Section 5: troubleshooting, Section 5: troubleshooting -1 – Tweco K4000 User Manual
Page 25
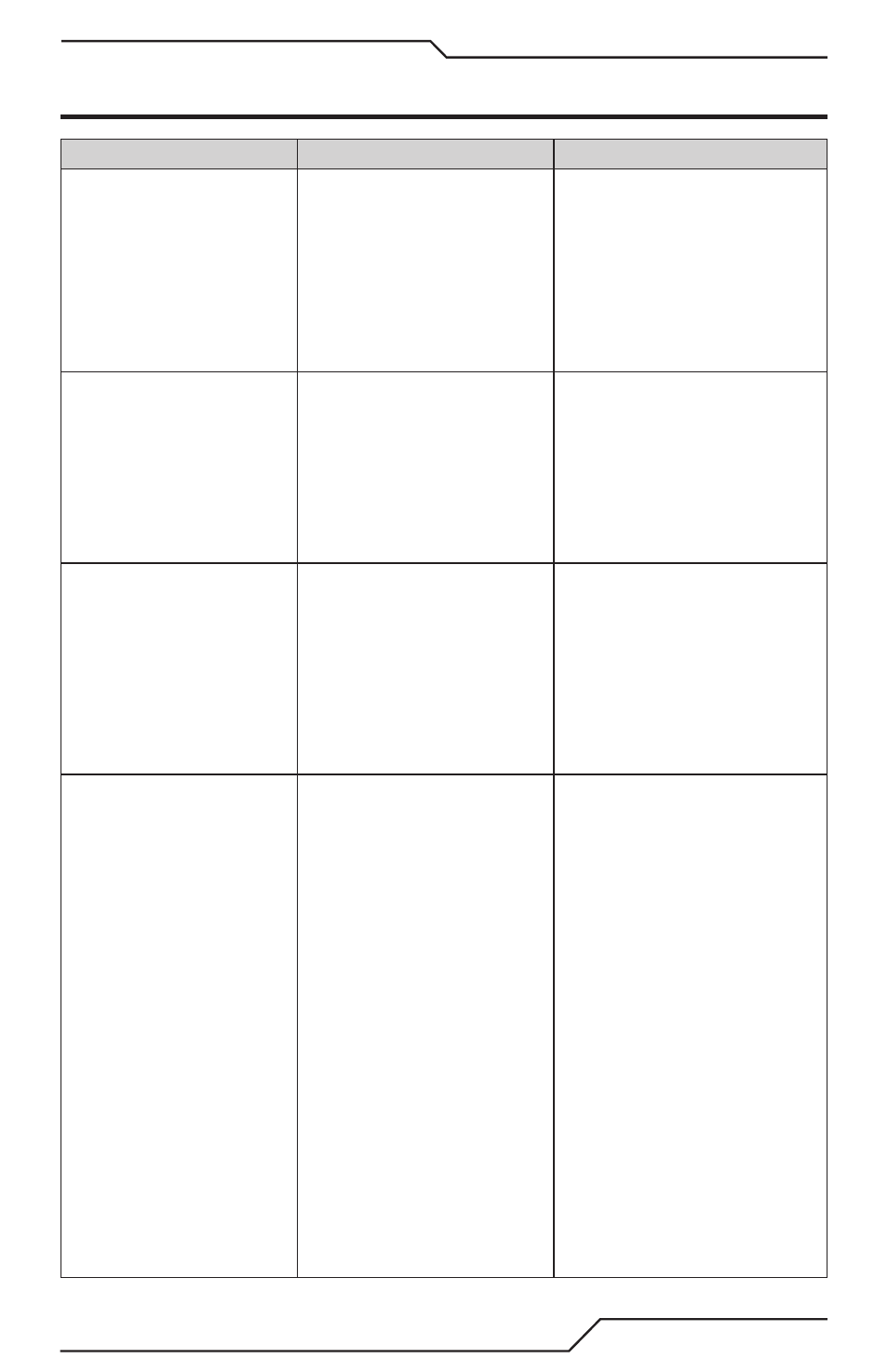
5-1
SECTION 5: TROUBLESHOOTING
Problem
Cause
Solution
Large free-carbon de-
posit at the beginning of
the groove.
1. The operator either ne-
glected to turn on the
air jet before striking
the arc or the torch was
located improperly.
1. Turn on air before strik-
ing the arc and air should
flow between the elec-
trode and the workpiece.
2. Carbon rod not posi-
tioned properly in head
assembly.
2. Ensure carbon rod is
seated in groove in torch
head.
An unsteady arc, causing
the operator to use a
slow travel speed even
on shallow grooves.
1. Not enough amperage
for the electrode diam-
eter used (see Table
2). While the lowest
recommended amper-
age may be enough, it
requires greater opera-
tor skill. A mid-range
amperage is better.
1. If the desired amper-
age cannot be obtained
from the available
power source, use the
next smaller diameter
electrode or parallel two
or more welding power
supplies.
Erratic groove with the
arc wandering from
side-to-side and with
the electrode heating up
rapidly.
1. The process used with
DCEN (electrode nega-
tive).
1. Gouging process should
be done with DCEP (Elec-
trode positive) whenever
possible. Direct current
electrodes should be
used with DCEP (elec-
trode positive) on all
metals, except for a few
copper alloys such as
Superston and Nialite.
Intermittent arc action
resulting in an irregular
groove surface.
1. The travel speed was
too slow in manual
gouging. The opera-
tor possibly set their
hand on other work for
balance, a tendency
in shielded metal-arc
welding. Since the
speed of air carbon-arc
gouging is much faster
than shielded metal-arc
welding, friction be-
tween the gloved hand
and the workpiece may
cause a jerky forward
motion thus causing
the gap between the
electrode and work-
piece to become too
large to maintain the
arc.
1. The operator should
stand comfortably so
their arms move freely
and their gloves do not
drag on the workpiece. If
using mechanized equip-
ment, check
Table 4 (Page 4-24) for
proper operating condi-
tions.
2. Poor ground connec-
tion.
2. Inspect ground clamps
and lead(s) to ensure
connection proper.