Making the chamber hypoxic, Pass box operation – Shellab BACTROX User Manual
Page 14
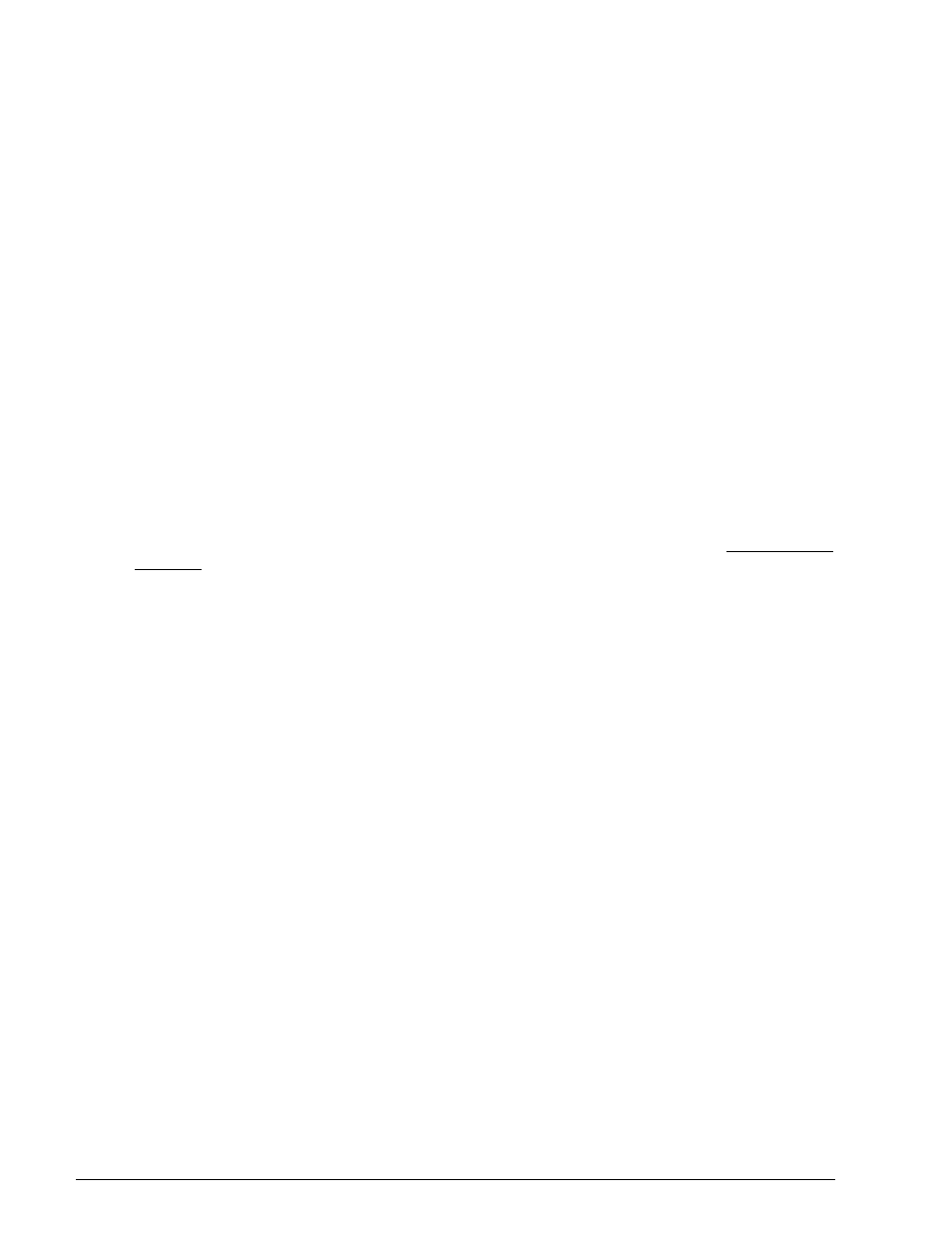
__________________________________________________________________________
Bactrox Operations Manual 14
10.5
Initial Control Settings: Each Bactrox comes preset from the factory at 37C and the O
2
and
CO
2
set to off. You should allow the incubator to heat up and stabilize for 24hrs. Turn the SET
OVERTEMPERATURE control clockwise until it stops so that it does not activate during the
initial warm up.
10.6
Calibrating the Controls for Temperature or CO
2
:
10.6.1 Push and hold BOTH the UP and DOWN buttons simultaneously for five (5) seconds.
10.6.2
If you are calibrating temperature, the Temperature Display panel will read “CO” and
then blink.
10.6.3 If you are calibrating CO
2
Level, the CO
2
will read “CO” and then blink.
10.6.4 While the display is blinking use the UP and DOWN buttons to adjust the display to
match the actual condition in the incubator chamber.
10.6.5 If no buttons are pressed within five (5) seconds the blinking will stop and the display will
revert to showing the process or actual parameter within the incubator chamber.
11.
MAKING THE CHAMBER HYPOXIC
11.1
Prior to Purging the Chamber
:
Turn Power switch to the “O” (Off) position.
11.2
Connect Nitrogen and Carbon Dioxide Gas supplies as directed in the Bactrox Appendix.
11.3
Open the incubator doors before leaving the chamber. This allows the incubator to become
hypoxic at the same rate as the workspace.
11.4
Put arm port doors in place, or the Arm Port Sleeve Plugs
NOTE: The Bactrox chambers have an efficient method for sealing the chamber by utilizing the Arm port
doors as shown in Figure 3. The tightening knob on the Arm port doors should be snug, DO NOT OVER
TIGHTEN. Damage can occur if too much force is placed on the Arm port door assembly. When the
knob just begins to “grab”, the tightening bolt has reached its maximum point. Over tightening will cause
the bolt to slip inside the handle and cause leakage.
Purging the Chamber
11.5
Turn Power
Switch to the “I” (On) position on the Control Module.
11.6
Note the reading on the gas regulators.
11.7
Set the Oxygen Setpoint to the desired value using the up and down arrows.
11.8
Set the Carbon Dioxide Setpoint to the desired value using the up and down arrows.
11.9
The Oxygen controller will automatically add Nitrogen gas or ambient air to achieve the desired
setting. Normally, it takes 1-1/2 to 2 hours to achieve a 1% concentration of O
2
inside the
chamber workspace, after initialization from ambient air.
11.10 The CO2 control module will automatically add Carbon Dioxide gas or Nitrogen to achieve the
desired setting. Normally, it takes ~45 minutes to achieve a 1% concentration of CO
2
inside the
chamber workspace, after initialization from ambient air.
11.11 If a precise control of the O2 concentration is required, refer to the calibration section of this
manual, to enter a custom calibration. The O
2
module is calibrated at the factory for two point
curve at 1% and 20.7%.
Summary
The chamber is ready when:
The
“SET OXYGEN %” led display reads the desired concentration of oxygen.
The
“SET CO 2%” led displays reads the desired concentration of oxygen.
The
“SET TEMPERATURE” controller displays the desired value. NOTE: It may take several
hours to overnight to achieve temperature stability after the incubator doors are closed after
initialization.
12.
PASS BOX OPERATION
12.1
Load the PASS BOX with samples, materials, supplies, etc.
12.2
Close the outer and inner PASS BOX Doors.
12.3
Activate the PASS BOX