Initial setup & ground checkout, Ust be performed before first flight – TruTrak EFIS AP (8300-057C) User Manual
Page 18
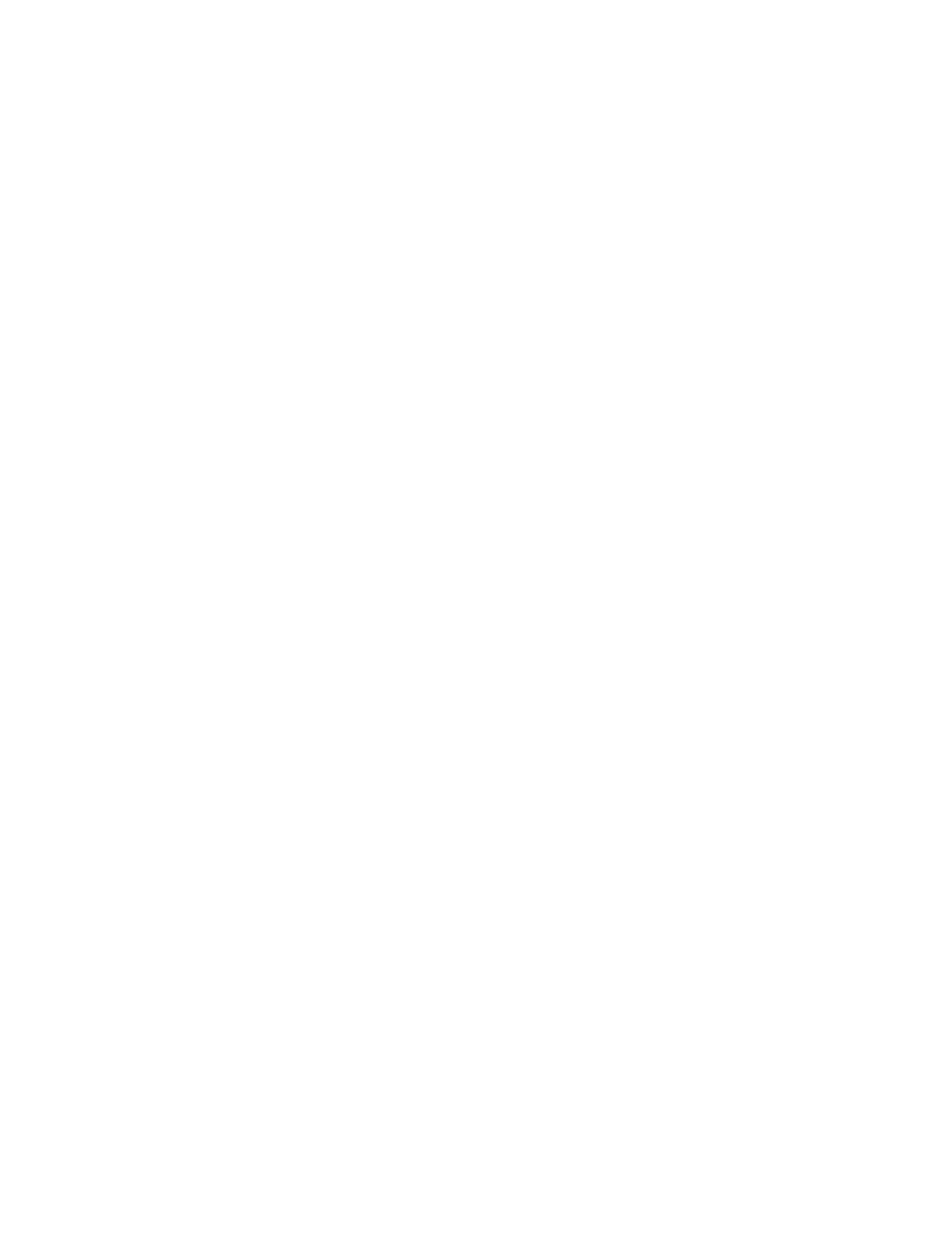
TruTrak Flight Systems
16
EFIS Autopilot Installation Manual
heckout
ust be performed before first flight
llation are completed, the autopilot should be tested in the aircraft while on
. The first step is to enter the setup modes on the autopilot and set all parameters to their
orrect values. Apply power to the EFIS autopilot. After approximately five seconds, the EFIS autopilot
tion above to set the different settings.
e sure and Set the airspeeds for
he next step in the checkout procedu is to
rify that all servos run, and in the correct direction. Power
roximately five seconds for EFIS warm-up. Then CLICK the AP
is point, the
TRK
and the
AP
will turn green and with AP III and IV,
VS
to indicate that they are autopilot controls on the display; the
will be shown below the
VS
on the right. For autopilots with option
y clicking the ALT button. Then push down on the tail (empennage)
ch the elevator movement. The elevator MUST move in the direction
. If AP III or IV then use the Vertical Speed knob to set selected
ready. The pitch servo should stop, or move only very slowly. Now
several hundred feet per minute is showing on the SEL
VS
field. At this
movi
te e kno
howing on the SEL
VS
field, the pitch servo should be moving the controls
forward
to lower the nose
t, install or remove the jumper between pins 1 and 2 of the autopilot
he roll servo should also be responding at this time, rotate the left knob to move the green bug back to 0
stop or move only very slowly. Rotated the knob clockwise from
ted a TRK to the right, the control yoke or stick MUST move in such a
Conversely, a rotation of the knob counter clockwise will move the
ols in the opposite direction to attempt a roll towards the left. If servo direction is not correct, the
ires going to pins 4 and 5 of the roll servo (pins 32 and 33 on the main connector) must be reversed to
chieve the correct response. If a servo does not move at all, double check the wiring, power and ground
pins 2, 3, 4, and 5 on the servo) to that servo for continuity and correctness. If the servo does not seem to
ave any torque, check the relevant torque control line for continuity and correctness. The voltage on pin
e AP engaged. Also if there is not adequate current
servo will not move without help.
m or capstan is properly operating the controls. For servo installations
heck that as the controls go from limit to limit the arm of the servo remains in the
perating range of the servo (a maximum of 100 degrees total rotation) and that when the controls are
is approximately perpendicular to the arm of the servo. For capstan
ng remains at proper tension and is properly secured as the servo moves the
ontrols from stop to stop. Insure that the servo remains secure in its mounting and does not flex its
ounting bracket as it drives the control to its stops. For installations using an arm, insure that as the
ervo moves the control towards the end of control travel it does not cause the main control’s torque tube
Initial Setup & Ground C
M
Once wiring and servo insta
the ground
c
is ready to be setup for operation.
UP SCREENS sec
Follow the SET
B
your aircraft before first flight!
T
re
ve
up the EFIS autopilot and wait app
button to engage the autopilot. At th
the SET BARO will change to SEL
selected vertical speed (“SEL
VS
”)
II, you must engage the ALT hold b
or lift up if a tail dragger and wat
that you are moving the empennage
vertical speed to zero if not there al
rotate the knob clockwise until
point, the pitch servo should be
ng the control yoke or stick
back
, in an effort to raise the nose of
the aircraft. Similarly, rota
th
b
ter clockwise until minus several hundred feet per minute is
coun
s
of the aircraft. If direction is incorrec
connector.
T
if not there already. The servo should
the current selected
TRK
to a selec
way as to roll the aircraft to the right.
contr
w
a
to the servos. If a servo jitters but does not actually rotate, check the wiring on the four servo drive lines
(
h
6 of the servo should be approximately 5 volts, with th
on the power and ground wires the
At this time, check that the servo ar
using an arm, c
o
centered, the connecting pushrod
systems, insure that the cabli
c
m
s
April 2009
8300-057 Rev D