Flintec LDU 69.1 User Manual
Page 15
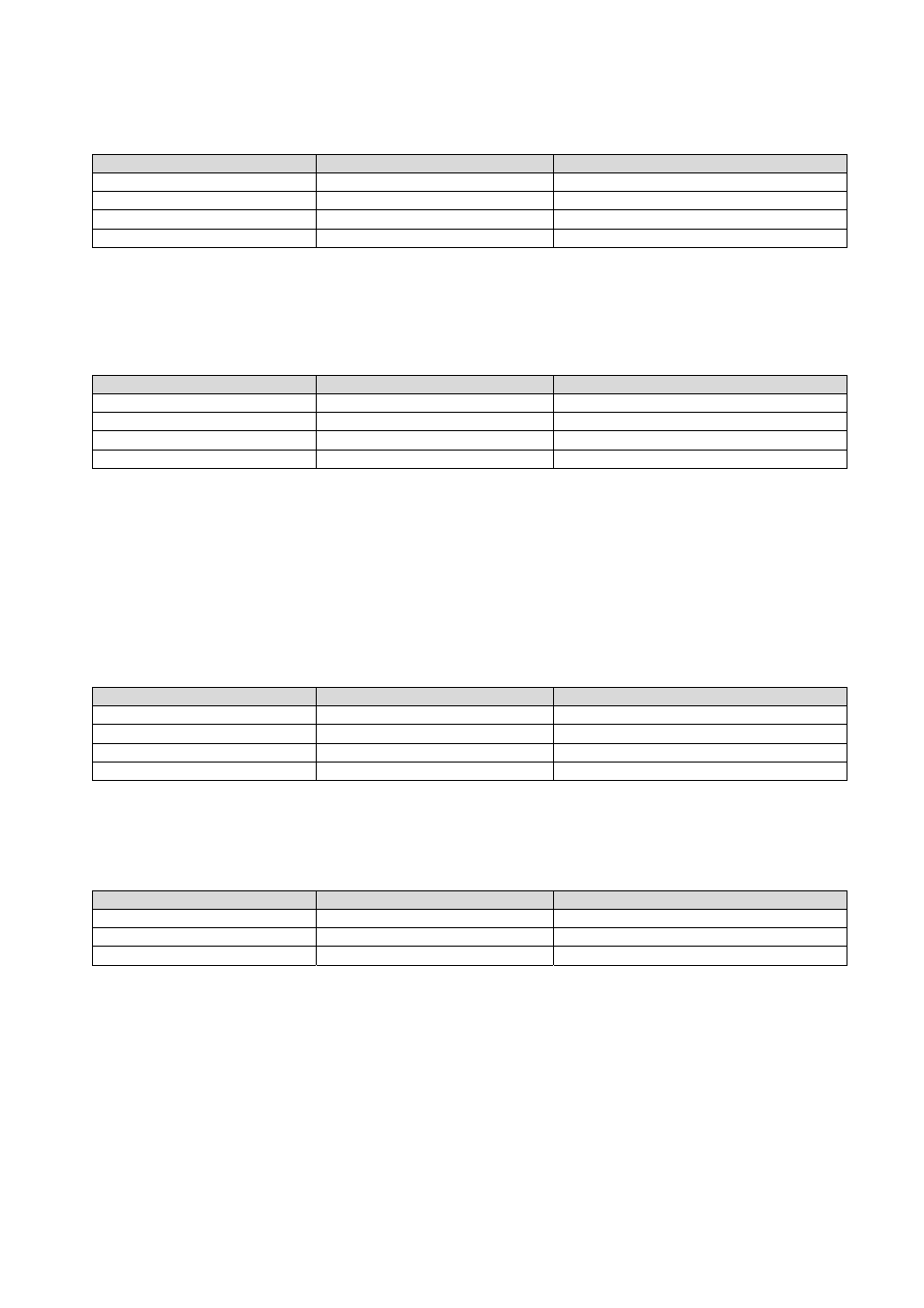
LDU 69.1 Technisches Handbuch, Rev. 12 January 2011
Page 15 of 28
8.2.4. MR Set Multi-range / Multi-interval
This command is only relevant, if CM 2 > 0 or CM 3 > 0. Is this the case,then this command defines, if the
application is multi-range or multi-interval. Permitted values are 0 (Multi-interval) or 1 (Multi-range).
Master (PC / SPS) sends
Slave (LDU XX.X) responds
Meaning
MR
M+00000
Request: MR = 0 (Multi-interval)
CE
E+00017
(example)
Request: TAC counter CE17
CE 17
OK
Calibration sequence active
MR 1
OK
Setup: MR = 1 (Multi-range)
Note:
Single range applications ignore this parameter.
8.2.5. DS
Set Display Step Size
This command allows the output to step up or down by a unit other than 1.
Permitted values are 1, 2, 5, 10, 20, 50, 100 and 200.
Master (PC / SPS) sends
Slave (LDU XX.X) responds
Meaning
DS
S+00002
Request: Step size 2
CE
E+00017
(example)
Request: TAC counter CE17
CE 17
OK
Calibration sequence active
DS 50
OK
Setup: Step size 50
Notes:
Legal for trade applications allow for up to 10 000 intervals. The allowed step size has to be considered.
In multi-range applications the command DS defines the step size of the lowest measuring range
(command CM 1). The next measuring range (command CM 2 respective CM 3) automatically uses the
corresponding next step size. (e.g. range 1 uses step size 20 range 2 uses step size 50 range 3
uses step size 100). The same applies for multi-interval applications.
8.2.6. DP
Set Decimal Point Position
This command allows the decimal point to be positioned anywhere between leftmost and rightmost digits of the
5-digit output result. Position 0 means no decimal point.
Master (PC / SPS) sends
Slave (LDU XX.X) responds
Meaning
DP
P+00002
Request: Position of decimal point 2
CE
E+00017
(example)
Request: TAC counter CE17
CE 17
OK
Calibration sequence active
DP 0
OK
Setup: no decimal point
Factory default: DP = 3
8.2.7. CZ
Set Calibration Zero Point
This is the reference point for all weight calculations, and is subject to TAC control.
Master (PC / SPS) sends
Slave (LDU XX.X) responds
Meaning
CE
E+00017
(example)
Request: TAC counter CE17
CE 17
OK
Calibration sequence active
CZ 0
OK
Zero point saved
Factory default: approx. 0 mV/V input signal