Grounding requirements – Rockwell Automation 1440-TB-E XM-944 Process/Temperature Terminal Base User Manual
Page 9
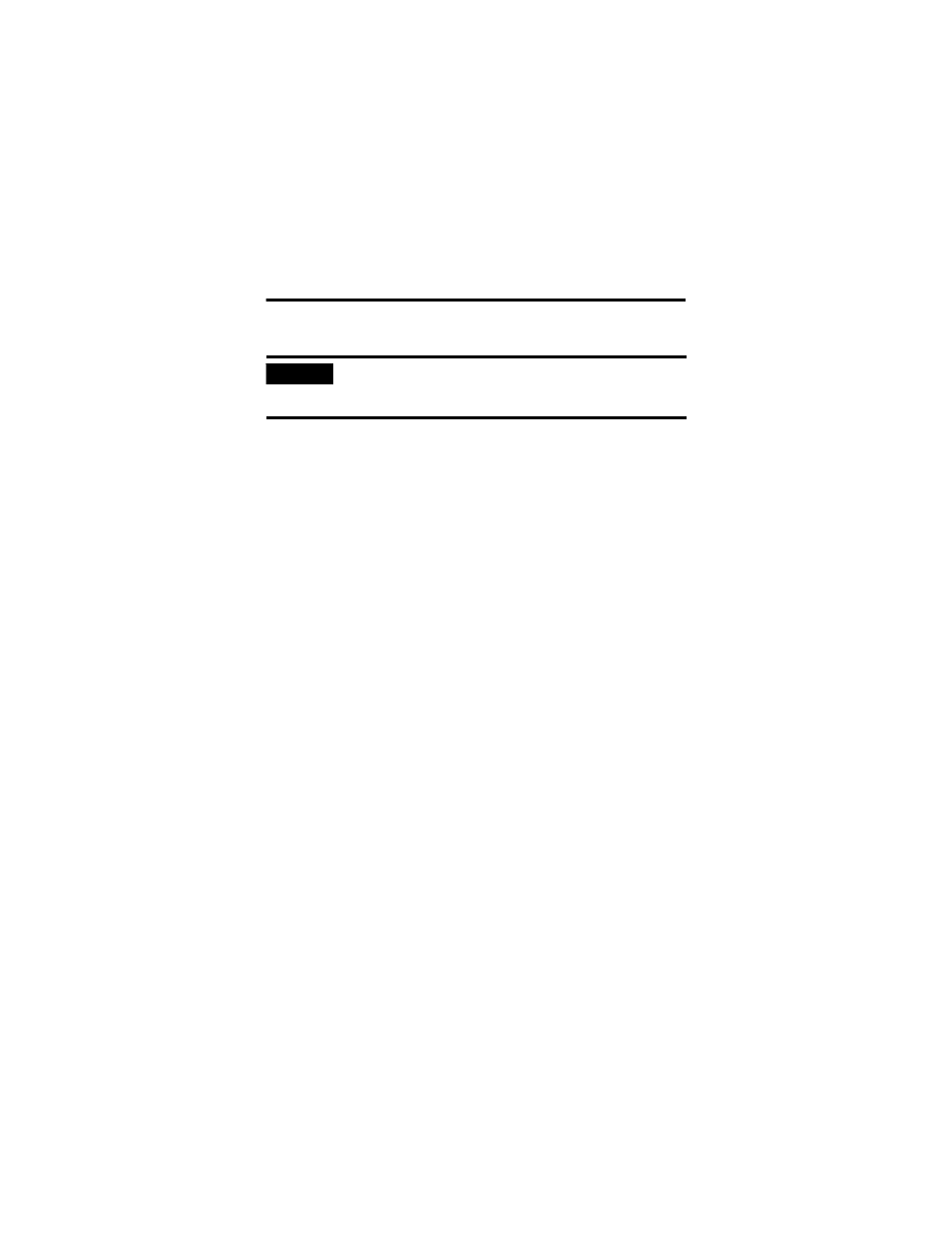
XM-944 Process/Temperature Terminal Base 9
Publication
GMSI10-IN024A-EN-P - May 2010
wires are much different, an error may exist. The closer the resistance values
are to each other, the greater the amount of error is eliminated.
To ensure that the lead values match as closely as possible:
• Keep lead resistance as small as possible and less than 50 ohms.
• Use quality cable that has a small tolerance impedance rating.
• Use a heavy-gauge lead wire which has less resistance per foot.
Grounding Requirements
Use these grounding requirements to ensure safe electrical operating
circumstances, and to help avoid potential emi and ground noise that can
cause unfavorable operating conditions for your XM system.
DIN Rail Grounding
The XM modules make a chassis ground connection through the DIN rail.
The DIN rail must be connected to a ground bus or grounding electrode
conductor using 8 AWG or 1 inch copper braid. See illustration on the
following page.
Use zinc-plated, yellow-chromated steel DIN rail (Allen-Bradley part no.
199-DR1 or 199-DR4) or equivalent to assure proper grounding. Using other
DIN rail materials (e.g. aluminum, plastic, etc.), which can corrode, oxidize, or
are poor conductors can result in improper or intermittent platform
grounding.
IMPORTANT
To ensure temperature or resistance value accuracy, the
resistance difference of the cable lead wires must be equal to
or less than 0.01 ohm.