TriangleTube 110 Solo User Manual
Page 67
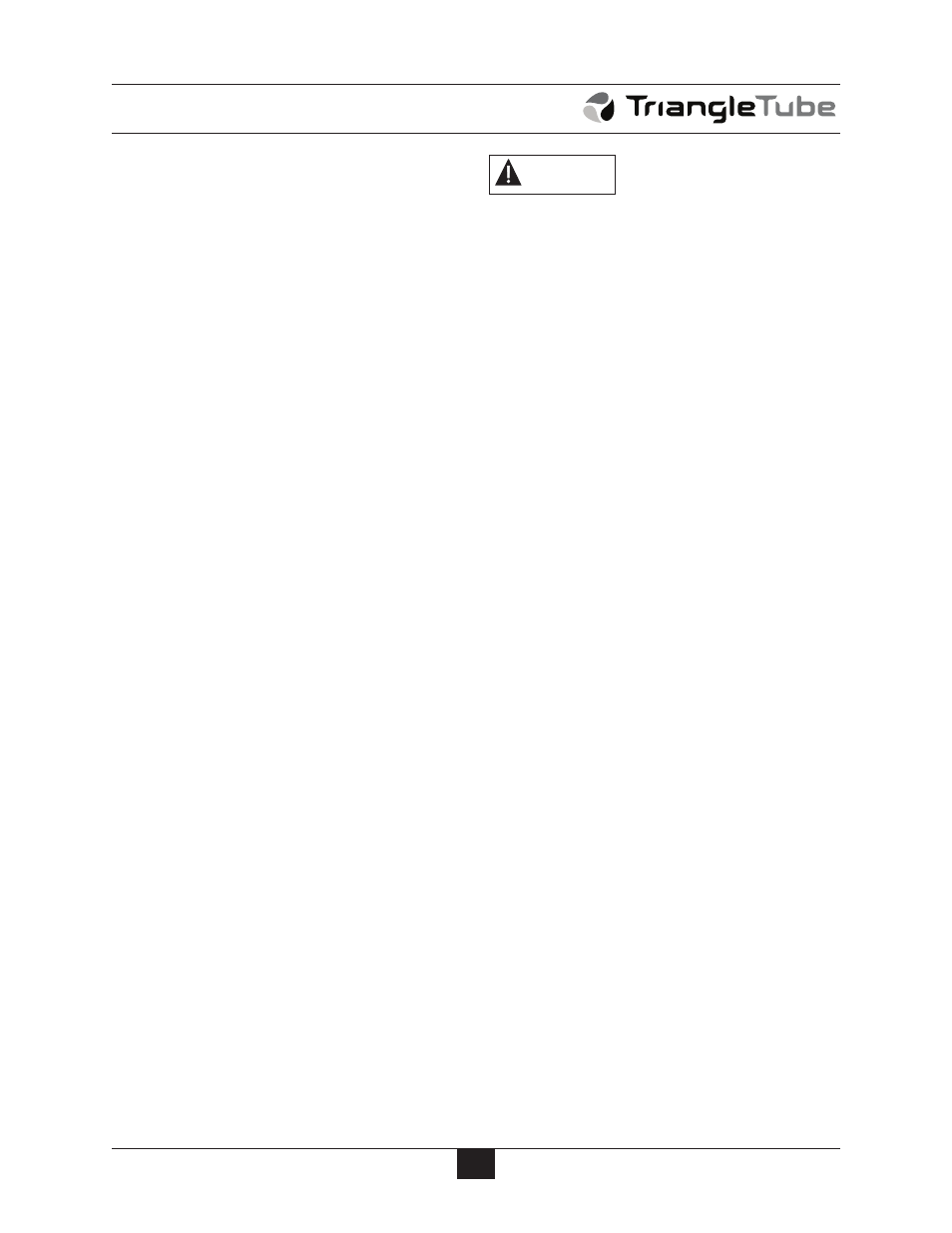
61
Maintenance Procedures
Check Expansion Tank
Refer to Section IV - Boiler Piping for rec-
ommended location of the expansion tank
and air eliminators.
Close -Type Tank:
-
Ensure tank is partially filled with
water leaving an air gap as a cushion.
Refer to the manufacturer’s instruction
for proper fill level.
-
Ensure the tank is fitted with a device
that reduces gravity circulation of air-
saturated tank water back into the sys-
tem. This device prevents air from
bubbling up through the water as it
returns from the system.
-
Ensure no automatic air vents are used
in the system. This will allow air to
escape from the system instead of
returning to the tank.
Diaphragm Tank:
-
Ensure the system contains a minimum of
one automatic air vent. Recommended
location of the air vent should be atop an
air eliminator.
-
Remove the tank from the system and
check the charge pressure. For residen-
tial applications the charge pressure is
typically 12 psig. If tank does not hold
a charge pressure, then the membrane is
damaged and the tank should be
replaced.
Check Boiler Relief Valve
Inspect the relief valve and lift the lever to ver-
ify flow at least annually or as recommended
on the warning tag of the valve.
Before manually operating the pressure
relief valve, ensure the discharge piping is
directed to a suitable place of disposal to
avoid a potential scald hazard. The dis-
charge piping must be full size without
restriction and installed to permit com-
plete drainage of both the valve and line.
If after closing the valve, the valve fails to seat
properly or continually weeps, replace the
relief valve. Ensure the cause of the relief
valve to weep is the valve itself, not due to sys-
tem over-pressurization caused by an expan-
sion tank that is waterlogged or undersized.
Inspection of Ignition Electrode
Remove the ignition electrode from the burner
mounting plate.
Remove any white oxides accumulated on the
electrode using fine grit sandpaper or steel wool.
If the electrode does not clean to a satisfactory
condition, replace the ignitor .
When replacing the ignition electrode, ensure
the gasket is in good condition and correctly
positioned, replace gasket if necessary.
Check Ignition Wiring and Ground Wiring
Inspect the burner wiring from the burner con-
trol module to the ground terminal behind the
control panel.
Ensure wiring is in good condition and secure-
ly connected.
Check ground continuity of the wiring to the
boiler jacket or piping using a continuity meter.
Replace and correct ground wire if ground con-
tinuity is not completed and satisfactory.
WARNING