Motor troubleshooting guide cont, Ro system troubleshooting – Watts PWR4011 User Manual
Page 7
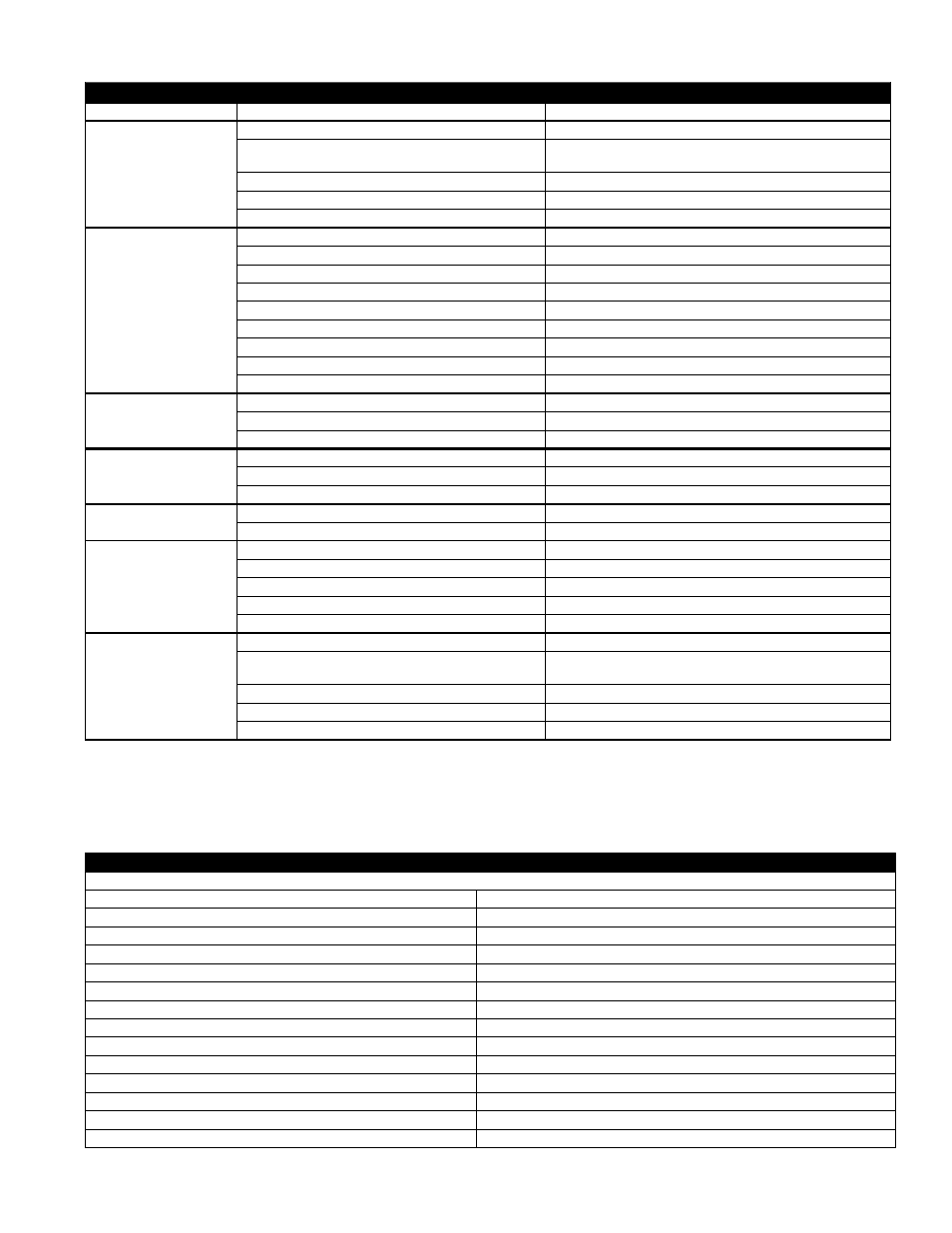
7
Motor Troubleshooting Guide cont.
PRoblem
Possible cause
coRRective action
Wrong rotation
Wrong sequence of phases
Reverse connections at motor or at switchboard.
Motor overheats while running
under load
Overloaded
Reduce load.
Frame or bracket vents may be clogged with dirt and prevent proper
ventilation of motor.
Open vent holes and check for a continuous stream of air from the motor.
Motor may have one phase open
Check to make sure that all leads are well connected.
Grounded could
Locate and repair.
Unbalanced terminal voltage
Check for faulty leads, connections and transformers.
Motor vibrates after correcting
have been made
motor misaligned
Realign
Weak support
Strengthen base.
Coupling out of balance
Balance coupling.
Driven equipment unbalanced
Rebalance driven equipment.
Defective ball bearing
Replace bearing.
Bearing not in line
Line properly.
Balancing weights shifted
Rebalance motor.
Polyphase motor running single phase
Check for open circuit.
Excessive end play
Adjust bearing or add washer.
Unbalanced line current on
polyphase motors during normal
operation
Unequal terminal volts
Check leads and connections
Single phase operation
Check for open contacts
Scraping noise
Fan rubbing air shield
Remove interference.
Fan striking insulation
Clear fan.
loose on bedplate
Tighten holding bolts.
Noisy operation
Airgap not uniform
Check and correct bracket fits or bearing.
Rotor unbalance
Rebalance.
Hot bearings general
Bent or sprung shaft
Straighten or replace shaft.
Excessive belt pull
Decrease belt tension.
Pulleys too far away
Move pulley closer to motor bearing.
Pulley diameter too small
Use larger pulleys.
Misalignment
Correct by realignment of drive.
Hot bearings ball
Insufficient grease
Maintain proper quantity of grease in bearing.
Deterioration of grease, or lubricant contaminated
Remove old grease, wash bearings thoroughly in kerosene and replace with new
grease.
Excess lubricant
Reduce quantity of grease: bearing should not be more than ½ filled.
Overloaded bearing
Check alignment, side and end thrust.
Broken ball or rough races
Replace bearing: first clean housing thoroughly.
These instructions do not cover all details or variations in equipment nor provide for every possible condition to be met in connection with installation, operation or maintenance. Chart courtesy of
Marathon Electric.
RO System Troubleshooting
PRoblem
coRRective action
General
high Product Water tDs
Membrane expanded.
Replace membrane.
Membrane attack by chlorine
Carbon pre-filter may be exhausted. Replace with a new cartridge.
Clogged pre-filter-creates pressure drop and low reject flow.
Replace pre-filter cartridge.
Feed pressure too low.
Feed pressure must be at least 20 psi.
Insufficiently flushed post-filter cartridge.
Flush post-filter with pure water.
Brine seal on membrane leaks.
Determine if seal or o-ring is bad. Replace as needed.
no Product Water or not enough Product Water
Feed water shut off.
Turn on feed water.
Low feed pressure. Feed pressure must be at least 20 psi.
Consider booster pump.
Pre-filter cartridge clogged.
Replace pre-filter cartridge.
Membrane fouled.
Determine and correct cause; replace membrane.
Product check valve stuck.
Replace check valve fitting.
Low pump discharge pressure
Open pump discharge valve, replace pump