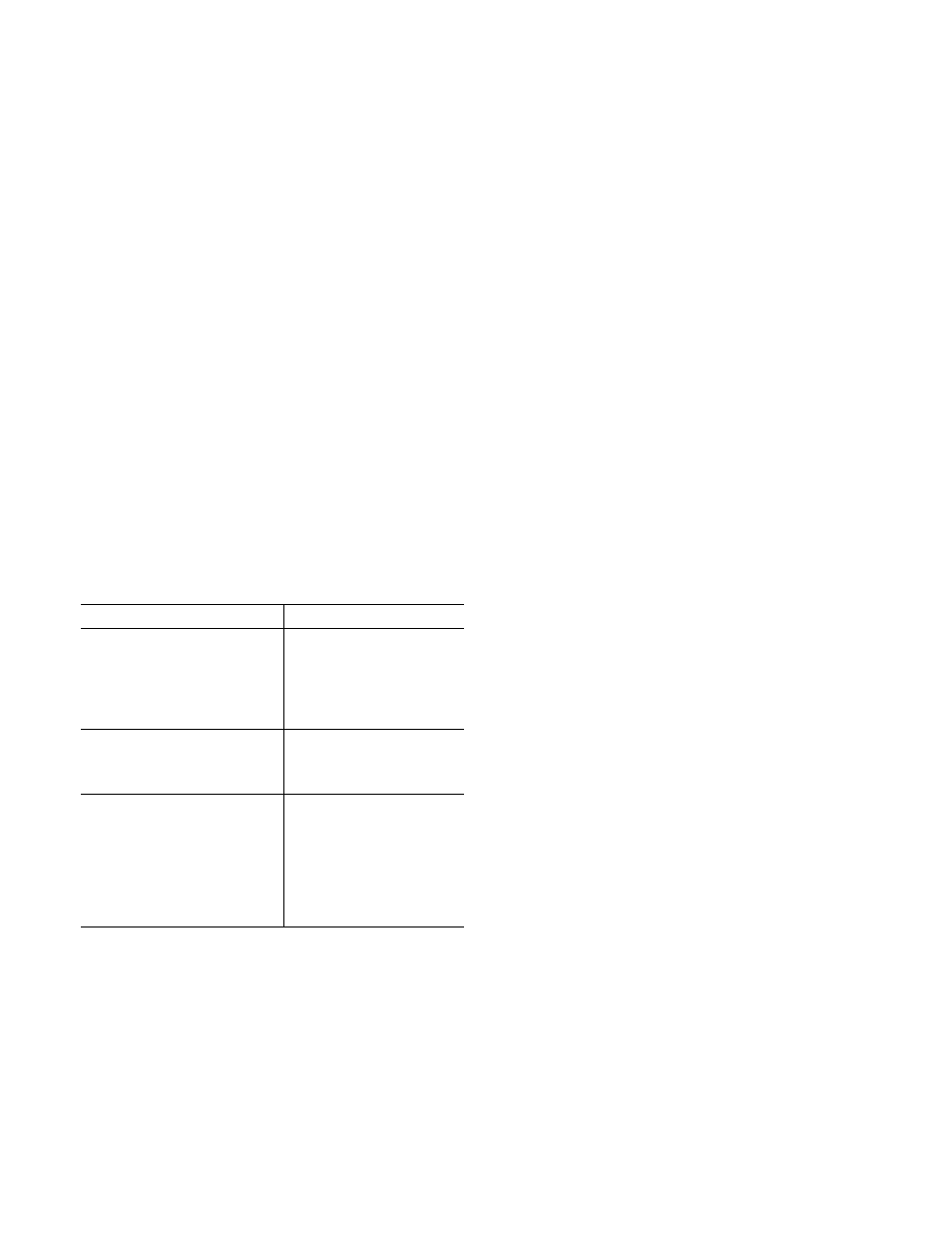
or gear to check for alignment drift while charging
with water and refrigerant. The weight of these
materials will always cause a shift in the position of
the machine components. Before and after indi
cator readings will give a good clue to the direction
final alignment should take.
CHARGE MACHINE WITH OIL
The 17DA machine has an integral lubrication
system mounted on the common base with the
compressor. A parallel auxiliary oil pump system
may also be furnished. Charge the oil system with
35 gal. of oil per Carrier Specification PP16-0
(Table 4). If oil other than this is used, the
replacement oil must be nearly equivalent.
Ensure that there is adequate lubrication prior
to the operation of all equipment. Check the gear
and drive manufacturer’s instructions for proper
initial
lubrication
procedure.
If
the
drive
machinery is to be operated before operating the
compressor, disconnect the shaft coupling and'
secure the shroud to prevent damage to the drive
shaft or the coupling.
Oil pressure from the main oil pump is set at a
pressure 35 psi greater than the back-of-seal oil
pressure. If, for any reason, the oil pressure falls to
23 psi above the back-of-seal oil pressure, the
auxiliary oil pump starts and maintains oil pressure
at a safe level.
Table 4 — Oil Specification (Carrier PP16-0)
CHARACTERISTIC
VALUE
Viscosity at 100 F
150 - 160 SSU
Viscosity at 210 F
40 - 45 SSU
Viscosity Index, minimum
90
Pour Point, maximum
0 F
Flash Point, minimum
400 F
Neut. No., maximum
.1 mg. KOFl/gm.
Rust Inhibiting Characteristics
Thematerial shall passthe
ASTM Rust Test D665-54.
Procedure A will be used
with a test period of24hr.
Oxidation Resistance
Thematerial shall passthe
ASTM Oxidation Test
D943-54 for a minimum of
1500 hr. The acid number
at the end of the test
period shall not exceed
2.0 mg. of KOH per gram
of oil.
SSU
— Saybolt Seconds Universal
FINAL PREOPERATION ALIGNMENT CHECK
Prior to operating the compressor and speed
increasing gear (if used), coupling alignment and
separation must be checked.
1.
Ensure that coupling alignment is within
coupling manufacturer’s specified tolerances.
2.
The hub separation tolerances are normally
stamped on coupling and vary depending on
coupling size.
3. When checking hub separation, electric motor
shaft must be in center position of shaft float.
If realignment is required, follow instructions
supplied by coupling manufacturer. Carrier Standard
Service Techniques, Form SM-15, Rev A, also de
tails realignment techniques.
OPERATE DRIVE
It is good practice to operate the drive sep
arately before operating compressor. Refer to drive
manufacturer’s instructions for drive protection
devices and settings. Check turbine overspeed at
this time. Reassemble couplings after operating
drive separately.
SET PURGE VALVES AND SWITCHES
Open all the purge service valves behind purge
console. Place purge operating valves in NORMAL-
AUTOMATIC position (shown on chart inside
console door). Place purge switch in AUTO,
position.
CHECK WATER SUPPLY
Be certain that chilled water, condensing water
and oil cooler water supplies are available and that
pumps will run before operating compressor.
CHECK AIR SUPPLY, PNEUMATIC MACHINES
Make sure that control air is 35 psig.
START-UP
Preoperation Settings
— Complete these settings
before starting compressor for first time.
Drive Operation
— Refer to drive manufacturer’s
start-up
instructions.
Complete
drive
starting
requirements before operating compressor.
If drive is wired for automatic starting, it will
start when compressor START button is pushed.
Starting procedure of manually started drives may
be initiated after START button is pushed.
Compressor Operation
1. Place control switch in ON position. Con
denser pressure, bearing temperature and
refrigerant temperature indicating lights on
control console should come on.
2. Place capacity control switch in MANUAL
position.
3. Open oil cooler water plug cock. Check fqr
water flow at open sight drain.
4. Open bleed valve on inboard side of the
compressor.
5. Open all valves and energize heater on seal oil
drain pot.
6. Open all valves in chilled water and condenser
water circuits.