Electrical pin-out – TruTrak EFIS AP (8300-057C) User Manual
Page 22
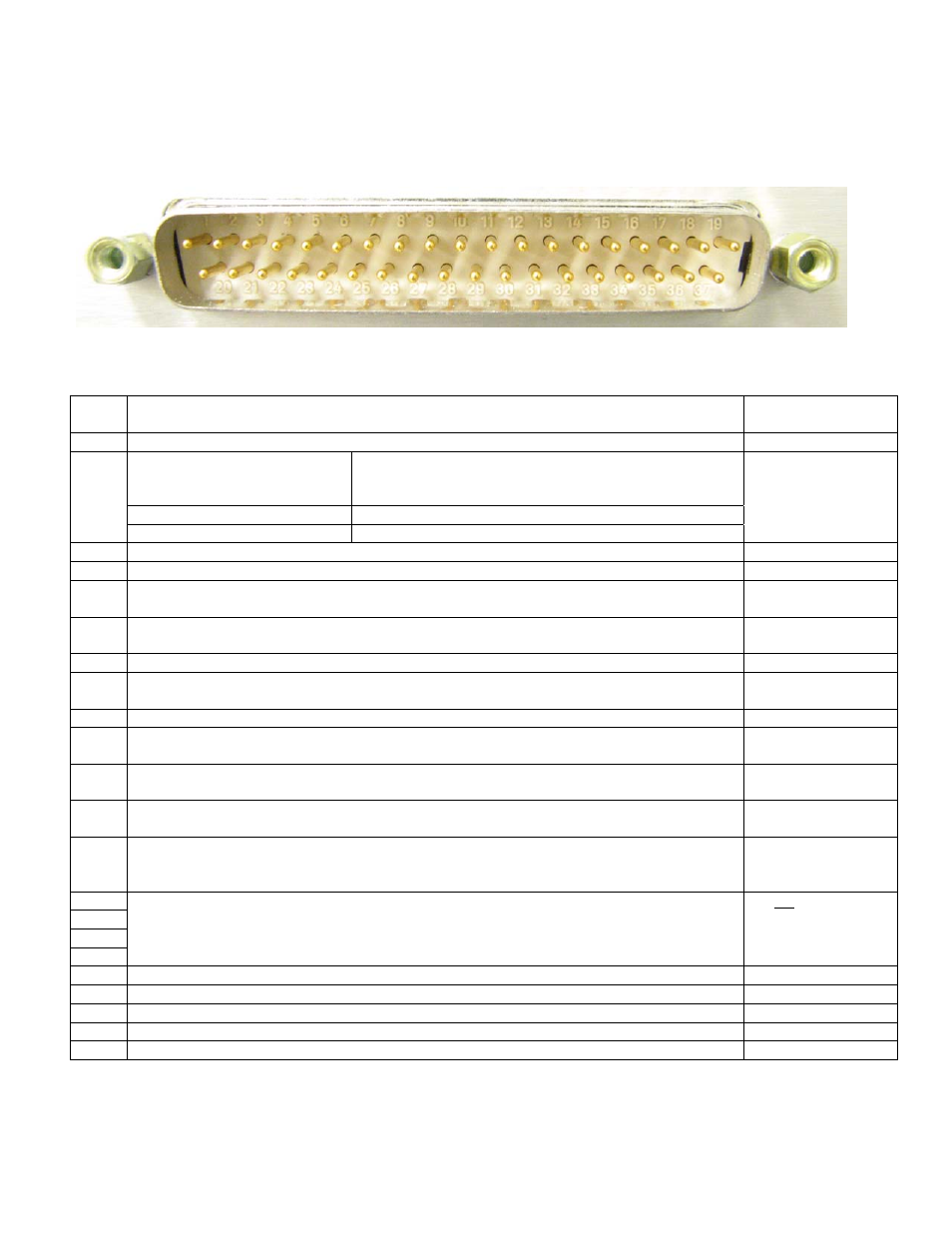
TruTrak Flight Systems
20
EFIS Autopilot Installation Manual
April 2009
8300-057 Rev D
Electrical Pin-out
EFIS with Yaw Damper will be covered in this manual.
The table below provides a brief explanation of each pin function on the main 37-pin connector P101.
P101 Autopilot Rear Connector (Viewed from rear of autopilot) or wire side of connector.
P101
Pin
Function
Notes
1 Dedicated ground connection for Pitch Reverse Jumper.
Pitch Reverse Jumper,
present or absent, as follows:
Direction of servo arm / capstan rotation
(as viewed from face of the servo body)
for UP elevator
Pin 2 open (no connect):
Servo CCW (counter-clockwise) Î UP
2
Pin 2 Jumper to pin 1:
Servo CW (clockwise) Î UP
3 NAV / TT Converter box RS-232 Output.
SL-30 NAV pin 4 RX
4 Dimmer
connection
5 Yaw Damper Activity. A signal from the autopilot which sets the amount of response the yaw
damper exhibits to azimuth disturbances and “ball” deflection.
EFIS with Yaw
Damper only
6 Yaw Damper Centering. A signal from the autopilot which is used for fine adjustment of the
“ball” in a yaw damper.
EFIS with Yaw
Damper only
7 AP illumination, To AP LEVEL Button lamp
8 Yaw Damper Activate. A signal from the autopilot which turns on the yaw damper function.
EFIS with Yaw
Damper only
9 No
Connection
10 Pitch Servo Torque Control. A signal from the autopilot to the pitch servo which sets the
amount of torque to be delivered by the servo.
11 Pitch Servo Trim Sensor. A signal from the pitch servo to the autopilot which indicates an
out-of-trim condition and its direction.
12 Autopilot Master (+12 to +28 V DC). The autopilot itself draws less than 3 ampere. Most of
the current required by the autopilot system is used by the servos (up to 1.5A per servo).
13 Audio signal Out. This pin may be wired to an unswitched input of an audio panel. The
autopilot uses various voice or tones to denote specific events (loss of GPSS, capture
Glideslope, etc). Volume is adjustable within a setup screen of the autopilot.
14
15
16
17
Pitch Servo control lines. These lines cause the stepping motor in the pitch servo to run in the
appropriate direction at the desired velocity. They are small-signal lines and do not have any
substantial current-carrying capability or require any special shielding. Connect to pitch servo
as shown on wiring diagram.
Do not attempt to
reverse servo
direction by
swapping wires
18 Future
Use
Unavailable at this time
19 Power Ground Connection. Provide #20 AWG to common grounding point.
20 CWS / AP LEVEL Button.
21 EMS
switch
Switch to ground
22 NO
CONNECTION