G. troubleshooting ro troubleshooting guide, Motor troubleshooting guide – Watts PWR4011 User Manual
Page 6
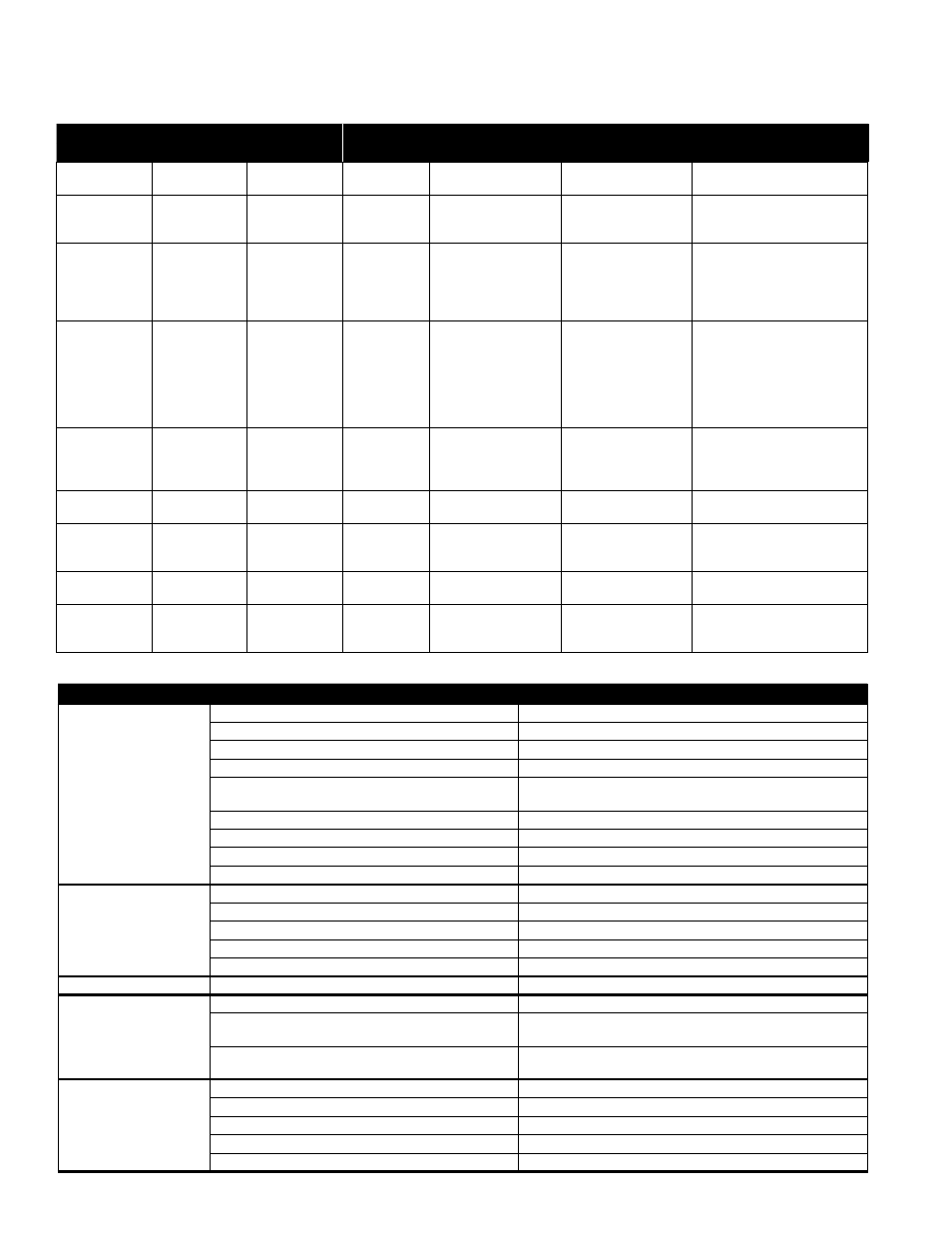
6
G. Troubleshooting
RO Troubleshooting Guide
sYmPtoms
salt PassaGe
PeRmeate FloW
PRessuRe DRoP
location
Possible causes
veRiFication
coRRective action
Normal to increased Decreased
Normal to increased Predominantly
first stage
Metal oxide
Analysis of metal ions in
cleaning solution.
Improved pretreatment to remove met-
als. Cleaning with acid cleaners.
Normal to increased Decreased
Normal to increased Predominantly
first stage
Colloidal fouling
SDI measurement of feed/
X-ray diffraction analysis of
cleaning sol. residue.
Optimize pretreatment system for
colloid removal. Clean with high pH,
anionic detergent formulation.
Increased
Decreased
Increased
Predominantly
last stage
Scaling (CaSO
4
, CaSO
3
,
BaSO
4
, SiO
2
)
Analysis of metal ions in
cleaning sol. Check LSI of
reject. Calculate maximum
solubility for CaSO
4
, BaSO
4
,
SiO
2
in reject analysis.
Increase acid addition and scale
inhibitor for CaSO
3
and CaSO
4
. Reduce
recovery. Clean with an acid formula-
tion for CaCO
3
, CaSO
4
and BaSO
4
.
Normal to moderate
increase
Decreased
Normal to moderate
increase
Can occur in any
stage
Biological fouling
Bacteria count in permeate
and reject. Slime in pipes
and vessels.
Shock dosage of sodium bisulfite.
Continuous feed of low conc. Of
bisulfite at reduced pH. Formaldehyde
sterilization. Clean with alkaline anionic
surfactant. Chlorine dosage up-stream
with subs. Dechlorination. Replace
cartridge filters.
Decreased or
moderately
increased
Decreased
Normal
All stages
Organic fouling
Destructive testing, e.g. IR
reflection analysis.
Optimization of pretreatment system
(e.g. coagulation process.) Resin/
activated carbon treatment. Clean with
high pH detergent.
Increased
Increased
Decreased
Most severe in
the first stage
Chlorine oxidant attack
Chlorine analysis of feed.
Destructive element test.
Check chlorine feed equipment and
dechlorination equipment.
Increased
Increased
Decreased
Most severe in
the first stage
Abrasion of membrane by
crystalline material
Microscopic solids analysis
of feed. Destructive ele-
ment test.
Improved pretreatment. Check all filters
for media leakage.
Increased
Normal to increased Decreased
At random
O-ring leaks, End or side
seal glue leaks.
Probe test. Vacuum test.
Colloidal material passage.
Replace O-rings. Repair or replace
elements.
Increased
Normal to low
Decreased
All stages
Conversion too high.
Check flows and pressures
against design guidelines
Reduce conversion rate. Calibrate
sensors. Increase analysis and data
collection.
Motor Troubleshooting Guide
PRoblem
Possible cause
coRRective action
Motor fails to start
Blown fuses
Replace fuses with proper type and rating
Overload trips
Check and rest overload in starter.
Improper power supply
Check to see that power supplied agrees with motor nameplate and load factor.
Open circuit in winding or control switch
Indicated by humming sound when switch is closed.
Mechanical failure
Check to see if motor and drive turn freely. Check bearing and
lubrication.
Short circuited stator
Indicated by blown fuses. Motor must be rewound.
Poor stator coil connection
Remove end bells, locate with test lamp.
Rotor defective
Look for broken bars or end ring.
Motor may be overloaded
Reduce load.
Motor Stalls
One phase connection
Check lines for open phase.
Wrong application
Change type or size. Consult manufacturer.
Overload motor
Reduce load.
Low motor voltage
See that nameplate voltage is maintained. Check connection.
Open circuit
Fuses blown, check overload relay, stator and push buttons.
Motor runs and then dies down
Power failure
Check for loose connections to line, to fuses and to control.
Motor does not come up
to speed
Not applied properly
Consult supplier for proper type.
Voltage too low at motor terminals because of line drop.
Use higher voltage on transformer terminals or reduce load. Check connections.
Check conductors for proper size.
Broken rotor bars or loose rotor.
Look for cracks near the rings. A new rotor may be required as repairs are usu-
ally temporary.
Motor takes too long to acceler-
ate
Open primary circuit
Locate fault with testing device and repair.
Excess loading
Reduce load.
Poor circuit
Check for high resistance.
Defective squirrel cage rotor
Replace with new rotor.
Applied voltage too low
Get power company to increase power tap.