Abs and atc wiring, Troubleshooting – Bendix Commercial Vehicle Systems EC-30 ABS/ATC CONTROLLER 2/08 User Manual
Page 19
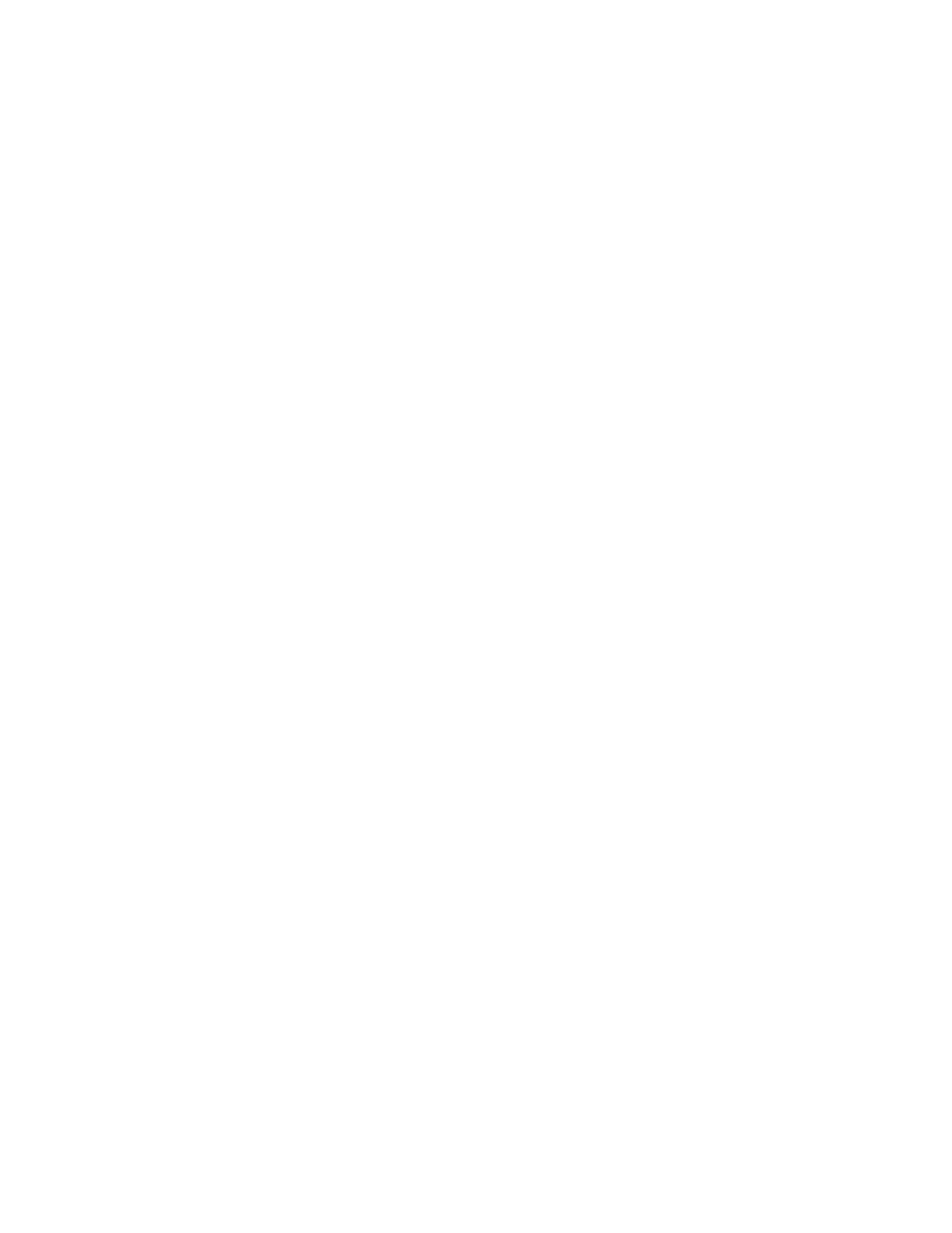
19
1. Position and secure the EC-30
™
controller in the original
mounting orientation using the four hex head bolts.
Torque the hex head EC-30
™
controller mounting
bolts to 98 in. Ibs. Over-tightening the ECU bolts
can cause damage to the EC-30
™
controller.
2. For a valve-mounted EC-30
™
controller, position and
secure the EC-30
™
controller assembly to the vehicle,
in the original mounting orientation. Reconnect all air
lines to the EC-30
™
controller assembly. All air lines and
fi ttings should be checked for leaks prior to returning
the vehicle to service.
3. Reconnect the electrical connectors to the EC-30
™
controller and torque the connector retaining jack-
screws to 15-20 in. lbs. Over-tightening the ECU
connector jack-screw(s) can cause damage to the
EC-30
™
controller.
4. Apply power and monitor the EC-30
™
controller power-
up sequence to verify proper system operation.
5. When necessary, it is possible to road test the ABS
function by making an abrupt stop from a vehicle speed
of about 20 mph to check for proper function. The
wheels should not enter a prolonged lock condition and
ABS function should be audible. It is the responsibility of
the technician to perform the tests in a safe location.
6. When necessary, it is possible to road test the ATC
function by accelerating on a road surface with
reduced traction. The drive wheels should not sustain
substantial spin. Audible bursts of air or engine throttle-
down should be noticed. It is the responsibility of the
technician to perform the tests in a safe location.
ABS AND ATC WIRING
The vehicle manufacturer designs and supplies the
vehicle harnesses for the EC-30
™
controller. However,
Bendix specifi es all component connectors. See chart 8
for components. The wiring harness and connectors are
weather resistant and sealed at the connector interface.
The wire gauge and insulation type used in the wire
harnesses is specifi c to the circuit function, but 16 gauge
GXL is most common. Refer to BW-106-A, Bendix ABS
Application Guideline, for specifi c wire harness application
information.
When troubleshooting ABS wiring, some general rules
should be followed where applicable.
1. Check all wiring and connectors to ensure they
are secure and free from visible damage. Check
for evidence of wire chafi ng due to poor routing or
poor securing of wires. Check connectors for proper
insertion and locking. Verify that the connector leads
are properly greased with a nonconductive electrical
grease compound and do not show signs of corrosion
or exposure to the environment.
2. During wiring repair, a splice must be properly soldered
and made waterproof.
3. Do not pierce wire insulation when checking for
continuity.
4. Do not deform individual pins or sockets during probing
with a volt/ohm meter.
5. Only use the correct crimping tool when replacing wire
terminals and connectors.
6. Properly resecure all wiring harness and sensor leads
when repairs are made.
TROUBLESHOOTING
Fault information can be retrieved from the EC-30
™
controller by using the diagnostic LED display, blink code
diagnostics or a diagnostic tool. However, the technician
must confi rm whether the fault resides in the component,
wiring or connectors. The following troubleshooting fl ow
charts will assist the technician in isolating the cause of
the fault.
Troubleshooting should always begin by observing the
ABS warning lamp and the ATC active/warning lamp
during the EC-30
™
controller power-up sequence.
If it is necessary to make electrical measurements, always
begin by taking voltage and resistance measurements at
the 30-pin and 18-pin wire harness connectors.
Once the circuit fault is found, isolate the area needing
repair by repeating the measurements at all connections
in the affected circuit (modulator, wheel speed sensor,
etc.).
No voltage or resistance measurements are to be made on
the bulkhead connector pins of the EC-30
™
controller.
When repairs are made, reconnect the electrical connectors
to the EC-30
™
controller and torque the connector
retaining jack-screws to 15-20 in. lbs. Over-tightening
the ECU connector jack-screw(s) can cause damage
to the EC-30
™
controller.
Troubleshooting Flowcharts
Section A - Power-up sequence - ABS warning lamp and
ATC active/warning lamp
Section B - Power-up sequence - Trailer ABS warning lamp
Section C - ABS warning lamp
Section D - ATC active/warning lamp
Section E - Trailer ABS warning lamp
Section F - Diagnostic LED quick reference
Section G - Power to the EC-30
™
controller
Section H - Wheel speed sensors
Section I - ABS modulators
Section J - ATC modulator
Section K - Serial communication