Table 1—dimensions (in.), Fig. 1—dimensional drawing – Carrier WEATHERMAKER 8000 58ZAV User Manual
Page 2
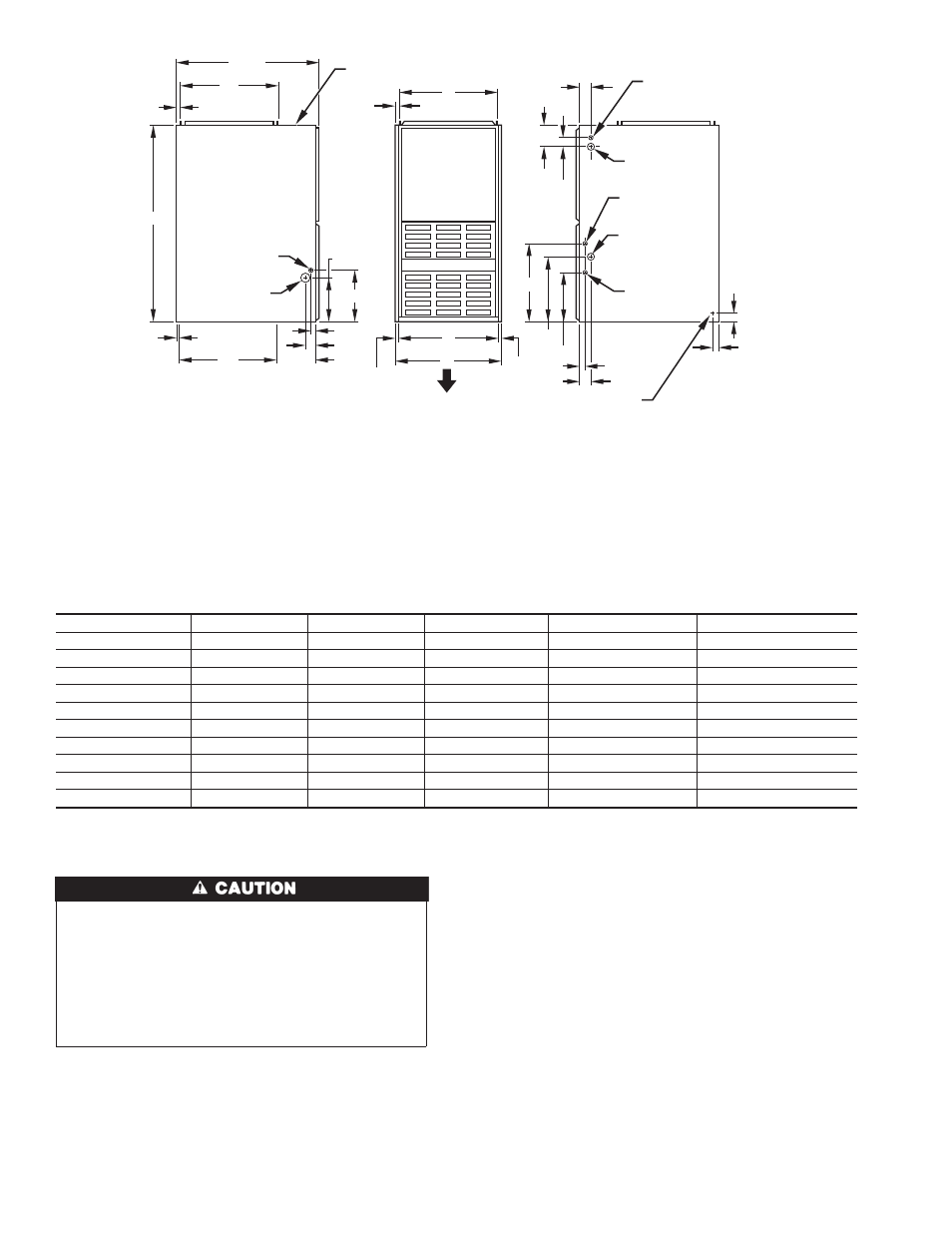
ELECTROSTATIC DISCHARGE (ESD) PRECAUTIONS
PROCEDURE
Electrostatic discharge can affect electronic components.
Take precautions during furnace installation and servicing to
protect the furnace electronic control. Precautions will pre-
vent electrostatic discharges from personnel and hand tools
which are held during the procedure. These precautions will
help to avoid exposing the control to electrostatic discharge
by putting the furnace, the control, and the person at the same
electrostatic potential.
1. Disconnect all power to the furnace. DO NOT TOUCH THE
CONTROL OR ANY WIRE CONNECTED TO THE CON-
TROL PRIOR TO DISCHARGING YOUR BODY’S ELEC-
TROSTATIC CHARGE TO GROUND.
2. Firmly touch a clean, unpainted, metal surface of the furnace
chassis which is close to the control. Tools held in a person’s
hand during grounding will be satisfactorily discharged.
3. After touching the chassis you may proceed to service the
control or connecting wires as long as you do nothing that
recharges your body with static electricity (for example; DO
NOT move or shuffle your feet, DO NOT touch ungrounded
objects, etc.).
4. If you touch ungrounded objects (recharge your body with
static electricity), firmly touch furnace again before touching
control or wires.
5. Use this procedure for installed and uninstalled (ungrounded)
furnaces.
6. Before removing a new control from its container, discharge
your body’s electrostatic charge to ground to protect the
control from damage. If the control is to be installed in a
furnace, follow items 1 through 5 before bringing the control
or yourself into contact with the furnace. Put all used AND
new controls into containers before touching ungrounded
objects.
7. An ESD service kit (available from commercial sources) may
also be used to prevent ESD damage.
Table 1—Dimensions (In.)
UNIT SIZE
A
D
E
VENT CONN
SHIP. WT (LB)
050-08
14-3/16
12-9/16
12-11/16
4
124
050-12
14-3/16
12-9/16
12-11/16
4
128
070-08
14-3/16
12-9/16
12-11/16
4
129
070-12
14-3/16
12-9/16
12-11/16
4
137
096-12
17-1/2
15-7/8
16
4
146
096-16
17-1/2
15-7/8
16
4
151
115-16
17-1/2
15-7/8
16
4
159
115-20
21
19-3/8
19-1/2
4
174
115-22
21
19-3/8
19-1/2
4
176
135-20
24-1/2
22-7/8
23
5
193
Fig. 1—Dimensional Drawing
A99288
4
3
⁄
16
″
2″
2
15
⁄
16
″
13
⁄
16
″
11
⁄
16
″
9
1
⁄
8
″
10
1
⁄
4
″
1
1
⁄
16
″
2
1
⁄
8
″
8
1
⁄
4
″
10
1
⁄
4
″
1
1
⁄
16
″
2
1
⁄
8
″
16
1
⁄
16
″
13
5
⁄
16
″
19″
11
⁄
16
″
13
⁄
16
″
11
⁄
16
″
20″
28
1
⁄
2
″
39
7
⁄
8
″
D
5
⁄
8
″ TYP
1″ TYP
E
A
AIRFLOW
OUTLET
INLET
1
⁄
2
″ DIA
THERMOSTAT
WIRE ENTRY
7
⁄
8
″ DIA
ACCESSORY
7
⁄
8
″ DIA
ACCESSORY
DIMPLES TO DRILL HOLES
FOR HANGER BOLTS (4 PLACES)
IN HORIZONTAL POSITION
ADDITIONAL
7
⁄
8
″ DIA K.O.’s ARE
LOCATED IN THE TOP PLATE
AND BOTTOM PLATE
NOTE:
7
⁄
8
″ DIA HOLE
POWER ENTRY
1
1
⁄
2
″ DIA
R.H. GAS ENTRY
7
⁄
8
″ DIA
ACCESSORY
1
3
⁄
4
″ DIA HOLE
GAS ENTRY
VENT CONNECTION
Minimum return-air openings at furnace, based on metal duct. If flex duct is used,
see flex duct manufacturer's recommendations for equivalent diameters.
a. For 800 CFM–16-in. round or 14
1
⁄
2
x 12-in. rectangle.
b. For 1200 CFM–20-in. round or 14
1
⁄
2
x 19
1
⁄
2
-in. rectangle.
c. For 1600 CFM–22-in. round or 14
1
⁄
2
x 23
1
⁄
4
-in. rectangle.
d. For airflow requirements above 1800 CFM, must use entire return air opening.
NOTE:
2