Top Flite TOPA0310 User Manual
Page 44
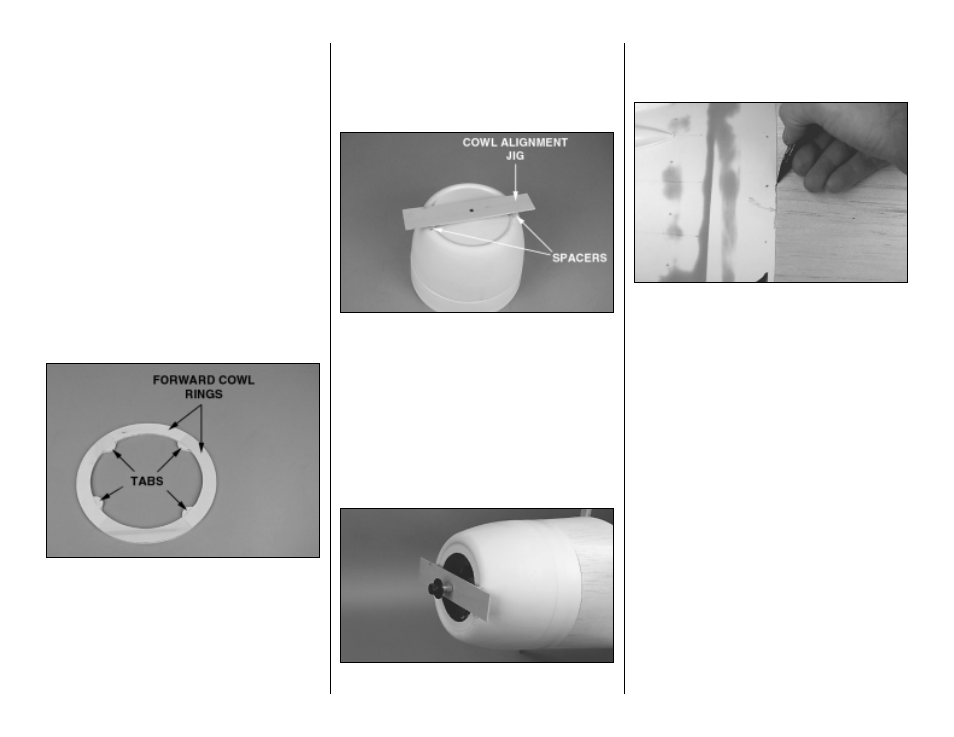
“tabs” on the cowl ring sections are where the cowl
mounting screws will be located, so position the tabs
where you will be able to access the mounting
screws, taking into consideration the positioning of
the engine, exhaust, and whatever other systems
you plan to install inside the cowl. If necessary, trim
the extension box to accommodate the cowl ring
sections (as we have done to our prototype seen in
the photo). Position the tabs over the 1/4" firewall if
possible.
Note:
It may be necessary to trim the ends
of the cowl ring sections so they will all fit together on
the firewall. From now on the joined assembly of the
four aft cowl ring sections will be referred to as the
aft cowl ring
.
❏
7. Temporarily hold the aft cowl ring to the firewall
with a few drops of CA or 3M
®
77 or 75 spray
adhesive.
❏
8. With the aft cowl ring temporarily held to the
fuse, glue the four die-cut 1/8" plywood
forward
cowl ring sections
and the four die-cut 1/8"
plywood
tabs to the aft cowl ring. Note that the joints
in the forward cowl ring sections
do not
align with
the joints in the aft cowl ring. From now on this
assembly will be referred to as the
cowl ring
.
For
illustration the cowl ring shown in the photo is off the
firewall, but yours should be on the firewall.
❏
9. Temporarily secure the cowl ring to the firewall
with four #2 x 3/8" screws. Be certain a small “ledge”
exists where the 1/8" fuse sheeting steps down to the
cowl ring for the thickness of the cowl. If necessary,
trim the cowl ring.
❏
10. Drill a 1/4" hole in the exact center of the cowl.
Make a
cowl alignment jig
by drilling a hole to fit the
crankshaft of your engine in a piece of leftover 1/8"
plywood or balsa. Align the hole in the jig with the
hole you drilled in the center of the cowl, then
temporarily glue the jig to the cowl with spacers in
between to set the desired prop clearance (1/4" is
recommended).
❏
11. The jig will center the front of the cowl on the
engine, so now cut the opening in the front of the
cowl as shown in the following photo.
❏
12. Fit the cowl to the fuse with the cowl alignment
jig on the engine. Be certain the molded-in
dimples
that indicate the location of the cowl blisters straddle
the centerline on the top and bottom of the fuse.
❏
13. Little by little, trim the aft edge of the cowl for
a good fit to the fuse.
Hint:
Scuff the outside of the
cowl so you can use a pencil to make marks. As you
“zero in” on the fit of the cowl to the fuse, mark the
high spots that interfere with a good fit to the fuse,
then remove the cowl and sand where you marked.
Test fit, mark and trim as necessary.
❏
14. After you are satisfied with the fit of the cowl
to the fuse, remove the cowl and the cowl ring. Use
a 1/4" drill to enlarge the holes in the firewall left by
the #2 screws. Use epoxy to glue four
6-32 threaded
inserts
into the holes.
❏
15. Enlarge the holes in the cowl ring with a 5/32"
drill bit, then test fit the cowl ring to the fuse with four
6-32 x 5/8" socket head cap screws, #6 lock washers
and #6 flat washers.
❏
16. Remove the cowl ring. Cover the entire firewall
with a piece of waxed paper, then remount the cowl
ring. Position the cowl on the fuse, confirm alignment,
then glue the cowl to the cowl ring with a mixture of
epoxy and microballoons to keep it from flowing.
❏
17. Blend the fuse to the cowl by sanding where
necessary. Remove the cowl and take off the cowl
alignment jig.
- 44 -