0 load train visual inspection suggestions, 1 visual inspection of shackles, Visual inspection of shackles – Rice Lake MSI-9300HT Hi-Torque Port-A-Weigh Plus CellScale RF Safety User Manual
Page 13
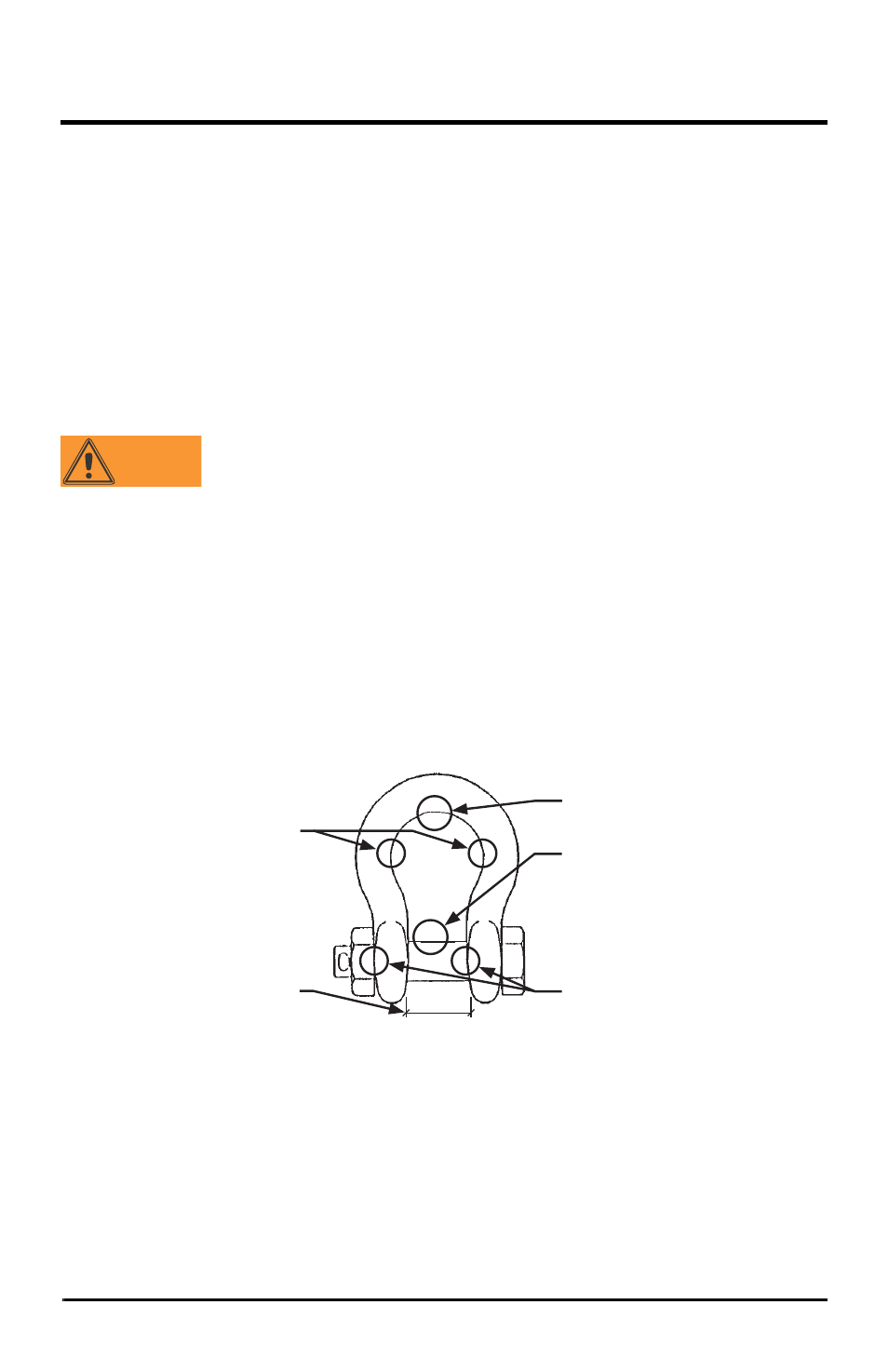
Load Train Visual Inspection Suggestions 9
4.0
Load Train Visual Inspection Suggestions
• Always visually inspect scale load bearing components before using.
• Check for distortion such as bends, twists and spread.
• Inspect for wear such as peening, nicks, gouges, cracks, corrosion and thread
damage.
• Magnetic Particle or Dye Penetrant crack detection of all components of the load
train assembly should be conducted annually. If the crane scale hook, shackle or
lifting eye are painted, visual inspection should take this coating into
consideration. Surface variations can disclose evidence of heavy or severe use
that requires more detailed analysis. The surface condition may, in such
instances, call for stripping the paint.
• Annual inspection of the load sensor by an Authorized
MSI
Distributor is
strongly recommended.
WARNING
CHECK FOR WEAR
CHECK FOR WEAR
AND STRAIGHTNESS
CHECK TO INSURE
THE PIN IS SEATED
CHECK SHACKLE
FOR OPENING
CHECK FOR WEAR
• Do not use any load bearing component that is worn beyond 5% of original
dimension.
• Remove from service any load bearing component with a detected crack.
4.1
Visual Inspection of Shackles
• Check for distortion such as bends, twists and spread.
• Look for peening, nicks and gouges.
• Inspect for cracks or corrosion.
• Check for thread damage.
Figure 4-1. Shackle Field Inspection Areas
- MSI-9300 Port-A-Weigh Plus CellScale RF Safety MSI-8000HD Indicator/RF Remote Display Safety MSI-8000 RF Remote Display Safety MSI-7300 Dyna-Link 2 Safety MSI-6260CS Trans-Weigh CellScale RF Safety MSI-4300 Port-A-Weigh Plus Safety MSI-4260 Port-A-Weigh Safety MSI-3460 Challenger 3 Safety MSI Tension Dynamometers Safety MSI Indicators/Remote Displays Safety