Description – JUMO 705001 mTRON T - Central Processing Unit Data Sheet User Manual
Page 2
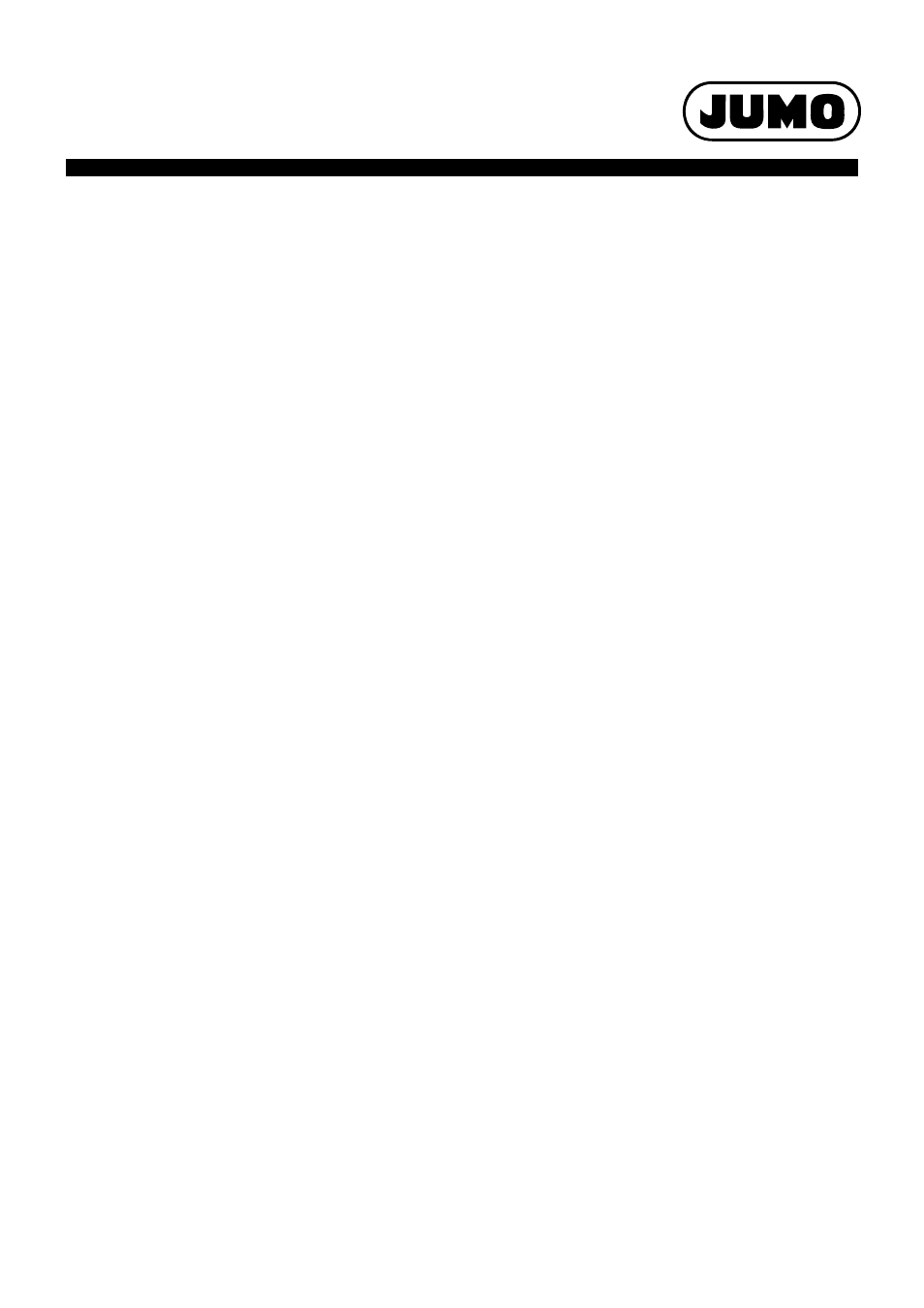
JUMO GmbH & Co. KG
Delivery address: Mackenrodtstraße 14
36039 Fulda, Germany
Postal address:
36035 Fulda, Germany
Phone:
+49 661 6003-0
Fax:
+49 661 6003-607
E-mail:
Internet:
www.jumo.net
JUMO Instrument Co. Ltd.
JUMO House
Temple Bank, Riverway
Harlow, Essex CM20 2DY, UK
Phone: +44 1279 635533
Fax:
+44 1279 635262
E-mail:
Internet: www.jumo.co.uk
JUMO Process Control, Inc.
6733 Myers Road
East Syracuse, NY 13057, USA
Phone: 315-437-5866
1-800-554-5866
Fax:
315-437-5860
E-mail:
Internet: www.jumousa.com
2014-08-22/00529105
Data Sheet 705001
Page 2/10
Description
Setup program
The setup program is installed on a PC and
connected to the base unit (central processing
unit) or the multifunction panel via USB or LAN
interface. That way the entire system can be
comfortably configured, parameterized, and
operated.
The setup data is transmitted to the up to 30
connected input/output modules (system bus).
General setup data and functions:
• Hardware configuration of the entire system
• Selection and editing of the operating lan-
guages
• Configuration and parameterization of the
input and output modules
• Configuration of the central processing unit
and the multifunction panel
• Configuration and programming of the PLC
• Program editor for 99 programs
• Configuration of the 9 program generators
• Configuration of the recording and the batch
reporting
• Editor for customer-specific process images
Limit value monitoring
With the limit value monitoring one input vari-
able can be monitored compared to a fixed
limit value or a different variable. 64 limit
values can be monitored in this way and for
each limit value monitoring eight different
alarm functions are available. The configura-
tion is carried out in the setup program or with
the multifunction panel.
Even extensive functions can be realized due
to additional parameters such as position and
value of the switching differential, switch ON/
OFF delay, pulse function, acknowledgement
type, and startup alarm suppression. The
startup alarm suppression can, for example,
be used to prevent the limit value monitoring
function to be tripped during the process start-
up phase.
Event list
The event list contains all events that occurred
in the system including date and time. This in-
cludes system messages (configuration
changes of a module, mains OFF/ON of the
central processing unit), general events
(sending an e-mail), malfunctions (module er-
rors, communication malfunction), alarms,
and collective alarms.
The list contains the last 150 events and can
be invoked as text in the set language via web
server and on the multifunction panel. In the
event of a mains failure, the event list remains
saved.
Event texts
The setup program can be used to define up
to 250 event texts, each with a length of up to
31 characters. This way, customized event
messages can be created.
Interfaces
The following interfaces are available:
• USB device to connect a PC (e.g. for the
setup program)
• LAN (Ethernet)
(HTTP or Modbus/TCP as master/slave)
• Serial RS232
(Modbus RTU as master/slave)
• Serial RS422/485
(Modbus RTU as master/slave)
• PROFIBUS-DP as slave (as of system ver-
sion 02)
• Bus Out (at the front) to connect a router
module or multifunction panel via network
cable
External signals
External input signals (variables) can be trans-
mitted to the system via the fieldbus interfaces
and the LAN interface (Modbus/TCP) in addi-
tion to the internal input signals. As a result, up
to 64 analog variables, up to 64 integer vari-
ables, and up to 64 digital variables as well as
up to 9 text variables are available.
Web server
The central processing unit serves as web
server and thereby offers the option to com-
fortably access the system via LAN using a PC
(web browser). This access method provides
the following information:
• Process values
• Event list
Access can be protected by a password.
Alarm transmission by e-mail
Alerts can be sent by e-mail to three addres-
ses simultaneously via a mail server. Up to five
alarm texts can be configured; sending is con-
trolled via binary signals.
If special e-mail addresses that forward to mo-
bile phones (text messaging) or fax machines
are provided in the company network, alerts
can also be transmitted using these communi-
cation channels.
Program generator
Nine independent program generators are
available as an option so that nine programs
can run asynchronously and independently
from each other. A total of 99 programs can be
managed in a program pool.
The program editor, which is part of the setup
program and the multifunction panel, can be
used to create a program.
Each program can consist of up to three pro-
gram channels with four setpoint values and
16 control contacts. Up to 99 program sections
are possible. A tolerance band monitoring can
be set for the first set point value of each pro-
gram channel.
A program can be started, stopped, and
aborted by an action on the multifunction
panel, a binary signal, or via the PLC. Toggling
between the program sections is possible as
well. A program can also be started by setting
default dates and times. The individual pro-
gram channels of a program are synchronous-
ly started.
The program is completed when all program
channels of the program are completed. If a
program channel is prematurely completed, its
setpoint values and control contacts are set to
a defined value (basic status).
For manual mode, separate setpoint values
and control contacts can be defined per pro-
gram channel (basic status). The setpoint
values can be adjusted through the multifunc-
tion panel.
The behavior after a mains interruption can be
configured (e.g. program abort, continued run,
or continuation/abort via multifunction panel).
Program generator with process
steps (as of system version 02)
The nine program generators support the use
of up to 100 process steps. In every process
step the allowed setpoint values and control
contacts are selected and the time limits of a
program section are defined. This assignment
is normally done by the plant manufacturer be-
cause special knowledge of the plant is re-
quired.
While entering a program using the program
editor, a certain process step is assigned to
each program section. As a result, the specifi-
cations defined with the process step are rele-
vant for the dedicated program section. This
means: only the allowed setpoint values and
control contacts can be used and the section
run time has to be within the time limits.
PLC function
The PLC function (option) is a fully adequate
PLC which can be used to read all inputs and
to write to all outputs of the modules in the
system. A library with predefined function
modules and data types including their docu-
mentation is available to the user.
For programming a control application, all
editors defined in the IEC 61131-3 standard
are provided:
• Structured text (ST)
• Sequential function chart (SFC)
• Continuous function chart (CFC)
• Function block diagram (FBD)
• Ladder diagram (LD)
• Instruction list (IL)
Furthermore, a large number of functions are
implemented which can be used to quickly and
efficiently debug, test, and start up the applica-
tion.
In addition, the user has the following func-
tions and possibilities when using the PLC:
• Generation of events saved in the event list
of the central processing unit
• Configuration of all system modules
• Process mask control of the multifunction
panel
The PLC programming system is started from
the setup program. Information about the
system hardware (modules) is automatically
loaded into the PLC programming system.
The user can assign machine specific names