Test check valve no. 1, Test check valve no. 2, Test for leaky no. 2 shutoff – Ames Fire & Waterworks LFC300, LFC300N Lead Free Double Check Detector Assemblies User Manual
Page 3: Material/tool requirements, Instructions
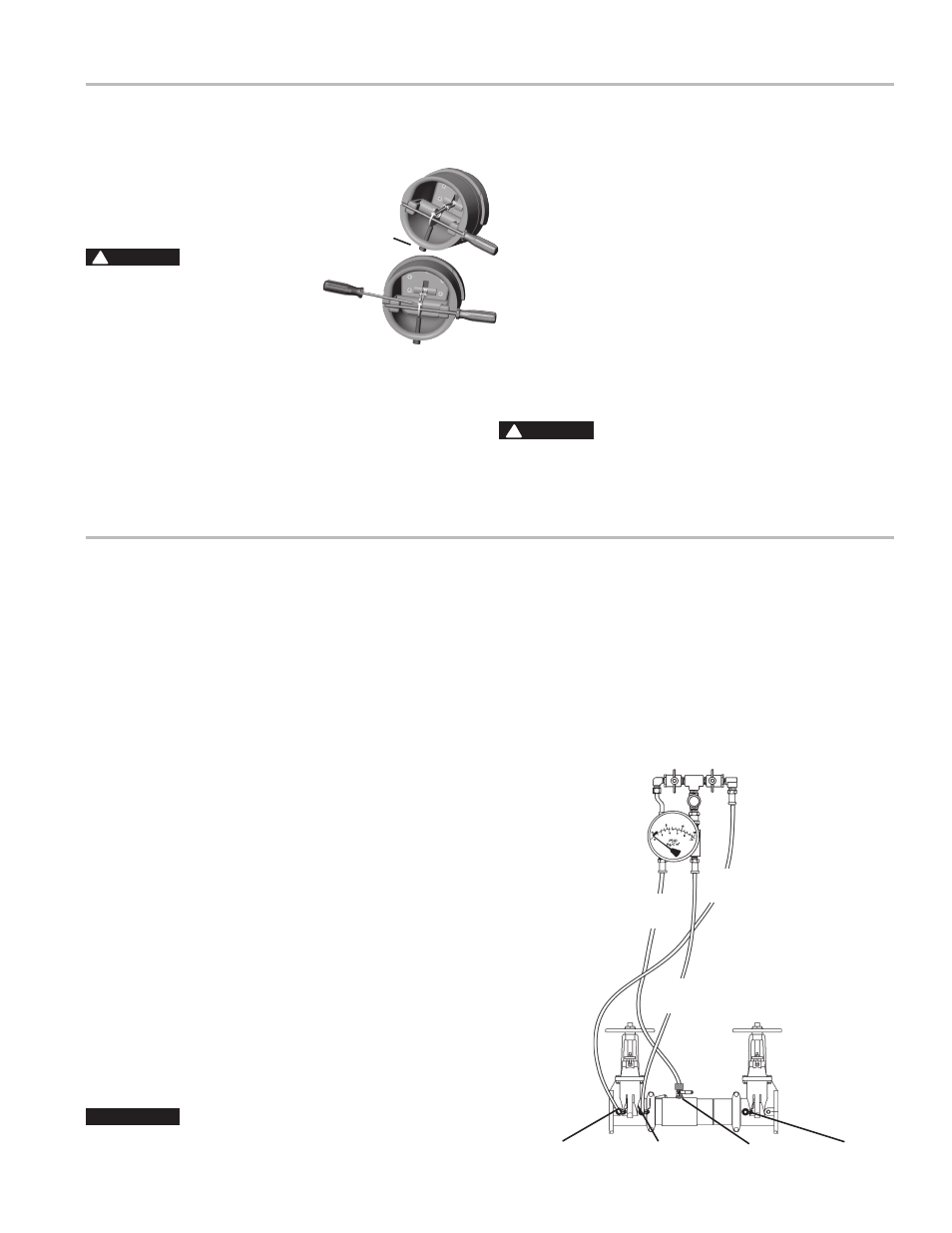
3
Ball Type Test Valves
A
C
B
Needle
Valve
High Hose
(Yellow)
Low Hose
(White or Red)
Vent Hose
(Blue)
Test Cock
Test Cock
Test Cock
Test Cock
No. 1
No. 2
No.3
No.4
Test Check Valve No. 1
Step 1: Ensure shutoff #1 is open, shutoff #2 is closed.
Step 2: Connect high side hose to test cock #3, low side to test
cock #2 and open both test cock #2 and test cock #3.
Step 3: Open valve C, then open A to bleed air from the high
side. Close valve A, then open B to bleed low side.
Close valve B.
Step 4: Connect vent hose loosely to test cock# 1. Open valve
A to vent air from vent hose, Tighten vent hose at test
cock #1, open test cock #1.
Step 5: Close shutoff #1. Slowly loosen hose at test cock #2
until differential gauge rises to 2psi and retighten hose.
If the differential reading does not decrease, record
check valves as “tight”.
Test Check Valve No. 2
Step 1: Move the high side hose to test cock #4, low side to test
cock #3 and open both test cock #3 and test cock #4.
Remove vent hose from test cock #1, open shutoff #1.
Step 2: Open valve C, then open valve A to bleed air from the
high side. Close valve A, then open valve B to bleed low
side. Close valve B.
Step 3: Connect vent hose loosely to test cock #1. Open valve A
to vent air from the vent hose. Tighten vent hose at test
cock #1, open test cock #1.
Step 4: Close shutoff #1, and then slowly loosen hose at test
cock #3 until differential gauge rises to 2psi and retight-
en hose. If the differential reading does not decrease,
record check as tight. Remove all hoses and restore
valve to original working condition.
NOTICE
The assembly will fail both the first and second check valve tests
above, if shutoff #2 leaks excessively. To test for a leaky #2 shutoff,
use the following procedure.
Test for Leaky No. 2 shutoff
Step 1: Connect the high side to test cock #1, low side to test
cock #4. Open test cock #1 and test cock #4. Close
shutoffs #1 and #2.
Step 2: Close valve C. Open valve A, then open valve B
1
/
2
turn,
loosen hose at test cock #4 to remove air. Retighten hose.
Step 3: If the differential gauge rises above 0, there is excessive
leakage at shutoff #2 and it must be replaced to test the
assembly.
Material/Tool Requirements:
• #4 Phillips screwdriver or
3
/
8
" diameter rod, length sufficient
to span diameter of check, see Figures A and B.
•
1
/
2
– 13" x 5" fully threaded hex bolt (Service bolt).
•
3
/
4
" open end or socket wrench.
Instructions:
WARNING
!
Prior to servicing any Ames valve, it is
mandatory to shut down the water sys-
tem by closing both the inlet and outlet shutoff
valves. After shutoff valves are closed, open test
cock #2, #3 & #4 to relieve pressure within the
backflow assembly.
1. After #3 test cock has been opened to relieve pressure, re-
move #3 test cock from housing. When repairing an
8" or 10" (200 or 250mm) device, remove both Victaulic
couplers from body. Slide the downstream Victaulic
coupler gasket to the downstream side of the housing.
The upstream Victaulic coupler gasket stays in place.
2. Remove checks to be maintenanced.
3. Locate the service hole and thread in the service bolt by
hand until it contacts the linkage. (Figure A)
4. Continue to thread in service bolt with the wrench until the
service hole in the linkage is aligned with the service notches
on the spring arbors. (Figure A)
5. Insert the Phillips screwdriver through the arbors and service hole
of the linkage making sure that the tip of the screwdriver extends
past the ends of the arbors by a minimum of
1
/
4
" (6mm). (Figure B)
6. Back out the service bolt until load is transferred to the screw-
driver. Continue to back out the service bolt until sufficient clear-
ance is achieved to remove the complete spring mechanism.
7. To disconnect linkage, remove retaining clip and pin (store in a
safe location for reinstallation).
8. To remove spring mechanism, grasp the screwdriver at the center
and pull complete assembly straight out and store in a safe place.
9. Reinstall in reverse.
WARNING
!
While the spring mechanism is removed for check servicing; never
pull the screwdriver out or off the support notches on the arbors.
Doing so may cause bodily injuries.
Maintenance Instructions 8" – 10" (200 – 250mm)
Testing — Double Check Valve Assemblies
Figure A
Figure B
Service Hole