Slant/Fin Gas Steam User Manual
Page 10
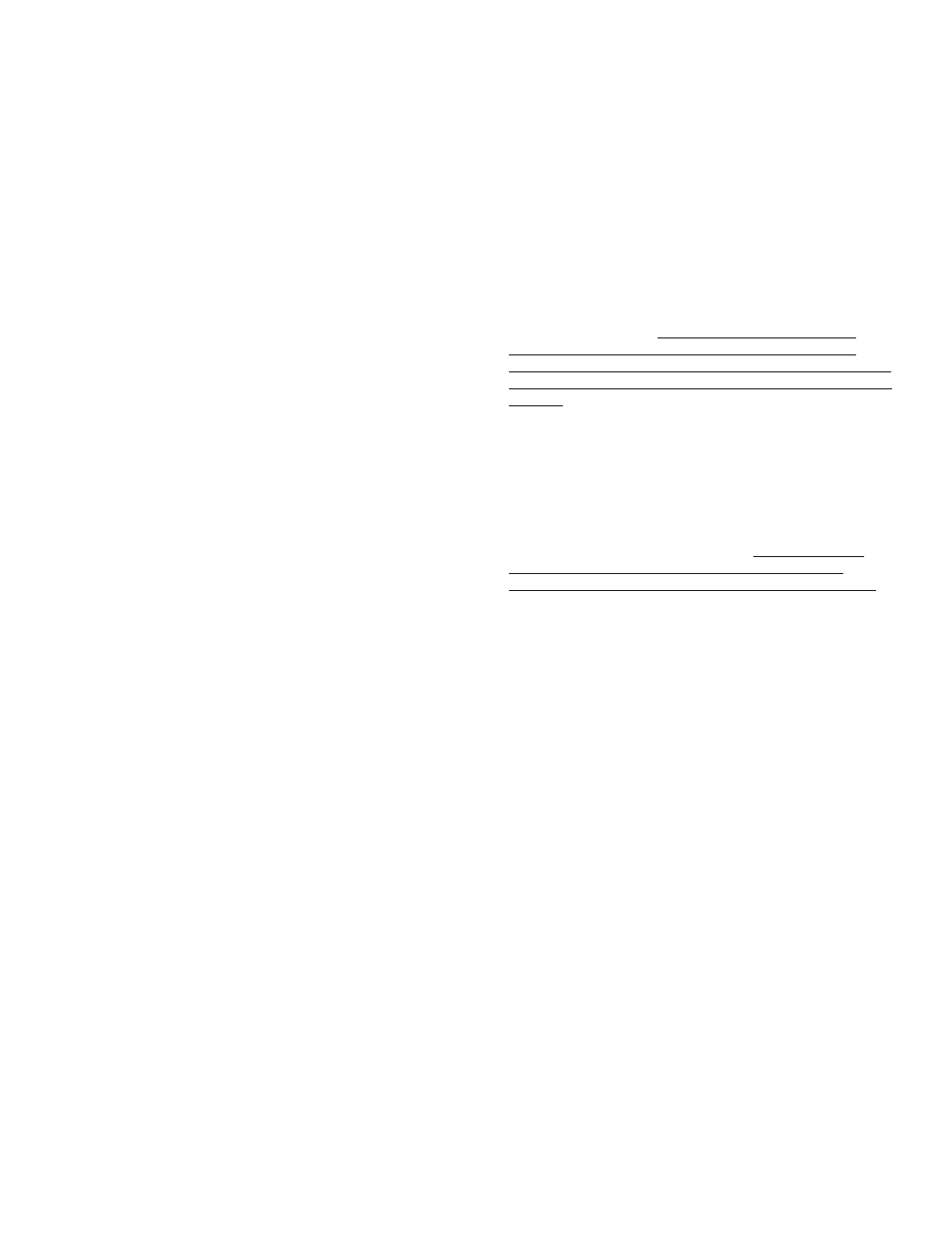
10
INSTALLATION AND PIPING RECOMMENDATIONS
When one or more steam boilers are replaced with a new
Caravan modular boiler system, there are certain conditions that
must be considered.
1.
All modules must be set on a level surface, and individually
leveled.
2.
When setting gas fired Caravan systems on a raised base, at
least 3 inches of the base must extend beyond the front and
sides of the bank of modules. This will ensure a smooth
pattern of combustion air entering the combustion chamber.
3. Leave a minimum of 7 inches between gas steam modules to
accommodate return piping, skimmer tapping, gauge glass
and low water cut off.
4. The module supply pipe must be increased from 2
1
⁄
2
" x 6" to
at least 3" (see figure 10, page 9). As shown, a 2
1
⁄
2
" x 6"
nipple is installed in the module supply tapping followed by
3" x 2
1
⁄
2
" reducing coupling and a 3" supply pipe. The 2
1
⁄
2
" x 6"
nipple is necessary to provide the needed clearances to
remove the pressure relief valve for servicing and
replacement. To minimize pressure drop, no more than
three 90 elbows should be installed between the module
supply tapping and the steam header (see figure 9, page 9).
5. All banks of modules must have an equalizer/drain line from
the supply header to the return header. This equalizer/drain
should be located at the end of the header that the system
steam supply is taken from. The equalizer/drain should be the
same size as the supply header (see figure 8, page 9). The
supply & return header for each bank should be sized
according to Table 8, page 9.
6. To prevent accumulation of condensate, steam headers
should be pitched down in the direction of steam flow and
toward the equalizer/drain with no reduction in size. Module
connections must be on the side of the header (horizontal) or
at any angle between the side and top of header, never
between the side and bottom. To prevent condensate in the
header from re-entering the boiler supply pipe, side connec-
tions must enter a header that is at least one size larger than
the boiler supply connections. Top or 45˚ top-angle connec-
tions are preferred and can enter a header of the same size
or larger. See Figure 9.The supply header for each module
should be sized according to Figure 10, page 9.
7. The supply connection between the building steam main and
the module steam header should be located between the last
boiler on the header and the equalizer/drain. Connection
must be at least 2 header diameters from the last module
(see Figure 8, Page 9).
8. Piping should provide a means for both surface and bottom
blow-down and flushing sediment from the system for clean,
safe and efficient operation (see Figures 11 and 12, Page 11
and Fig. 7 page 8).
9. The use of a pump control is recommended to regulate the
water level in a bank of boilers and prevent the bank from
operating with an unsafe low water condition. For protection
of banks with 2 to 5 modules, the control should be located
on the equalizer line. All applications require a low water
cut-off on each module and one cut off for each bank.
10. Supply and/or return shut-off valves on individual modules
are not recommended. However, if valves on individual
modules are unavoidable, additional safety controls are
required on each module. Full-port valves should be used to
minimize pressure drop and should be the same diameter as
the pipe.
11. Impurities and oxygen in fresh water cause scaling and leave
deposits in the boiler and surrounding pipes. This leads to
inefficient operation and other system problems. The older
the system, the greater the probable accumulation of scale.
Therefore, it is necessary to check the piping for blockage or
restriction and clean or replace the piping as required.
Applications such as process systems can result in excessive
introduction of fresh water into a steam boiler. This will dam-
age the boilers and void any warranty. Caravan modular
boiler systems are not recommended for applications
involving the use or discharge of raw steam or condensate.
In all cases, boiler water should be tested periodically to
determine if conditioning treatment is needed. Consult a
local boiler water treatment expert.