MK Diamond Baldor Motor User Manual
Page 19
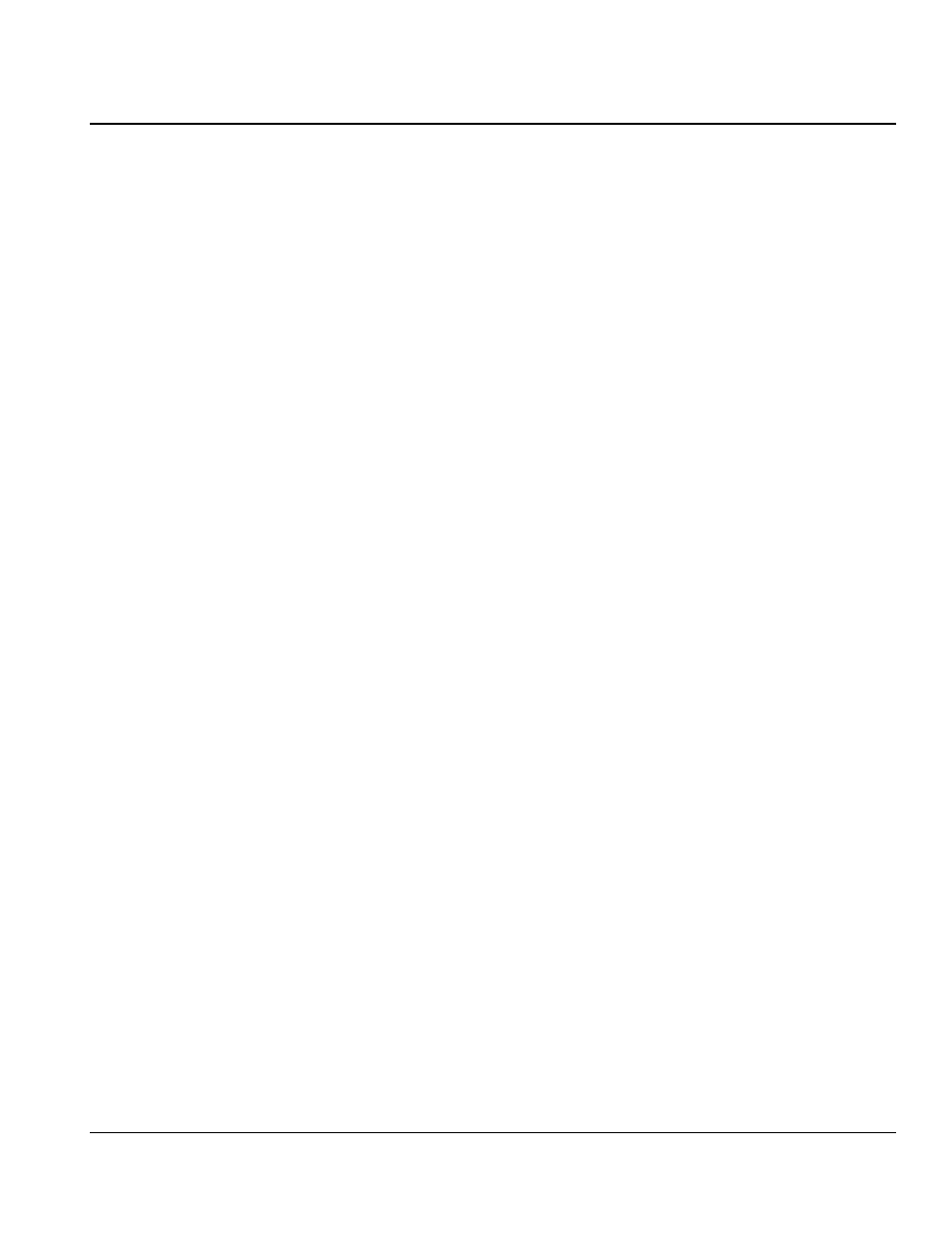
Installation & Operation 2-9
MN428
If thermostats are provided as a condition of certification, it is the installer’s responsibility to make sure that
these devices are properly connected to a suitable switching device. The ATEX directive requires that motor
shutdown on thermal trip be accomplished without an intermediate software command. Where intermediate
circuitry is involved the circuit shall fall within the scope of a safety, controlling and regulating device as defined
in article 1(2) of European Directive 94/9/EC, and shall be covered by an appropriate EC Type Examination
Certificate.
Flameproof motors, internationally referred to as Ex d use a protection concept similar to that used in Class
I Division 1 motors, with minor differences in the flameproof joints and cable entry designs. Flameproof and
explosion proof motors are both type tested. Representative motors are connected to a reference gas and
ignited in laboratory conditions to verify that the flame is not transmitted outside the motor enclosure and to
determine the maximum internal pressure encountered.
Explosion proof and Flame proof motors shipped without a conduit box require use of a certified box of
suitable dimensions and that is appropriate for the classification. Openings in connection boxes must be
closed with suitably certified and dimensioned device.
Hazardous location motors equipped with NPT pipe nipples are designed and built such that the pipe nipple is
securely attached to the motor frame. This is accomplished externally by interference between the threads as
well as tack welding. The conduit box is securely attached to the pipe nipple at the factory per:
1. Standard Commercial NPT & Explosion Proof IEC/ATEX parts : L-1 gauging notch +/- 1 thread (ref.
ANSI/ASME B1.20.1 and Clarification Sheet ExNB/98/06/010/CS) Note: Clarification Sheet
ExNB/98/06/010/CS provides inspection criteria to meet (6 threads minimum per engineering part drawing
for ATEX parts).
2. Explosion Proof UL conduit boxes & MSHA parts: L-1 gauging notch “+1 min to + 3 1/2 max threads.
Note: Provides inspection criteria to meet (5 threads minimum per engineering part drawing for MSHA parts
and meet UL 1203 requirement for L-1 gauging notch flush to + 3 1/2 max threads).
This allows the end user to position the conduit box according to the application then secure when in place.
For obvious reasons having the conduit box snug prior to affixing to the pipe nipple is preferable. However, the
guidance in numbers 1 and 2 above can be used in determining thread engagement.
Note: In the United States most non-mining applications have rigid conduit for cabling, therefore not tack
welding the conduit box to the pipe nipple is standard. In markets outside the United States, flexible
conduit/cabling are common and end users should take note to secure the conduit box to the pipe nipple
once in position. Further, the flexible leads should be secured to inhibit forces acting on the conduit box.
Class I Division 2 / Zone 2 Ex nA, [Equipment Protection Level (EPL) Gc ]
This protection concept relies on having no sources of ignition present such as arcing parts or hot surfaces.
For this protection concept, internal temperatures as well as external temperatures are considered. In many
cases, the internal temperatures are higher than the external temperatures and therefore become the limiting
factor in determination of temperature code designation. In these applications, it is very important to use a
motor that has been evaluated thermally for use with an inverter or converter, if variable speed operation is
desired. Thermostats used for Class I Division 2 and Ex nA motors are used to protect the motor only. For
motors using flying lead construction, it is important to use connection lugs and insulate with heat shrink
tubing or a double wrap of insulation grade electrical tape to avoid the risk of spark or ignition.
Class II Division 1 / Zone 21 [Equipment Group III, Equipment Protection Level (EPL) Db ]
This area classification is one where the risk of ignitable concentrations of dust is present at all or some of the
time. The protection concepts used for Class II Division 1 is similar to flamepath, except with additional dust
exclusion paths designed for the rotating shaft. In the international designations, this concept is referred to as
dust ignition proof or Ex tD. External surface temperature remains the limiting factor. Thermal limiting devices
such as thermostats, thermistors or RTDs may be provided on these motors to limit the external surface
temperature during overload conditions. If thermostats are provided as a condition of certification, it is the
installer’s responsibility to make sure that these devices are properly connected to a suitable switching device.
Note: In the North American area classification system, Class III exists for fibers and flyings.
In the IEC designation, both dusts and flyings are absorbed into Group III.
Class II Division 2 / Zone 22 [Equipment Group III, Equipment Protection Level (EPL) Dc ]
This area classification is one where the risk of exposure to ignitable concentrations of dust are not likely
to occur under normal operating conditions and relies heavily on the housekeeping practices within the
installation.
Sine Wave Power Operation for Division 1 or 2 and Zone 1 or 2 and Zone 21 or 22 Hazardous Location.
These motors are designed to operate at or below the maximum surface temperature (or T−Code) stated
on the nameplate. Failure to operate the motor properly can cause this maximum surface temperature to
be exceeded. If applied in a Division 1 or 2 / Zone 1 or 2 and Zone 21 or 22 environment, this excessive
temperature may cause ignition of hazardous materials. Operating the motor at any of the following
conditions can cause the marked surface temperature to be exceeded.