Inspect and adjust – Carrier 17DA User Manual
Page 3
Attention! The text in this document has been recognized automatically. To view the original document, you can use the "Original mode".
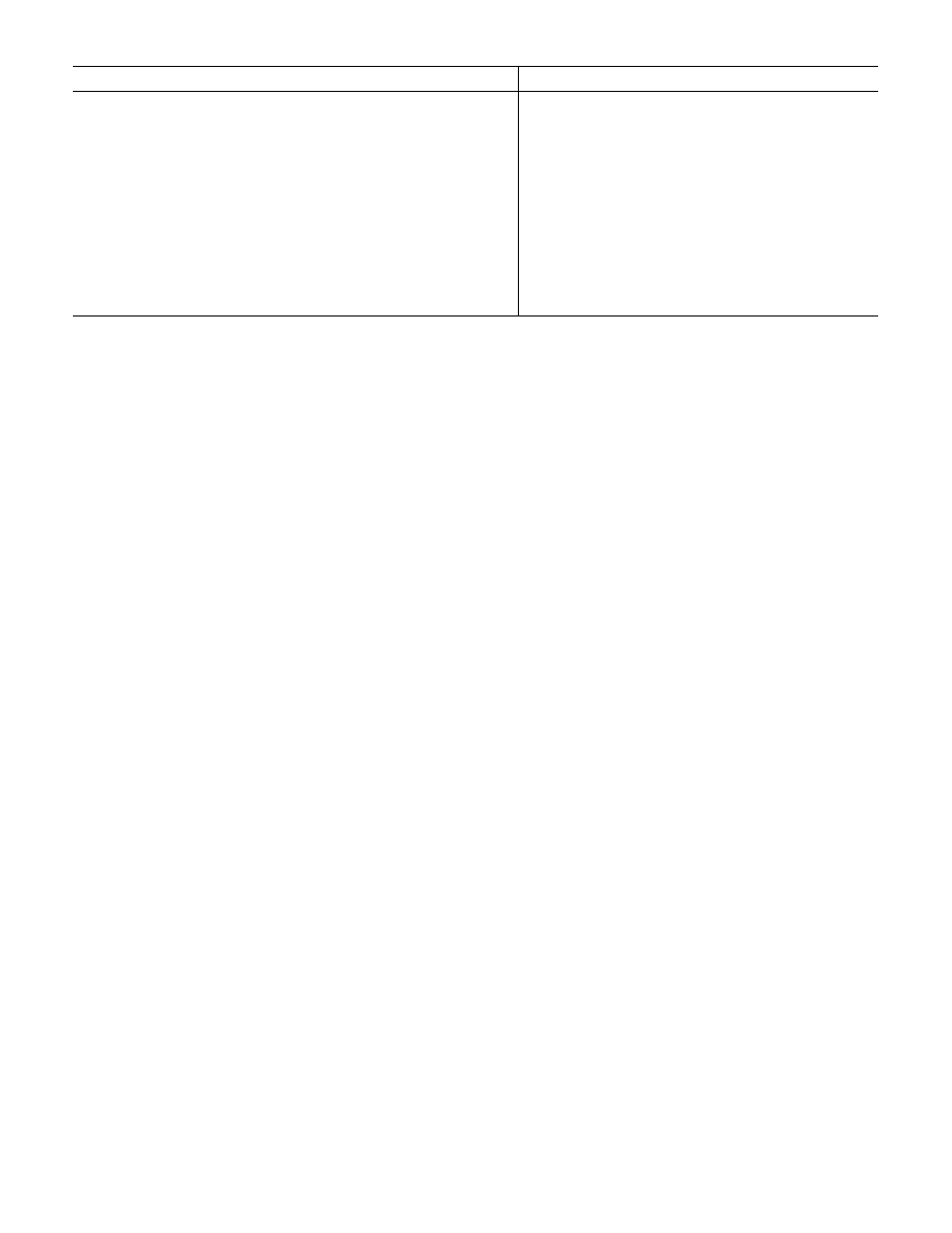
Table 1 — Essential Tools
ITEM
USE
1. Mechanic's tools
1. Machine piping connections, control calibration
2. Día! indicators
2. Check alignment
3. Volt-ohmmeter
3. Calibrate controls
4. Drum charging valve
4, Refrigerant charging connection
5. 5/8-inch SAE X 3/4-inch MPT adopter
5. Cooler charging valve
6. 5 to 10 ft length of 5/8-lnch soft copper tubing with 5/8-inch
6. Charging line
flare nut on each end
7. Halide leak detector or electronic leak detector'
7. Leak testing machine
8. Low-pressure indicator such as:
8. Check machine dehydration
a. Absolute pressure manometer or
b. Vacuum indicator
9. Portable dehydration vacuum pump — 5 or 7.5 cfm capacity
9. Dehydrating machine
10. 1/2-inch flare plug
10. Block purge suction line during leak testing
Essential Tools
— See Table 1 for tools and
materials required to perform initial start-up.
INSPECT AND ADJUST
Machine Room
— All installation work as outlined
in 17DA Installation Instructions book should be
completed, and all construction debris must be
removed
from
the
immediate
area
of
the
machinery prior to initial start-up of the machine.
Drive Arrangement
— Inspect drive mounting,
location, couphng, speed rating, etc., for agreement
with job blueprints and specifications. Gear assem
bly (if used) must agree with installation recom
mendations
outlined
in
gear
manufacturer’s
instructions.
Piping
— Check the following installations:
1. Refrigerant pumpout system
2. External or auxiliary oil system
3. All bypass lines and valves
4. Turbine drive piping, i.e.
a.
Blowdown valves for each turbine stage
installed per manufacturer’s instructions.
b.
Oil lubrication piping for speed control
installed in agreement with blueprints.
c. Steam supply Une condensate traps properly
installed to keep condensate out of turbine.
d. Proper supports on steam supply and ex
haust line to prevent stress or strain on the
turbine at operating temperatures.
5. Gas engine drive piping — Check the following
piping for agreement with job blueprints:
a. Gas pressure reducing valves with shutoff
valves.
Engine coolant piping with coolant thermo
static valve installed so that water flows in
direction marked on valve.
Oil cooler package piping
Exhaust piping
WARNING: Exhaust piping is critical.
Refer to drive manufacturer’srecominen-
dations for installation of exhaust piping.
b.
c.
d.
Wiring
— Refer to job wiring blueprints. All wiring
must agree with these prints.
AUXILIARY EQUIPMENT WIRING - Check the
following:
1. Brine pump
2. Condenser water pump
3. CooHng tower fan motor
4. Auxiliary oil pump
5. Oil heater
6. Overload selections in all motor starters. Over
load values must agree with motor nameplate
data.
TURBINE
DRIVE
WIRING
-
Check
the
following:
1. Turbine solenoid trip mechanism.
Auxiliary oil pump if used. Check pump starter
for proper voltage, amperage, and overload
setting. Operate pump to determine direction
of rotation. Do not operate dry of oil.
Check job drawings for other electrical devices
used with the turbine. Ensure that their wiring
agrees with the job wiring blueprints.
GAS ENGINE DRIVE WIRING - All wiring must
agree with job wiring blueprints. Refer to engine
manufacturer’s instructions for starting techniques.
Safety Controls
— It is good machinery practice to
preset safety controls using standard temperature
sources; i.e., ice baths, warm circulating oil baths
with standard calibrated thermometers. All con
trols must be rechecked during machine operation
and given final calibration as required. See Table 2
Control Settings and Fig. 1 17DA Safety Instru
ment Panel.
Check the following safety controls as shown
on job blueprints:
1. Main drive de-energizing devices, i.e.
a. Starter holding coil
b. Turbine solenoid trip, etc.
2. Brine low-temperature cutout
3. Refrigerant low-pressure cutout
2
.
3.