Dynon Avionics EFIS-D10A Installation Guide User Manual
Page 66
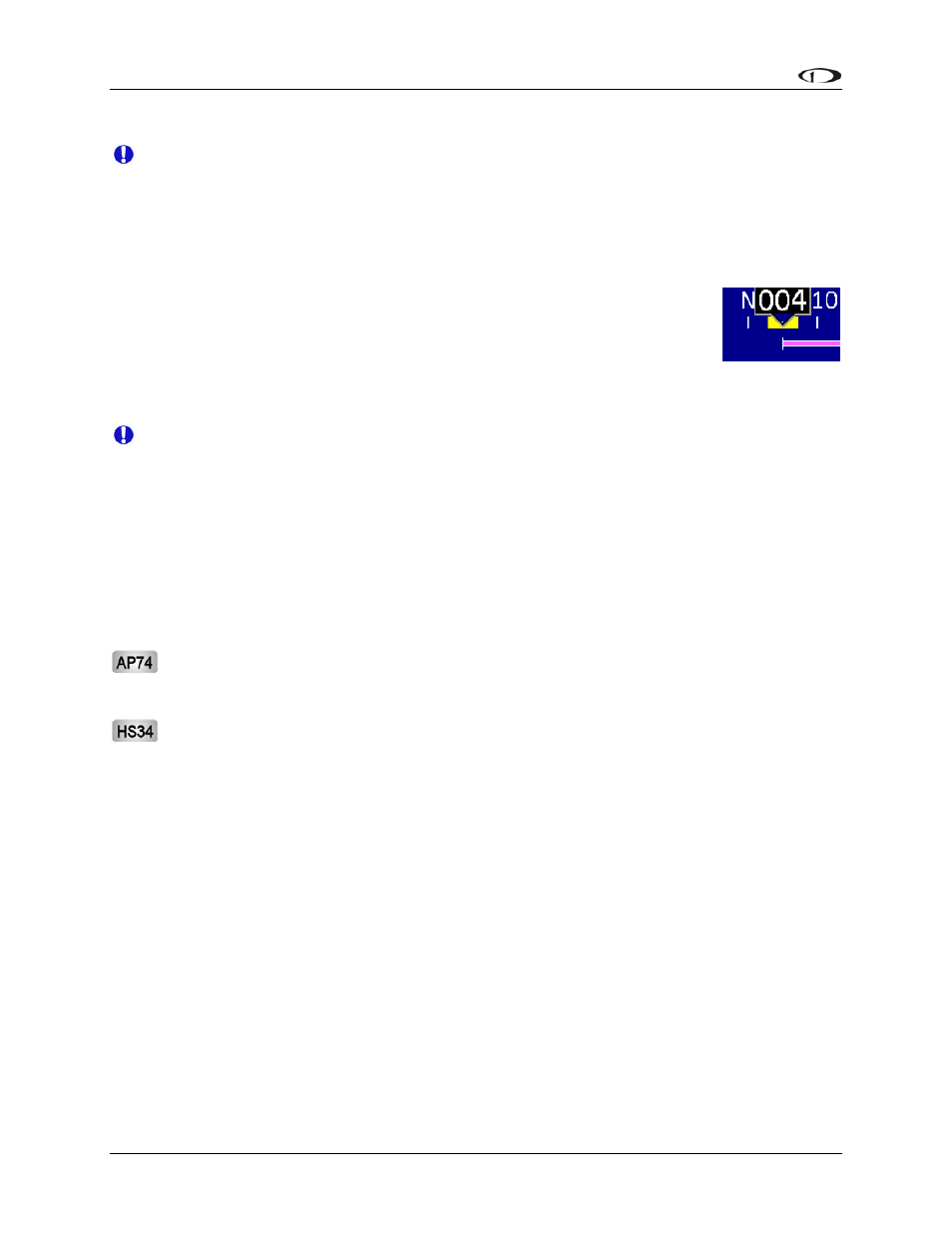
Autopilot Installation and Configuration
If necessary, adjust the TORQUE value in the EFIS > SETUP > AP > ROLL SERVO menu.
If you have adjusted the roll servo TORQUE value to 100% and are still seeing frequent
slips, you may need to move the linkage attachment point on the roll servo 1 hole closer
to the shaft. When doing this, take all precautions to ensure that an over center condition
cannot occur, while still preserving the control surfaces’ full range of motion. If a
mechanical solution is not possible, you may wish to try a higher strength servo (e.g., if
genta to signify GPS
you have an SV32 installed, try swapping for an SV42).
After verifying that the TORQUE value is set appropriately, watch closely for
AP “wandering” around the target heading or track. The AP should keep the
inverted triangle of the heading bug closely aligned with the triangle of the
numerical magnetic heading indicator (as shown at right). If flying in TRK
mode, the AP should keep the inverted triangle of the bug (colored ma
mode) aligned with the magenta triangle of the current ground track.
.
90 degrees to the left or right of current heading via any of these
met d
If excessive wandering is observed, increase the SENSITIVY parameter in the EFIS >
SETUP > AP > ROLL SERVO menu. If the AP control seems “twitchy” or aggressive,
decrease the SENSITIVITY value. All adjustments of SENSITIVITY should be done in
increments of 1 or 2, allowing you to notice subtle changes in control
Step 8f – Change the heading bug 90 degrees from the current heading
Change the HDG bug to
ho s:
On the EFIS, enter the EFIS > AP > BUGS > HDG menu, and press INC + or DEC - to
set desired heading.
, if you have configured
t) until the HDG bug adjustment window is
On the AP74, press the VALUE knob (or just begin rotating knob
the VALUE KNOB settings to allow for tha
displayed. Rotate the knob until the desired target heading is set.
On the HS34, rotate the HEADING knob.
As soon as the heading bug is changed, the AP begins changing the aircraft’s direction to follow.
P status indicator as you did in step 8e; if
s
an
ITY needs to be increased. If, upon reaching the target
Step 8g – Verify roll TORQUE and SENSITIVITY settings during turn(s)
During an AP-commanded turn, observe the A
excessive slipping is observed (indicated by a yellow highlight around the HDG status), then
increase the roll servo’s TORQUE parameter.
Repeat the 90 degree AP-commanded turns and torque adjustments until the HDG indicator doe
not display a slip indication.
Continue performing AP-commanded turns, and observe the overall behavior of the aircraft. If
the aircraft wallows, or rolls out of turns slowly as it reaches the target heading, that is
indication that the Roll Servo SENSITIV
heading and the stick “twitches” excessively, that is an indication that the Roll Servo
SENSITIVITY needs to be decreased.
6-26
EFIS-D10A
Installation
Guide