Thermal Transfer Systems TEMA Designations of Heat Exchangers User Manual
Page 2
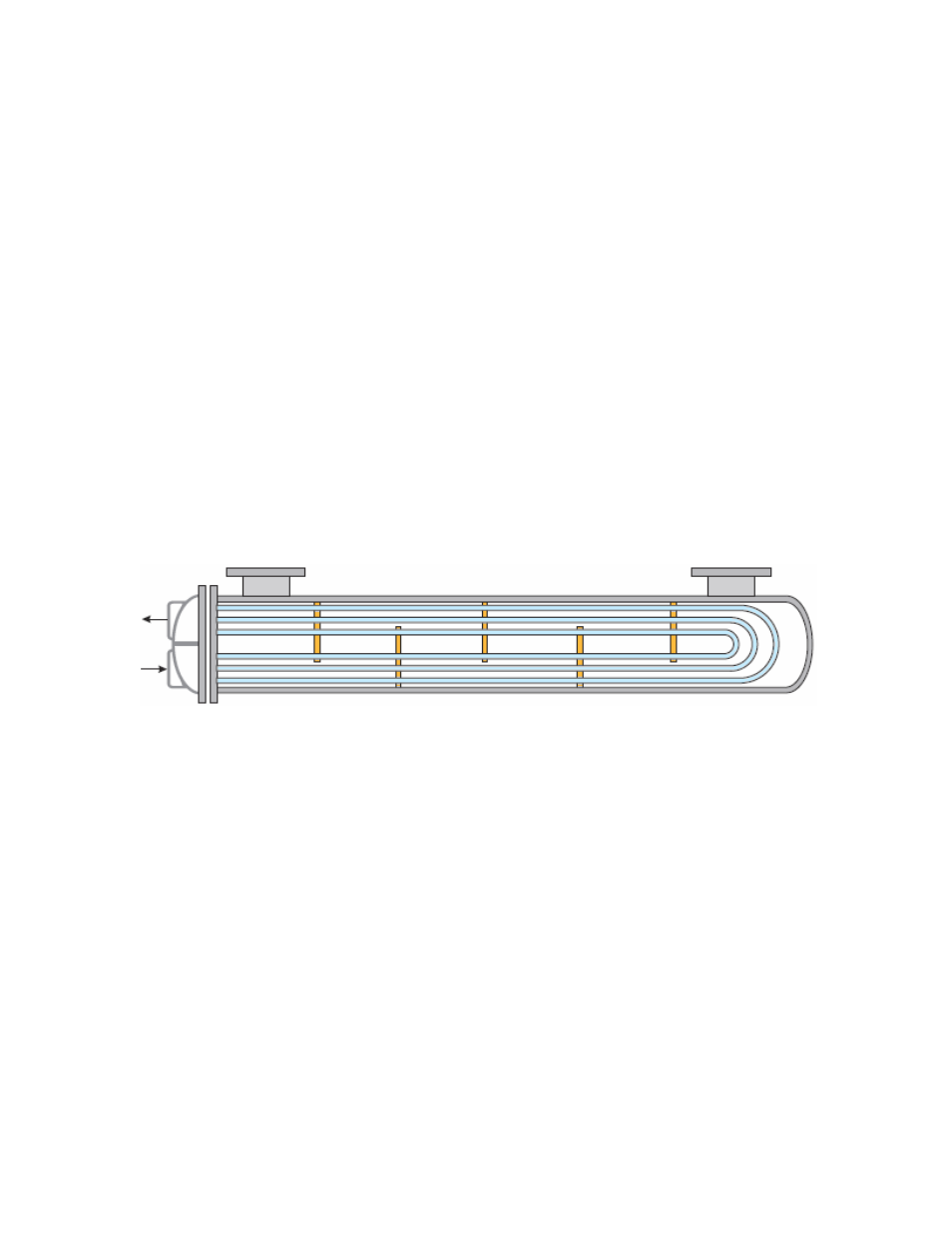
NEN- Tubesheets are welded to both the Shell & Bonnets. Access to the tubes is through
covers on the channels. These units are favored in very high pressure designs as their
construction minimizes the tubesheet thickness and number of high pressure retaining flanges.
AEM/BEM/AEL-Shell side is completely welded up, however, the bonnets are removable.
Chemical, mechanical, and water blast cleaning of the tubes is possible, however you do not
have access to the shell.
You should avoid using Steam cleaning on a fixed tube sheet unit unless the unit has a shell
side expansion joint. The steam will cause the tubes to expand and pull out of the Tube Sheet
causing failure at startup.
DIFFERENTIAL THERMAL EXPANSION
Since the duty of heat exchangers includes the handling of fluids of differing temperature, flow
rate and thermal properties, differential expansion of the metals will take place.
When the terminal temperature difference between the fluids is substantial, over 50-60
degrees, these stresses can become severe, causing shells to become deformed and damage
mounting supports, tubes to deform the tube sheet or tubes to become broken or dislodged
from the tube sheet.
Fixed tube sheet designs are most vulnerable to differential thermal expansion, because there
is no inherent provision to absorb the stresses. One approach in common use is installing an
expansion joint in the shell pipe of such designs. This is a cost effective approach for pipe-size
shells. An expansion joint can also be installed in the tube side of floating head designs, but
Diagram of U-Tube Heat Exchanger
manufacturing costs are much higher. Alternative approaches involve the design of a U-tube
bundle so that each tube can independently expand and contract as needed or by using a rear
floating internal tube sheet design which allows the entire bundle as a unit to expand and
contract. The floating head is typically sealed against the interior of the shell by means of
packing or O-ring designs.
U-tube designs while offering the best answer for differential thermal expansion have some
drawbacks. Individual tubes can be difficult of expensive to replace, especially for interior
tubes. Also, the tube interior cannot be effectively cleaned in the u-bends. Erosion damage is
also frequently seen in the u-bends in high tube side velocity applications. In large diameter
shells, the long length of unsupported tube in the u-bends of outer tubes can lead to vibration
induced damage.
FLOATING HEAD DESIGNS OF HEAD EXCHANGERS
In an effort to reduce thermal stresses and provide a means to remove the tube bundle for
cleaning, several floating rear head designs have been established.
The simplest is a "pull-through" design which allows the tube bundle to be pulled entirely
through the shell for service or replacement. In order to accommodate the rear head bolt
circle, tubes must be removed resulting in a less efficient use of shell size. In addition, the
SOURCE: WWW.WERMAC.ORG/