2 cut quality, 3 recommended cutting speeds, 2 cut quality 5.3 recommended cutting speeds – Tweco Drag-Gun User Manual
Page 20: 3 recommended cutting
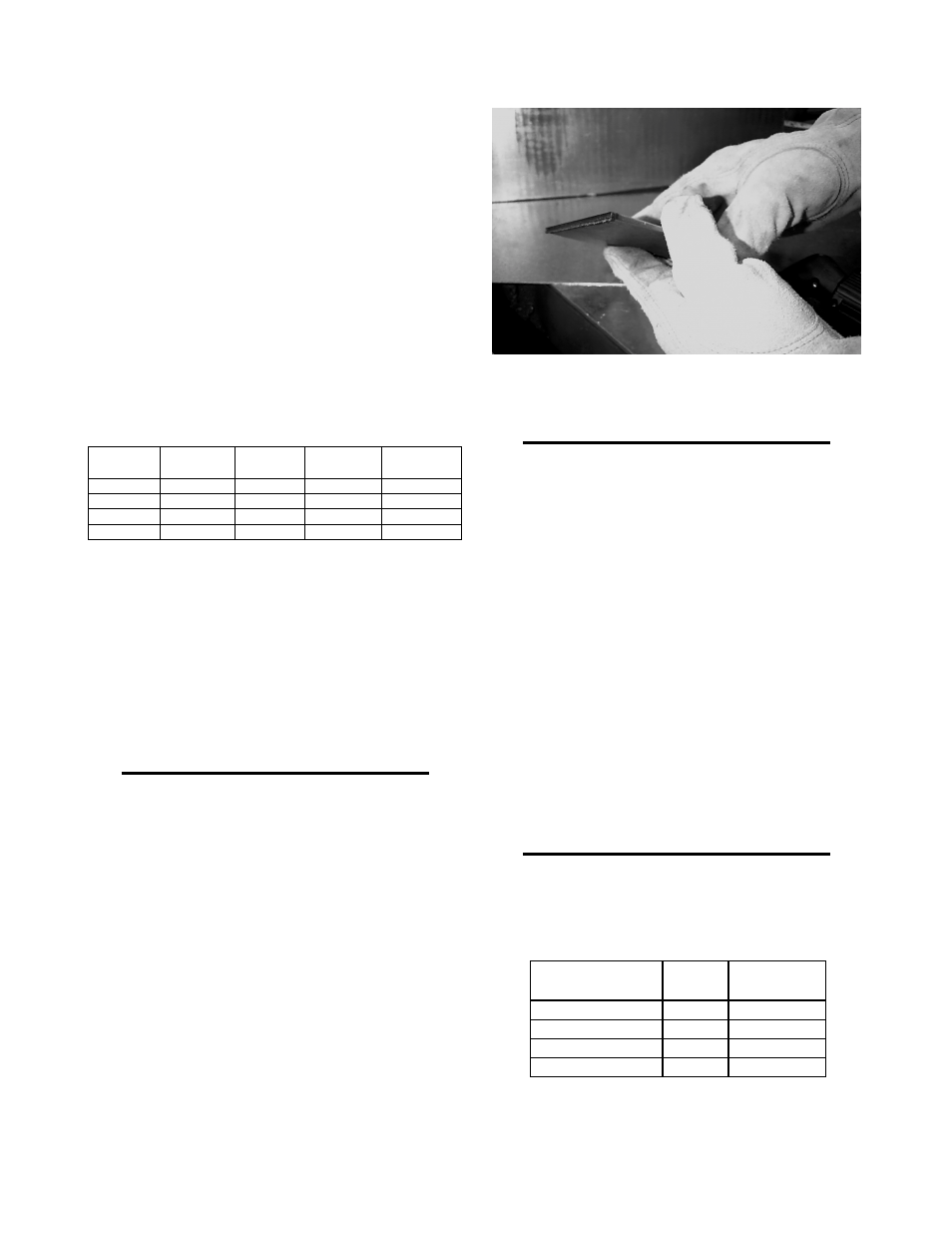
DRAG-GUN Plasma Cutter
16
Operating Manual 0-2682
3. Start the pierce off the cutting line on the scrap piece
or template and then continue the cut onto the cut-
ting line. Hold the torch perpendicular to the
workpiece after the pierce is complete.
4. Clean spatter and scale from the shield cup and the tip
as soon as possible.
5.2 Cut Quality
5.2 Cut Quality
5.2 Cut Quality
5.2 Cut Quality
5.2 Cut Quality
Cut quality depends heavily on setup and parameters
such as torch alignment with the workpiece, cutting
speed, condition of torch parts, input line voltage, and
operator ability. Cut quality will also vary on different
types of material and thicknesses.
The following table shows the cut quality one can expect
from this equipment for materials with a thickness of
7 gauge or less:
Material
Thickness
Mild Steel
Stainless
Steel
Aluminum
Galvanized
Steel
20 Gauge
Excellent
Excellent
Very Good
Excellent
16 Gauge
Very Good
Excellent
Good
Excellent
10 Gauge
Very Good
Good
NR
Good
7 Gauge
Severance
Severance
NR
Severance
Figure 5-5 Cut Characteristics
Excellent
- No bevel or dross*
Very Good
- Negligible bevel; slight dross* (easy to remove)
Good
- Slight bevel with some dross* (easy to remove)
Severance
- Substantial reduction in cut quality and speed
NR
- Not Recommended
NOTES
Pierce Capacity is 1/16" (1.59 mm)
* Dross is molten material which is not blown out
of the cut area and resolidifies on the plate. Top
spatter is dross which accumulates on the top sur-
face of the workpiece. Top spatter is normally
caused by a slow torch travel speed or too high of a
torch standoff distance. Dross normally breaks off
quite easily by simply scraping it off with a piece
of metal.
Figure 5-6 Cut Sample
NOTE
A worn tip can also affect the quality of a cut.
Consider replacing the tip if any of the following
indicators are present:
• reduced speed
• voltage drop
• crooked cut
5.3 Recommended Cutting
5.3 Recommended Cutting
5.3 Recommended Cutting
5.3 Recommended Cutting
5.3 Recommended Cutting
Speeds
Speeds
Speeds
Speeds
Speeds
Cutting speed depends on material type, material thick-
ness, and the operator’s ability to accurately follow the
desired cut line. The following factors may have an im-
pact on system performance:
• Torch parts wear
• Line voltage fluctuations
• Torch standoff height
NOTE
This information represents realistic expectations
using recommended practices and well-maintained
systems. Actual speeds may vary up to 50% from
those shown.
Material
Gauge
Inches per
Minute
Stainless Steel
20
60
Galvanized Steel
18
60
Aluminum
16
20
Carbon Steel
10
9
Figure 5-7 Cutting Speed Chart