Ames Fire & Waterworks Air Gaps For Reduced Pressure Zone Assemblies User Manual
Installation instructions air gap, Sizes: 2, Testing
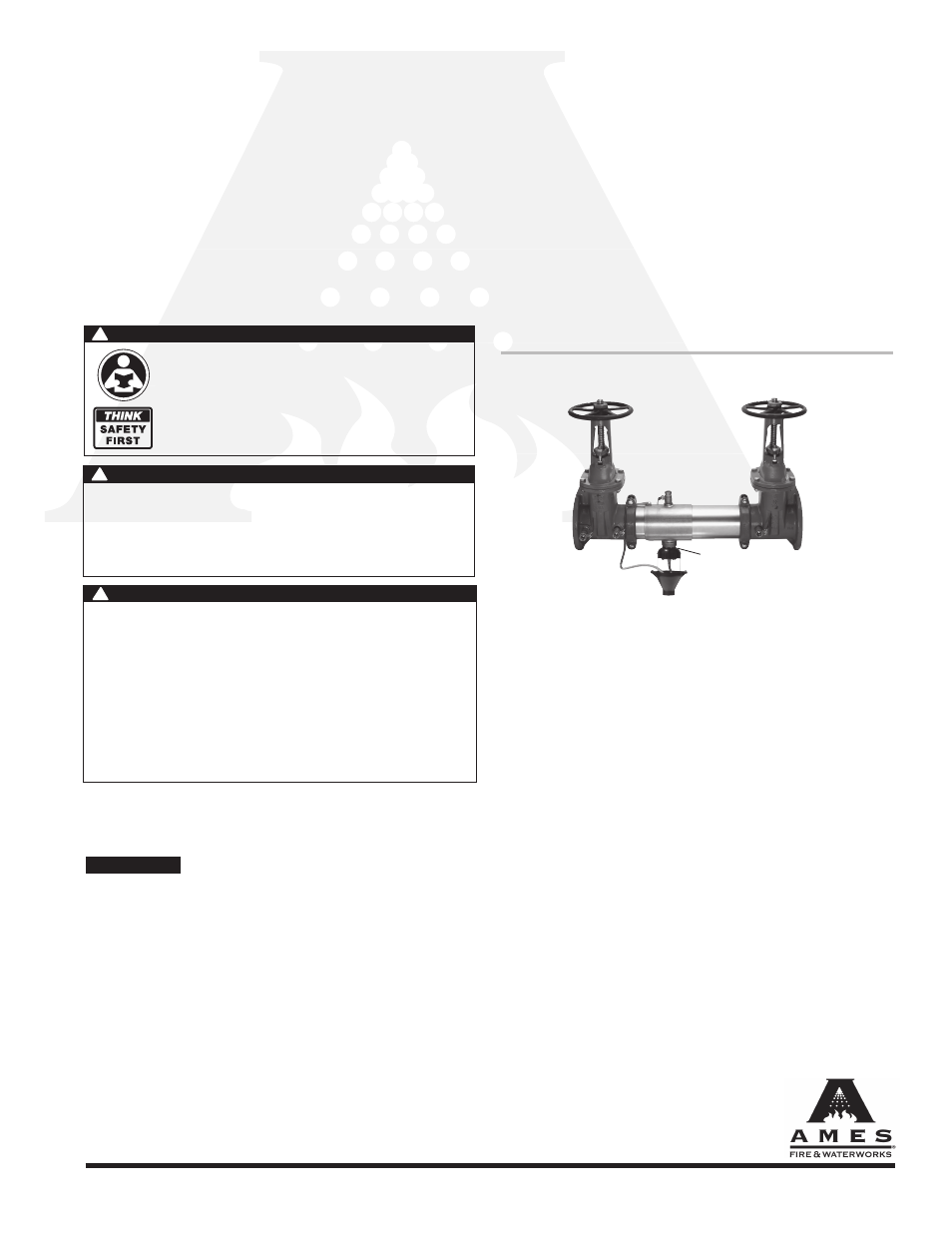
IS-A-AirGaps
Installation Instructions
Air Gap
1. Remove L shape bracket from one side of air gap drain.
2. Remove screw from one side of the splash guard.
3. Slide one half of the splash guard into the groove on the relief
valve body.
4. Slide the other half of the splash guard into the groove on the relief
valve body and reassemble the two parts together.
5. Reattach the L shape brackets long side up into slots in the
splash guard with screws.
6. Push as much of the sensing hose as possible into the air gap
drain funnel to prevent over spray.
Series 400 and 500 Air Gaps
Sizes: 2
1
⁄
2
" - 10" (65 – 250mm)
**
Ames Air Gap Drains are designed to collect water that is being
discharged by the relief valve, due to minor check valve fouling
and/or line pres sure fluc tu a tions.
NOTICE
Air Gap Drains are not designed to collect the full discharge
capacity of the relief valve.
Testing
For field testing procedure, refer to Ames installation sheets
IS-A-ATG-1 found on
www.amesfirewater.com.
For other repair kits and service parts, refer to our Backflow
Prevention Products Repair Kits & Service Parts price list
PL-A-RP-BPD found on
www.amesfirewater.com.
For technical assistance, contact your local Ames representative.
Splash
Guard
www.amesfirewater.com
A Division of Watts Water Technologies, Inc.
WARNING
!
Read this Manual BEFORE using this equipment.
Failure to read and follow all safety and use information can
result in death, serious personal injury, property damage, or
damage to the equipment.
Keep this Manual for future reference.
You are required to consult the local building and plumbing
codes prior to installation. If the information in this manual
is not consistent with local building or plumbing codes,
the local codes should be followed. Inquire with governing
authorities for additional local requirements.
WARNING
!
Need for Periodic Inspection/Maintenance: This product must
be tested periodically in compliance with local codes, but at least
once per year or more as service conditions warrant. If installed on
a fire suppression system, all mechanical checks, such as alarms
and backflow preventers, should be flow tested and inspected in
accordance with NFPA 13 and/or NFPA 25. All products must be
retested once maintenance has been performed. Corrosive water
conditions, and/or unauthorized adjustments or repair could render
the product ineffective for the service intended. Regular checking
and cleaning of the product’s internal components helps assure
maximum life and proper product function.
WARNING
!
** Metric Dimensions are nominal pipe diameter. This product is produced with
NPT threaded end connections.