MK Diamond Baldor Motor User Manual
Page 18
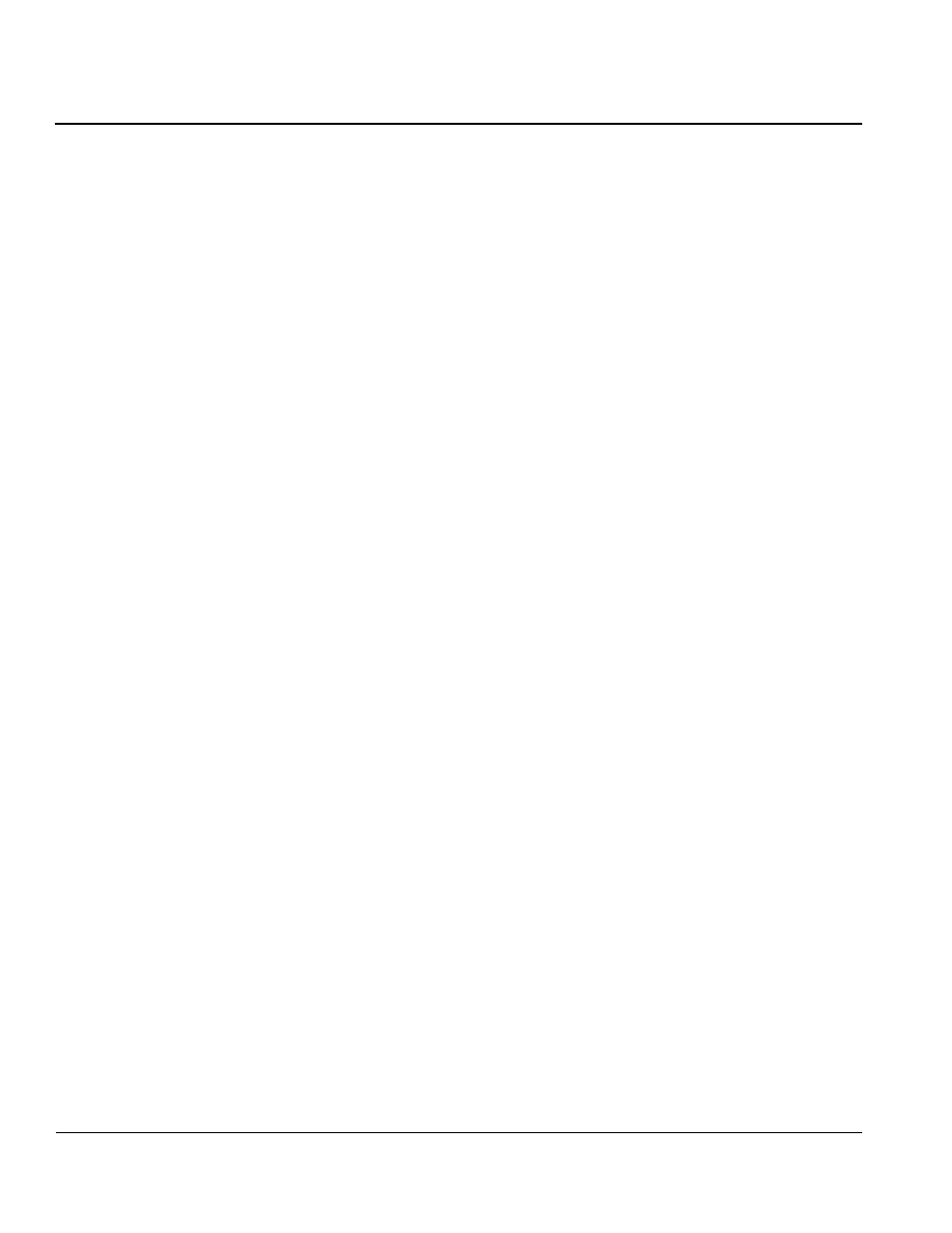
2-8 Installation & Operation
MN428
10. After 1 hour of operation, disconnect power and connect the load to the motor shaft.
Verify all coupling guards and protective devices are installed. Ensure motor is properly ventilated.
11. If motor is totally enclosed fan−cooled or non−ventilated it is recommended that condensation drain plugs,
if present, be removed. These are located in the lower portion of the end−shields. Totally enclosed fan−
cooled “XT” motors are normally equipped with automatic drains which may be left in place as received.
Coupled Start Up
This procedure assumes a coupled start up. Also, that the first time start up procedure was successful.
1. Check the coupling and ensure that all guards and protective devices are installed.
2. Check that the coupling is properly aligned and not binding.
3. The first coupled start up should be with no load. Apply power and verify that the load is not transmitting
excessive vibration back to the motor though the coupling or the foundation.
Vibration should be at an acceptable level.
4. Run for approximately 1 hour with the driven equipment in an unloaded condition.
The equipment can now be loaded and operated within specified limits. Do not exceed the name plate ratings
for amperes for steady continuous loads.
Jogging and Repeated Starts
Repeated starts and/or jogs of induction motors generally reduce the life of the motor winding insulation.
A much greater amount of heat is produced by each acceleration or jog than by the same motor under full
load. If it is necessary to repeatedly start or jog the motor, it is advisable to check the application with your
local Baldor distributor or Baldor Service Center.
Heating - Duty rating and maximum ambient temperature are stated on the motor name plate.
Do not exceed these values. If there is any question regarding safe operation, contact your local Baldor
distributor or Baldor Service Center.
Hazardous Locations
Hazardous locations are those where there is a risk of ignition or explosion due to the presence of combustible
gases, vapors, dust, fibers or flyings.
Selection
Facilities requiring special equipment for hazardous locations are typically classified in accordance with
local requirements. In the US market, guidance is provided by the National Electric Code. In international
hazardous location areas, guidance for gas / vapor / mist classification is given in IEC60079−14, or for dust in
IEC61241−14. This classification process lets the installer know what equipment is suitable for installation in
that environment, and identifies what the maximum safe temperature or temperature class is required.
It is the customer or users responsibility to determine the area classification and select proper equipment.
Areas are classified with respect to risk and exposure to the hazard. In the US market, areas are typically
classified as follows Class, Division, Group and Temperature Class. In some newer installations in the US and
in most international markets, areas are classified in Zones.
Protection Concepts
Class I Division 1 / Zone 1 [Equipment Group I (mining) or II (surface), Equipment Protection Level (EPL)
Gb, Mb ]
Baldor offers a range of motors suitable for installation in a Division 1 or Zone 1 environment.
These motors are known as explosion proof or flameproof.
Motors that are explosion proof or flameproof use specially machined flameproof joints between the end bell or
bracket and the frame, as well as along the rotating shaft and at connection box covers and entries.
The fit of these flameproof joints are designed to contain the combustion or quench the flame of an explosive
gas atmosphere prior to it exiting the motor. These flameproof joints have lengths and widths selected and
tested based on the gas group present in the atmosphere. Baldor•Reliance motors are typically designed to
meet Class I (Division 1) Group C and D (explosion proof) or Ex d IIB (flameproof).
An application note regarding equipment applied in accordance with the US National Electric Code (NFPA
70−2008) − according to Article 500.8(C) Marking, sub clause (2) in the fine print note, it is noted that
Equipment not marked to indicate a division is suitable for both Division 1 and Division 2 locations.
These motors are not gas tight. To the contrary, this protection concept assumes that due to the normal
heating and cooling cycle of motor operation that any gas present will be drawn into the motor. Since
flameproof or explosion proof motors are designed to contain the combustion and extinguish any flame
transmission, for this protection concept, only external surface temperatures are of concern. Thermal limiting
devices such as thermostats, thermistors or RTDs may be provided on these motors to limit the external
surface temperature during overload conditions.