MK Diamond Baldor Motor User Manual
Page 24
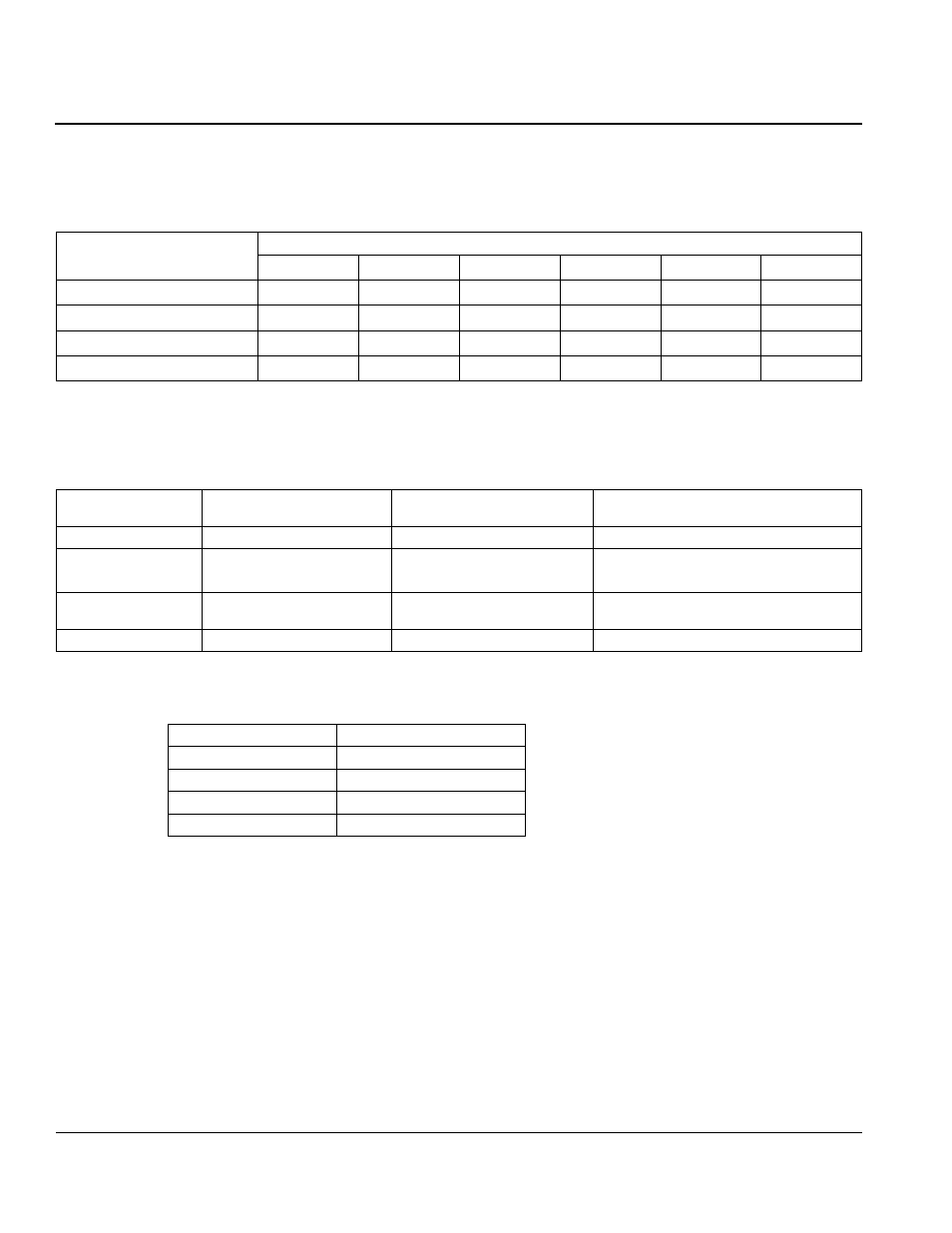
3-2 Maintenance & Troubleshooting
MN408
Relubrication Intervals
Recommended relubrication intervals are shown in Table 3-1. It is important to realize that the recommended
intervals of Table 3-2 are based on average use.
Refer to additional information contained in Tables 3-2, 3-3 and 3-4.
Table 3-1 Relubrication Intervals *
NEMA /
(IEC) Frame Size
Rated Speed - RPM
10000
6000
3600
1800
1200
900
Up to 210 incl. (132)
**
2700 Hrs.
5500 Hrs.
12000 Hrs.
18000 Hrs.
22000 Hrs.
Over 210 to 280 incl. (180)
**
3600 Hrs.
9500 Hrs.
15000 Hrs.
18000 Hrs.
Over 280 to 360 incl. (225)
**
* 2200 Hrs.
7400 Hrs.
12000 Hrs.
15000 Hrs.
Over 360 to 449 incl. (315)
**
*2200 Hrs.
3500 Hrs.
7400 Hrs.
10500 Hrs.
* Relubrication intervals are for ball bearings.
For vertically mounted motors and roller bearings, divide the relubrication interval by 2.
** For motors operating at speeds greater than 3600 RPM, contact Baldor for relubrication
recommendations.
Table 3-2 Service Conditions
Severity of Service
Hours per day of
Operation
Ambient Temperature
Maximum
Atmospheric Contamination
Standard
8
40 ºC
Clean, Little Corrosion
Severe
16 Plus
50 ºC
Moderate dirt, Corrosion
Extreme
16 Plus
>50 ºC* or Class H Insulation
Severe dirt, Abrasive dust, Corrosion,
Heavy Shock or Vibration
Low Temperature
<−29 ºC **
*
Special high temperature grease is recommended (Dow Corning DC44). Note that Dow Corning DC44
grease does not mix with other grease types. Thoroughly clean bearing & cavity before adding grease.
** Special low temperature grease is recommended (Aeroshell 7).
Table 3-3 Relubrication Interval Multiplier
Severity of Service
Multiplier
Standard
1.0
Severe
0.5
Extreme
0.1
Low Temperature
1.0
Some motor designs use different bearings on each motor end. This is normally indicated on the motor
nameplate. In this case, the larger bearing is installed on the motor Drive endplate. For best relubrication
results, only use the appropriate amount of grease for each bearing size (not the same for both).